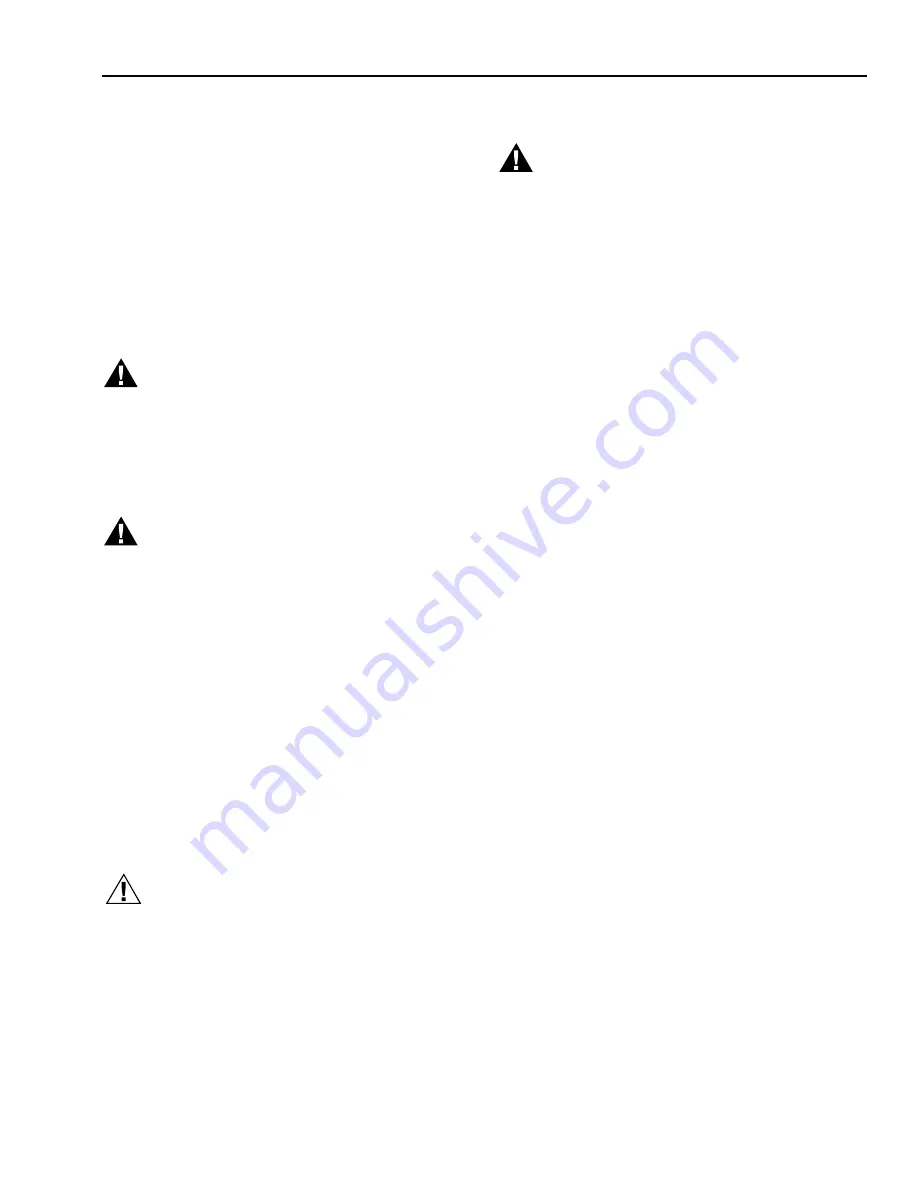
VS8510/VS8520 MILLIVOLT COMBINATION GAS CONTROL
68-0203
5
INSTALLATION
When Installing this Product...
•
Read these instructions carefully. Failure to follow them
could damage the product or cause a life threatening
hazardous condition.
•
Check the ratings given in the instructions and on the
product to make sure the product is suitable for your
application.
•
Installer must be a trained, experienced service
technician.
•
After installation is complete, check out product operation
as provided in these instructions.
WARNING
Oxygen depletion hazard.
Can cause injury or death due to asphyxiation.
1.
Use only vented gas valve models on vented
appliances.
2.
Use only unvented gas valve models on unvented
appliances.
WARNING
Fire or explosion hazard.
Can cause severe injury or death and property
damage.
Follow these warnings exactly:
1.
Disconnect power supply before wiring to prevent
electrical shock or equipment damage.
2.
To avoid dangerous accumulation of fuel gas, turn
off gas supply at the appliance service valve
before starting installation, and perform a Gas
Leak Test after the installation is complete.
1.
Always install the sediment trap in the gas supply
line to prevent contamination of the gas control.
2.
Do not force the gas control knob. Use only your
hand to turn the gas control knob. Never use any
tools.
3.
If the gas control knob does not operate by hand,
the gas control should be replaced by a qualified
service technician. Force or attempted repair can
result in fire or explosion.
CAUTION
Equipment damage.
Can burn out heat anticipator in thermostat.
Never apply a jumper across or short the valve coil
terminals.
IMPORTANT
These gas controls are shipped with protective seals
over the inlet and outlet tappings. Do not remove the
seals until ready to connect the piping.
Follow the appliance manufacturer instructions, if available;
otherwise, use these instructions.
Converting Between Natural and LP Gas
WARNING
Fire or explosion hazard.
Can cause severe injury or death and property
damage.
1.
Do not use a gas control set for natural gas on an
LP gas system or a gas control set for LP gas on
a natural gas system.
2.
When making a conversion, the main pilot burner
orifices must be changed to meet the appliance
manufacturer specifications.
Refer to the appliance manufacturer instructions for orifice
specifications and changeover procedure. Gas controls are
factory-set for natural (and manufactured) or LP gas. Do not
attempt to use a control set for natural (manufactured) gas on
LP gas, or a control set for LP on natural (manufactured) gas.
Gas controls with standard regulator can be converted from
one gas to the other with a conversion kit (ordered
separately). Order part no. 395991 to convert from natural
(manufactured) to LP gas. Order part no. 395992 to convert
from LP to natural (manufactured) gas.
Location
Locate the combination gas control where it cannot be
affected by steam cleaning, high humidity, dripping water,
corrosive chemicals, dust or grease accumulation or
excessive heat. To ensure proper operation, follow these
guidelines:
•
Locate gas control in a well-ventilated area.
•
Mount gas control high enough to avoid exposure to
flooding or splashing water.
•
Ensure the ambient temperature does not exceed the
ambient temperature ratings for each component.
•
Cover gas control if appliance is cleaned with water,
steam, or chemicals or to avoid dust and grease
accumulation.
•
Ensure the gas control is not located where exposure to
corrosive chemical fumes or dripping water can occur.
Install Piping to Gas Control
All piping must comply with local codes and ordinances or
with the National Fuel Gas code (ANSI Z223.1 NFPA No. 54),
whichever applies. Tubing installation must comply with
approved standards and practices.
1. Use new, properly reamed pipe free from chips. When
tubing is used, ensure the ends are square, deburred
and clean. All tubing bends must be smooth and without
deformation.
2. Run pipe or tubing to the control. If tubing is used,
obtain a tube-to-pipe coupling to connect the tubing to
the control.
3. Install sediment trap in the supply line to the gas
control. See Fig. 3.
Install Control
1. Mount control 0 to 90 degrees, in any direction, from
the upright position of the gas control knob, including
vertically.
2. Mount the control so gas flow is in the direction of the
arrow on the side of the control.