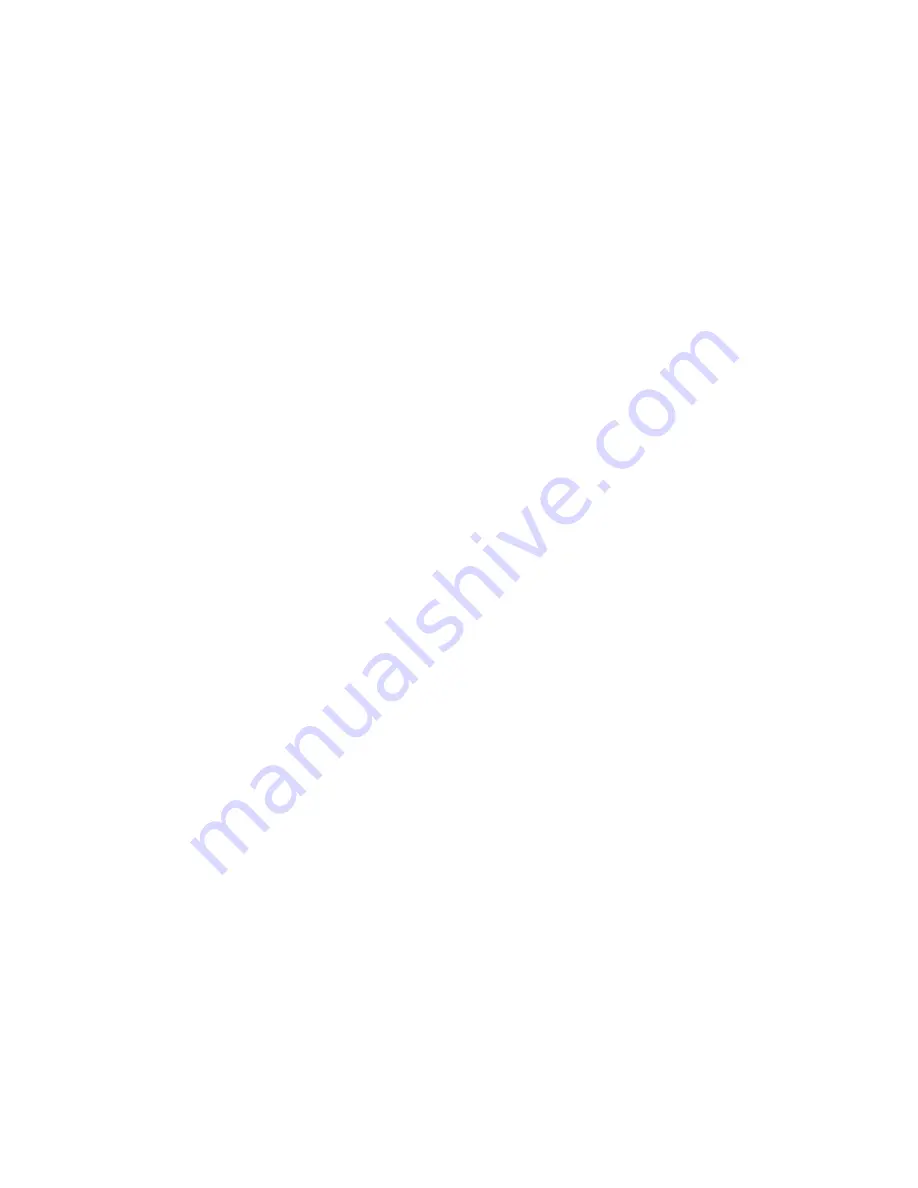
19
5. BIN CONTROL
This machine uses a lever-actuated proximity switch (mechanical bin control) to control
the ice level in the storage bin. No adjustment is required.
[a] EXPLANATION OF OPERATION
The bin control is connected to the K1 connector (pins 4 & 5) on the control board.
When the bin control is calling for ice (proximity switch closed; "POWER OK" LED on),
the control board continues icemaking operations. When the bin control is activated
in the bin full position (proximity switch open; "POWER OK" LED flashing), the control
board drains and shuts down the unit. However, to prevent incomplete batches of ice
from forming on the evaporator, the control board will only shut down the machine
during the freeze cycle before the five minute timer expires. The five minute timer starts
counting down when the thermistor temperature reaches 2°C. If, during the freeze cycle,
ice pushes in the lever after the five minute timer expires, the control board will allow the
machine to complete the freeze cycle and the following harvest cycle before shutting
down the machine.
[b] BIN CONTROL CHECK PROCEDURE
1) Clear any ice away from the bin control.
2) Make sure the control switch is in the "ICE" position.
3) Check that the "POWER OK" LED on the control board is on.
4) Activate the bin control actuator (press the actuator in). Check that the "POWER OK"
LED flashes.
5) Disconnect the bin control at the 2-pin connector attached to the black wires coming
from the K1 connector (pins 4 & 5) on the control board.
6) Check for continuity across the bin control leads. When calling for ice, the bin control
proximity switch should be closed. If open, replace the bin control. Activate the bin
control actuator (press the actuator in), check for continuity across the bin control
leads. The bin control proximity switch should be open. If closed, replace the bin
control.
7) Reconnect the 2-pin connector. Allow the machine to cycle into the freeze cycle. In
the first 5 minutes of the freeze cycle, activate the bin control actuator (press the
actuator in). The "POWER OK" LED should flash and the machine should turn off. If
not, replace the control board.