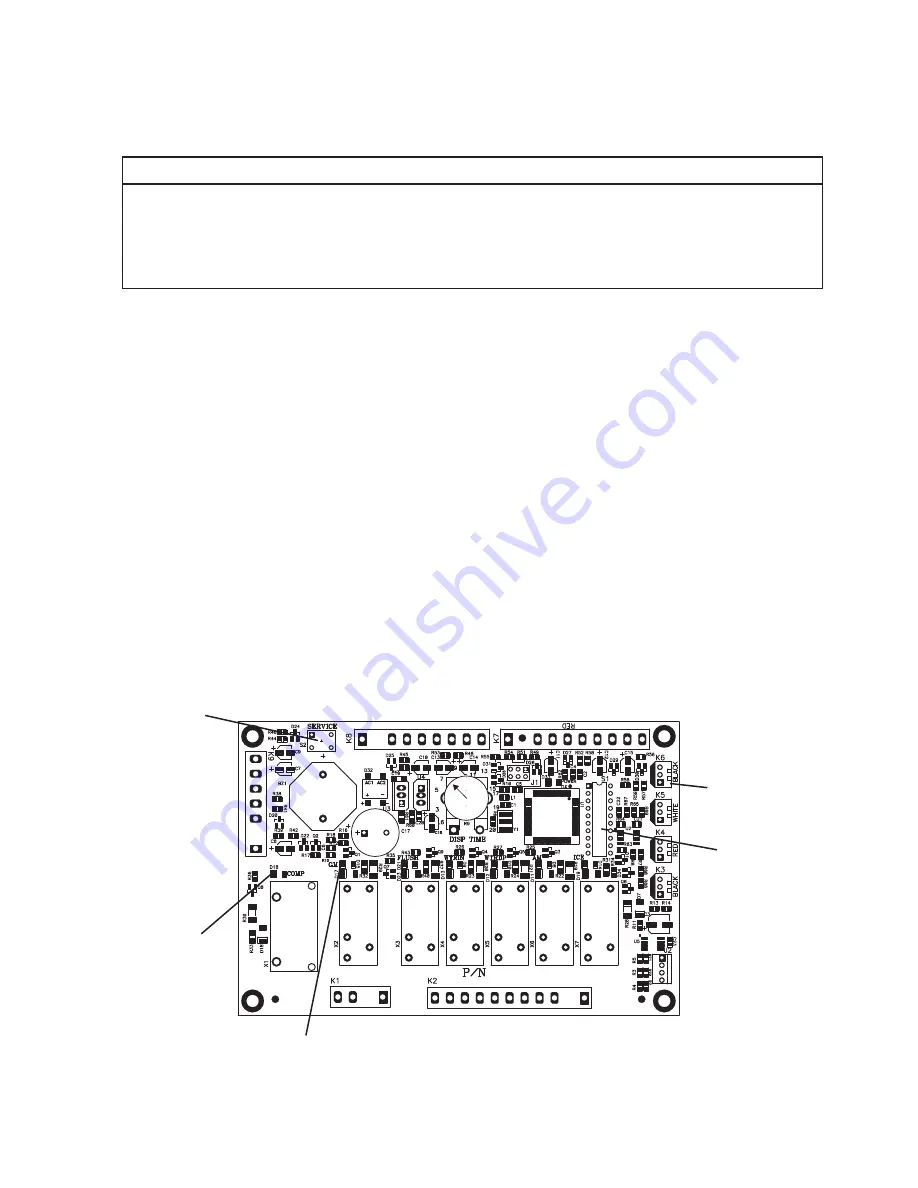
37
K. Bin Control Check
An infrared sensor is used as the primary bin control to control the level of ice in the
dispenser unit/ice storage bin. A mechanical bin control is used as a backup bin control.
IMPORTANT
• Make sure the icemaker has been installed as outlined in this manual and that the
water supply is on.
• Make sure S1 Dip Switch 7 is in the "ON" position. This allows the control board to
monitor the infrared sensor.
1. Infrared Sensor Check
1) If not already removed, remove the front panel, top panel, and control box cover.
2) Make sure the power switch is in the "OFF" position and that the power supply is off.
3) Confirm that control board S1 dip switch 1, 2, and 3 are in the proper position for your
application. "See II.K.3. Infrared Sensor Shutdown Delay."
4) Move the control switch to the "ICE" position, then move the power switch to the "ON"
position.
5) Turn on the power supply to start the automatic icemaking process. Confirm the green
LED on the infrared sensor turns on. This LED confirms 20VDC power to the sensor.
6) Make sure the "GM" LED on the control board is on. See Fig. 15. There is a delay of
at least 30 seconds before the "GM" LED turns on after power-up. After the "GM" LED
turns on, press the "SERVICE" button on the control board to bypass the 5-minute
compressor delay.
WARNING! Risk of electric shock. Care should be taken not to
touch live terminals.
Confirm the "COMP" LED turns on.
"SERVICE"
Button
S1 Dip Switch
"GM" LED
"COMP" LED
K
6 - Connector for
Infrared Sensor
Fig. 15
2A9093-01