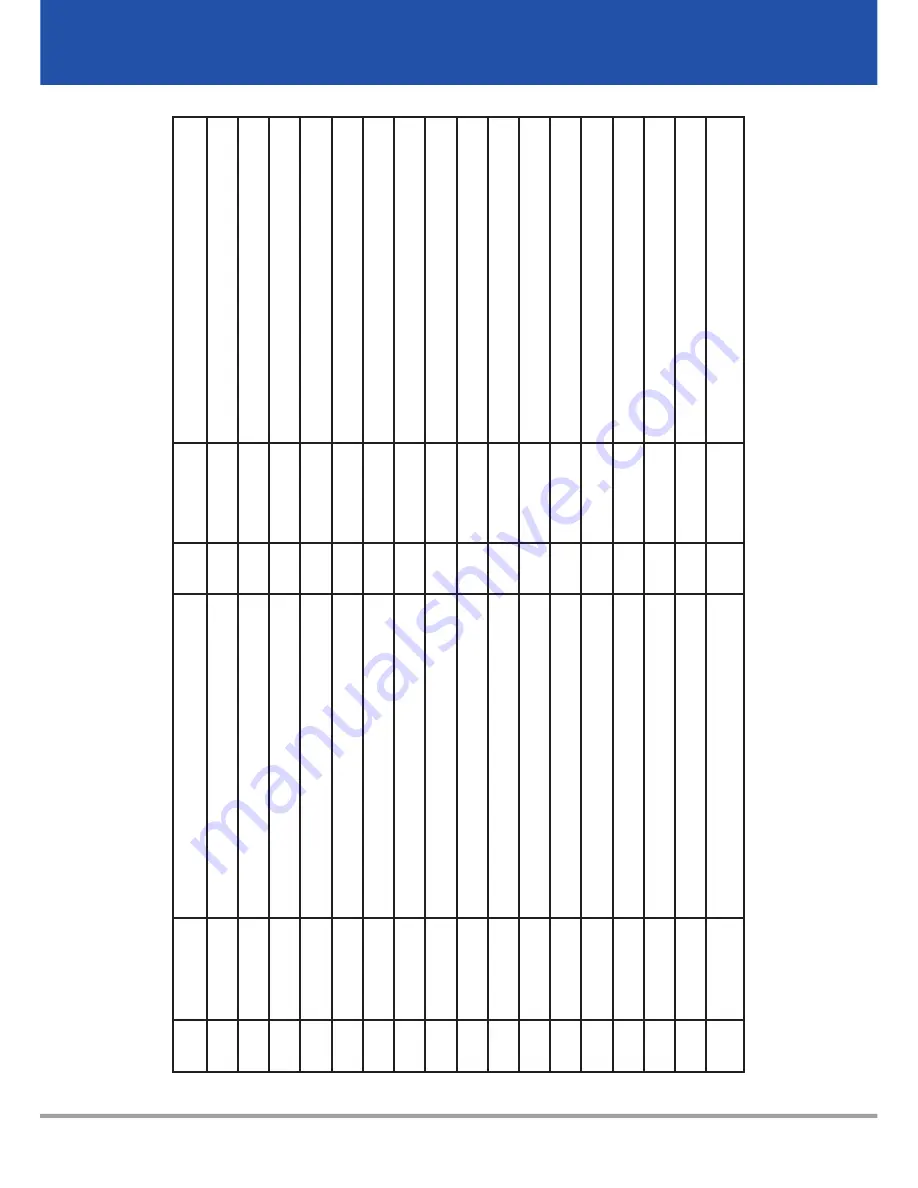
HORNER - SUREGRIP INSTRUCTION MANUAL
SUREGRIP - PARTS LIST
1
H19-200
Left Hand Fork
19
H19-218
Safety Screw
2
H19-201
Right Hand Fork
20
H19-219
Handle
3
H19-202
Fork Retaining Spring
21
H19-220
Oil Hole Screw & Washer
4
H19-203
Fork Retainer Screw
22
H19-221
Oil Hole Washer
5
H19-204
Fulcrum Cup
23
H19-222
Crank Roller
6
H19-205
Tension Pin Cup
24
H19-223
Crank Spindle
7
H19-206
Tension Pin Retaining Spring
25
H19-224
Main Bush
8
H19-207
Bare Fork Body
26
H19-225
Internal O-Ring
9
H19-208
Complete Fork Body
27
H19-226
External O-Ring
10
H19-209
Comb Screw (Knucklesaver)
28
H19-227
Back End Guard
11
H19-210
Fulcrum Post Nut
29
H19-228
Joint Spring
12
H19-211
Fulcrum Post
30
H19-229
Joint Cap
13
H19-212
Threaded Bush
31
H19-230
Back Joint Short Half
14
H19-213
Tension Circlip
32
H19-231
Cog
15
H19-214
Tension Pin
33
H19-232
Back Joint Long Half
16
H19-215
Sliding Sleeve
34
H19-233
Worm Back Spindle
17
H19-216
Tension Knob
35
H19-234
Pin Back Spindle
18
H19-217
Rubber Bung
36
H19-235
Short Spindle Pin
13