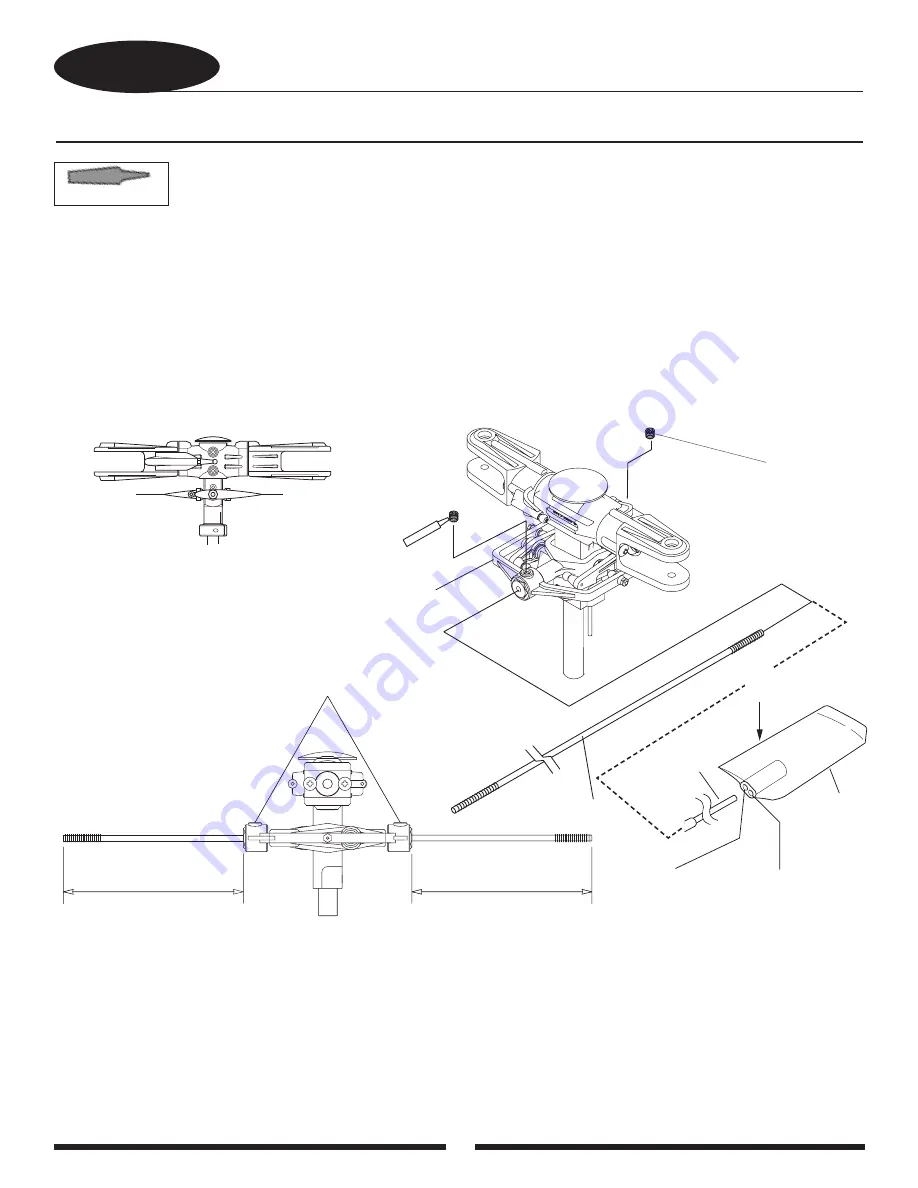
38
4-5
OPTIONAL AGGRESSIVE 3D CONTROL SYSTEM SETUP
C. 3D FLYBAR/PADDLE INSTALLATION
Remove the current flybar and paddles by removing one paddle and loosening the two 4 mm flybar
control arm screws.
Install the special 410 mm 3D flybar and paddles as shown. Check to make sure that the flybar is
centered before attaching the paddles.
Thread the 3D paddles onto the flybar through the front hole in the paddles. It is not recommended
that the paddles be used in the rear hole, as they will make the control overly aggresssive.
Use Blue Threadlock
Align paddles so they
are parallel to each
other and to the flybar
control arm.
Flybar Control Arm
Adjust so that A and B are
exactly the same length.
Rear Hole:
Very aggresssive cyclic
rate; not recommended
as the cyclic rate will be
excessive.
Front Hole:
Recommended for
a high cyclic rate.
A (6
1
/
8
'')
B (6
1
/
8
'')
410 mm
Flybar
Paddle threads onto
Flybar 25 mm
Thin 3D
Paddle
4x4 mm Set Screw
410 mm Flybar
Continued