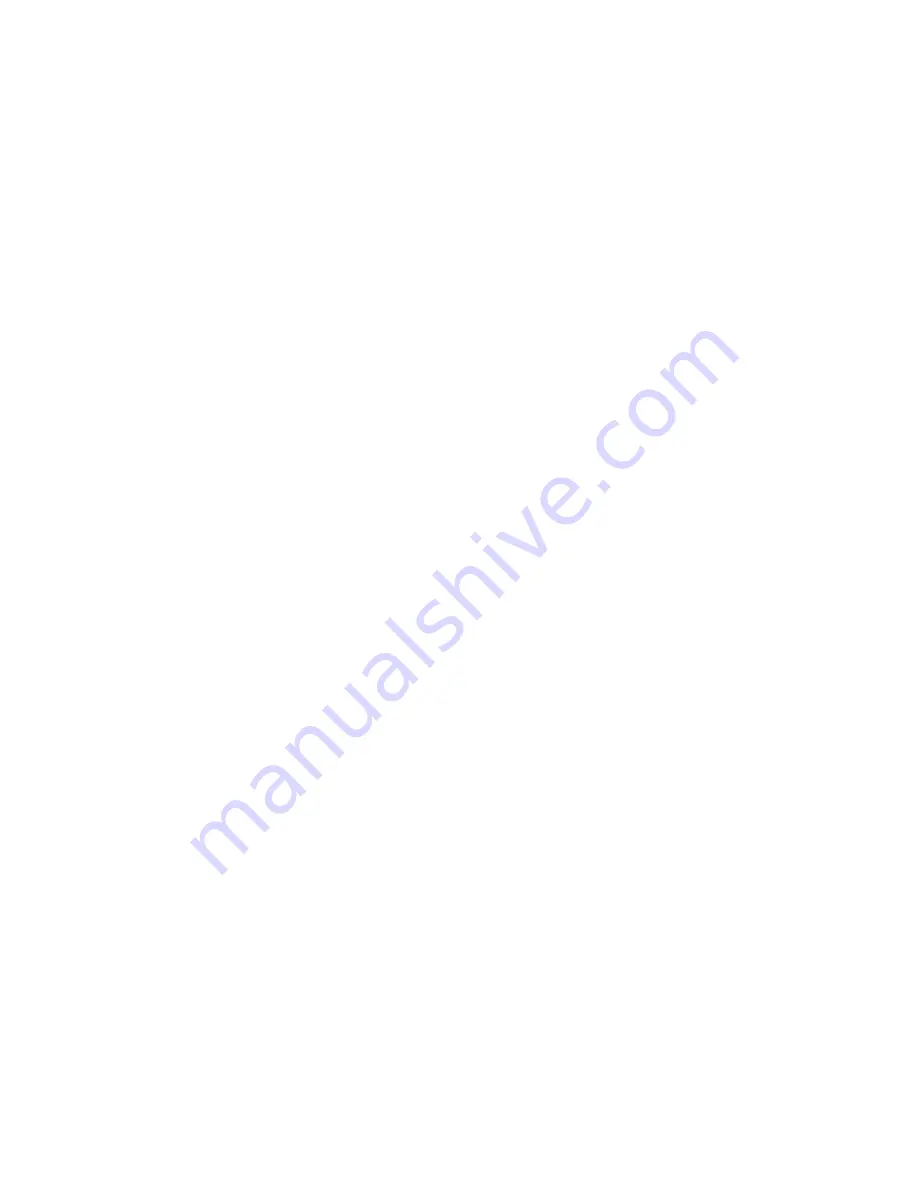
40
[c] Water Plate Switch
1) Remove the screws and nuts fixing the water plate switch to the mechanism base.
[d] Cam Switch
1) Unscrew and remove the cam switch from the switch bracket.
[e] Water Tank Assembly
1) Remove the flange nuts fixing the bearing plate to the mechanism base.
2) Pull out the water tank assembly with the bearing plate from the bottom.
3) Remove the bearing plate and spring from the water tank assembly.
[f] Lower Evaporator
1) Remove the flange nuts, spring washers, washers, evaporator screws and plastic
washers under the water plate to release the lower evaporator from the water plate.
[g] Evaporator Base
1) Remove the screws fixing the evaporator base on the water plate.
[h] Pump Motor
1) Remove the screws fixing the pump motor to the side of the water plate.
2) Remove the discharge and suction hoses.
[i] Water Tank
1) Remove screws fixing the water tank to the water plate.
Summary of Contents for IM-50BAA-Q
Page 52: ...51 C Wiring Diagram ...