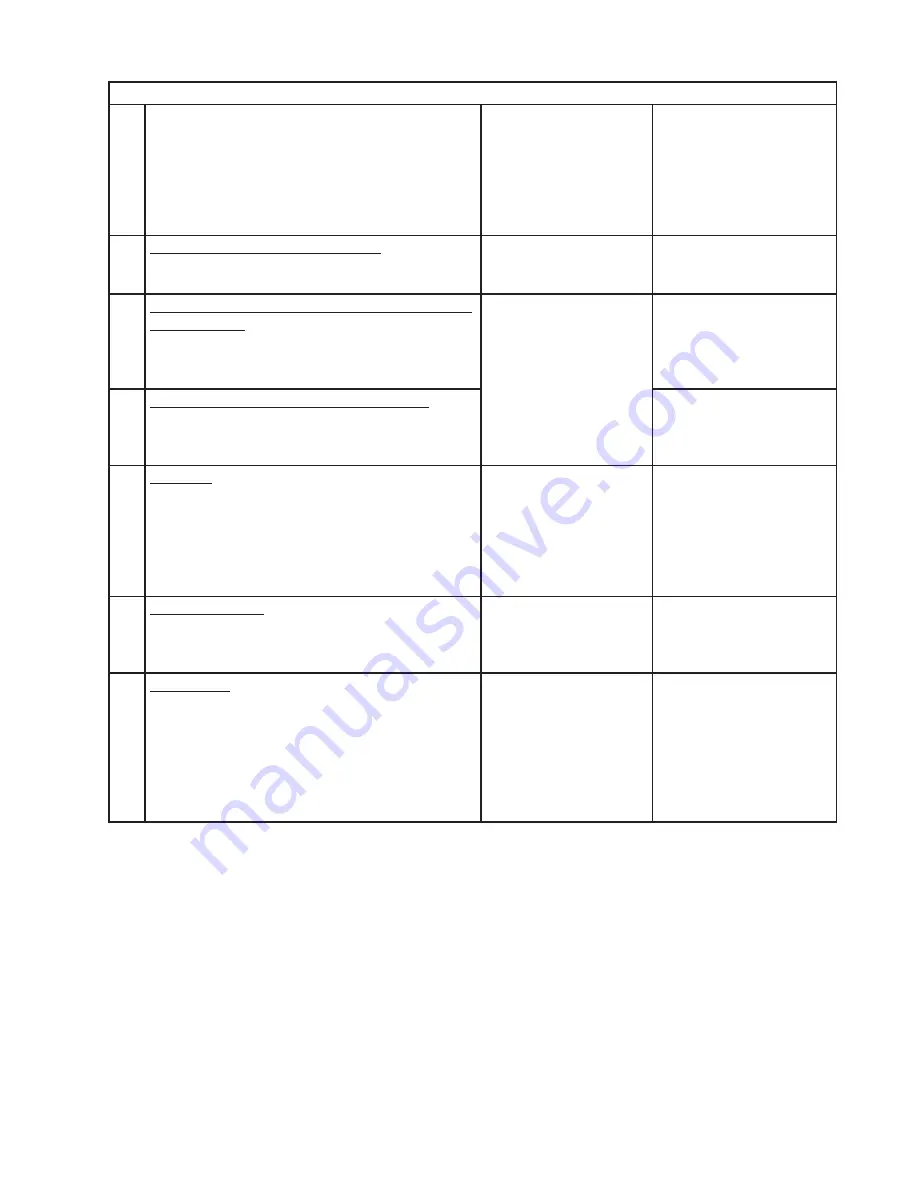
29
Control Board Information Display
No. Item
Description
History Cleared by
Pressing and Holding
SERVICE 1 and
SERVICE 2 Buttons
Simultaneously for
5 Sec. when Item Value
is Displayed?
h1
Last Completed Freeze Cycle Time
Freeze cycles interrupted by bin control shutdown
or the "RESET" button are not recorded.
0 to 99 min.
Yes
h2
Number of Completed Freeze Cycles Since Last
Counter Reset
Counter updates every 10 freeze cycles. Freeze
cycles interrupted by bin control shutdown or the
"RESET" button are not recorded.
Displays up to 999,999
cycles. Displays two
digits at a time. For
example, 655,350 cycles
display as follows:
65>off>53>off>50>off>- -
(repeat)
Yes
h3
Total Number of Completed Freeze Cycles
Counter updates every 10 freeze cycles. Freeze
cycles interrupted by bin control shutdown or the
"RESET" button are not recorded.
No
h4
Error Log
Displays up to 5 errors with the most recent error
first. For error details, see "III.F. Error Codes."
For example, E5 (most
recent), E4, E3, E2, E1
(least recent of up to 5
errors) displays as fol-
lows:
E5>off>E4>off>E3>off>E
2>off>E1>off>- - (repeat)
Yes
h5
Firmware Version
Displays control board's firmware version.
For example, version
1.0A, displays as follows:
01.>off>0A>off>- - (re-
peat)
No
h6
Model Code
The model code puts all settings for a given
model to the correct default settings. The model
code setting mode should only be used when the
control board has been changed, the model code
is incorrect, or to reset all settings to the default.
For details about the model code setting mode,
see "III.E. Control Board Model Code Setting."
Displays two-character
model code.
"00" to "FF"
No