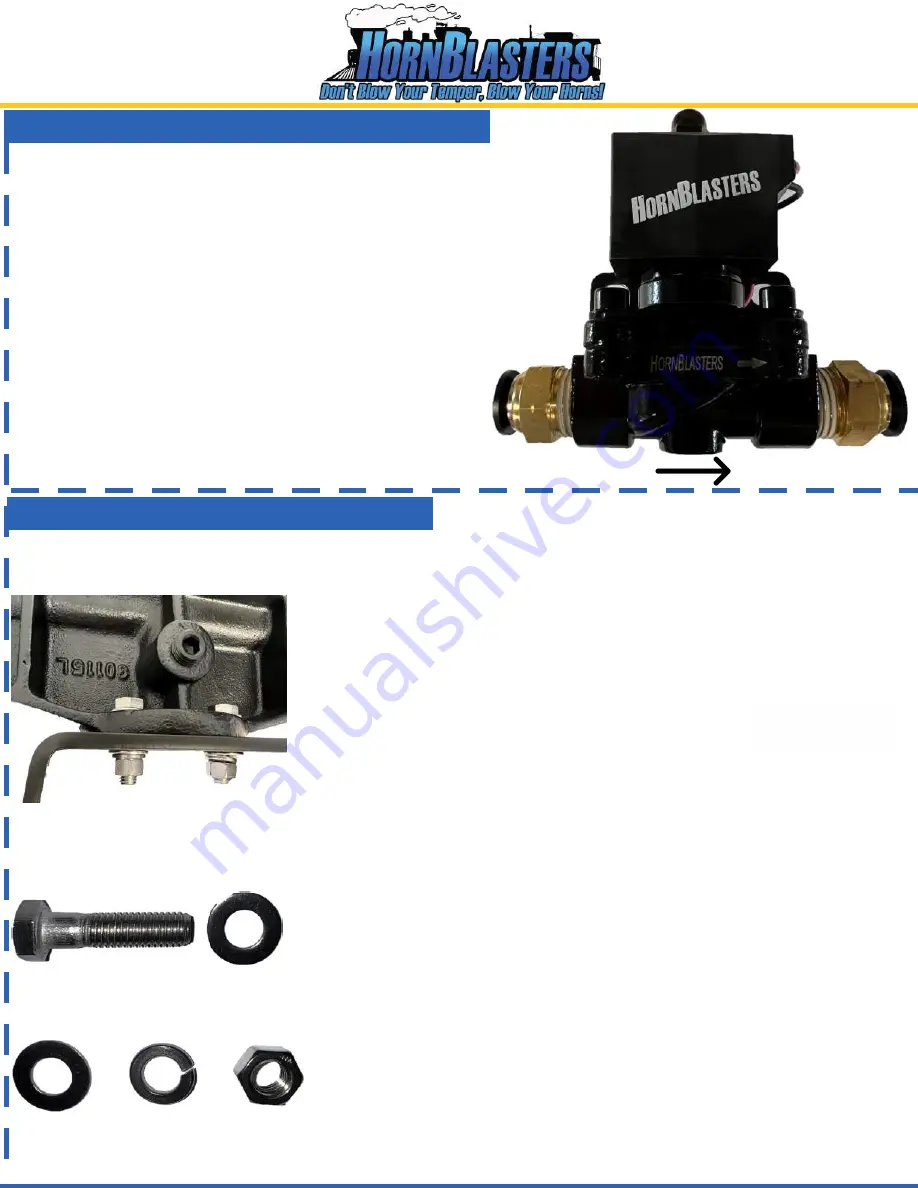
Plumbing the Valve to the Tank (Continued)
•
•
•
www.hornblasters.com
Securing the horn to the Mounting Bracket
L
o
cate the solenoid valve for your horns. Take note of
the arrow on the side of the body of the valve. This
arrow must point TOWARDS your horns. If the valve
is mounted with the arrow pointing towards the tank, the
valve will not hold air pressure and leak
instantly
.
Locate
two of the four 1/2" NPT x 1/2" PTC fittings that
came with your kit.
Plumb
each
fitting into the air valve.
Use a wrench to tighten the fitting snug. Be careful not to
apply pressure to the plastic portion of the fitting. It can
break.
Grab the 1/2" line that we plumbed into the tank and route
it up to this valve. Insert the line into the 1/2" fitting on the
inlet portion of the valve.
Locate the
horn mounting bracket as we need to secure the horn to this mount before it can be plumbed to the
solenoid valve. The image below shows what the hardware looks like when assembled.
Start by positioning the horn manifold over the bracket so that the four
mounting holes line up. You will need the following hardware:
•
4x - 3/8" Threaded Bolt
•
8x - 3/8" Flat Washer
•
4x - 3/8" Split Lock Washer
•
4x 3/8" Nut
Start by feeding a bolt through one of the flat washers (figure 1). Move
the washer all the way up to the head of the bolt. Route the bolt/washer
combo down through the horn manifold and horn bracket.
On the bottom of the bracket, feed a flat washer and split lock washer
over the bolt thread. Make sure the split lock washer is on the bottom of
the stack (figure 2).
Thread the nut onto the bolt and use a 9/16" wrench to tighten it up. You
will need another wrench on the bolt head to tighten the nut up
later
.
The split lock washer will compressor when full tightened. Repeat this
process for all four mounting points to secure the horn to the mounting
bracket.
Leave these bolts loose for now, as we still need to plumb the
inlet fitting into the horn. Leaving the bracket loose makes the next step
much easier.
Figure 1
Figure 2
Flat washer - Split Washer - Nut
Page 11
Summary of Contents for NATHAN AIRCHIME
Page 15: ...Quad Compressor Wiring Diagram Page15 ...
Page 17: ...Page17 ...