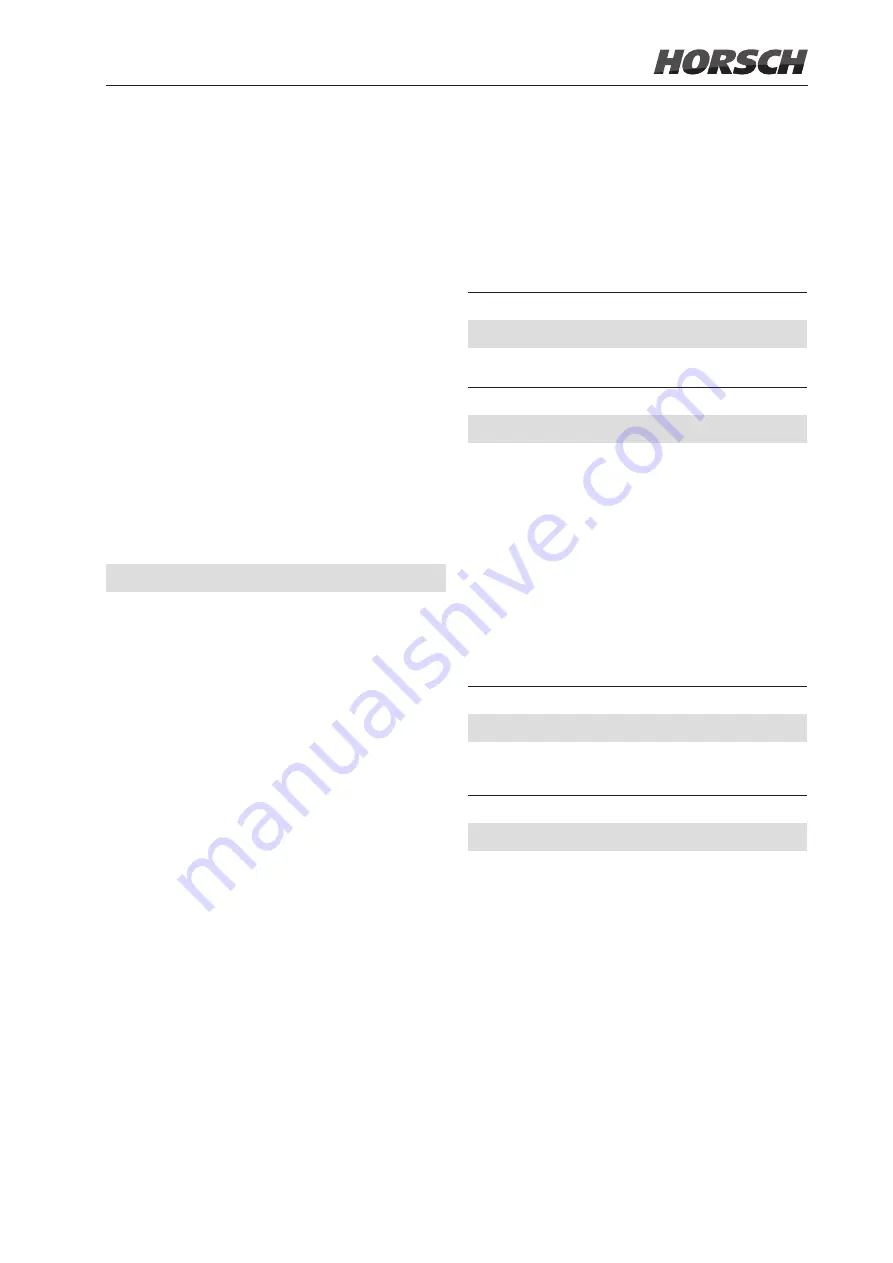
Calculating filling / refill
quantities
Example 1: Filling quantities
The following is known:
Rated tank volume 1000 l
Residual quantity in tank 0 l
Required water 400 l/ha
Required amount of chemical per ha
Product A 1.5 kg
Product B 1.0 l
Question:
How many l of water, how many kg or product
A and how many l of product B do you have to
fill in, if the area to be treated is 2.5 ha?
Calculation formula and solution
Component [quantity/ha] x area [ha]
= required quantity [l] or [kg]
Water: 400 l/ha x 2.5 ha = 1000 l
Product A: 1.5 kg/ha x 2.5 ha = 3.75 kg
Product B: 1.0 l/ha x 2.5 ha = 2.5 l
Example 2: Addition of product, area
The following is known:
Rated tank volume 1000 l
Residual quantity in tank 200 l
Required water 500 l/ha
Recommended concentration 0.15 % l/l or kg/l
Question 1:
How many l or kg preparation must be metered
for one container filling?
Calculation formula and answer to
question 1:
Water refill quantity [l] x concentration [%]
100
= product addition [l] or [kg]
(1000-2000) [l] x 0.15 [% l/l or kg/l]
100
= 1.2 [l] or [kg]
Question 2:
How large is the area to be treated in ha, which
can be treated with one filling, if the tank can
be sprayed down to a residual quantity of 20 l?
Calculation formula and answer to
question 2:
Available amount of chemical [l] – Residual
quantity [l]
Required water [l/ha]
= area [ha]
1000 [l] (rated volume) – 20 [l] (residual quantity)
500 [l/ha] (required water)
= 1.96 [ha]
33
Summary of Contents for Shuttle 8.000 L
Page 2: ......
Page 5: ......
Page 7: ...3...
Page 19: ...Fill the hand washing tank only with clear water 04002628 15...
Page 20: ...Position of safety stickers depending on equipment 16...
Page 64: ......