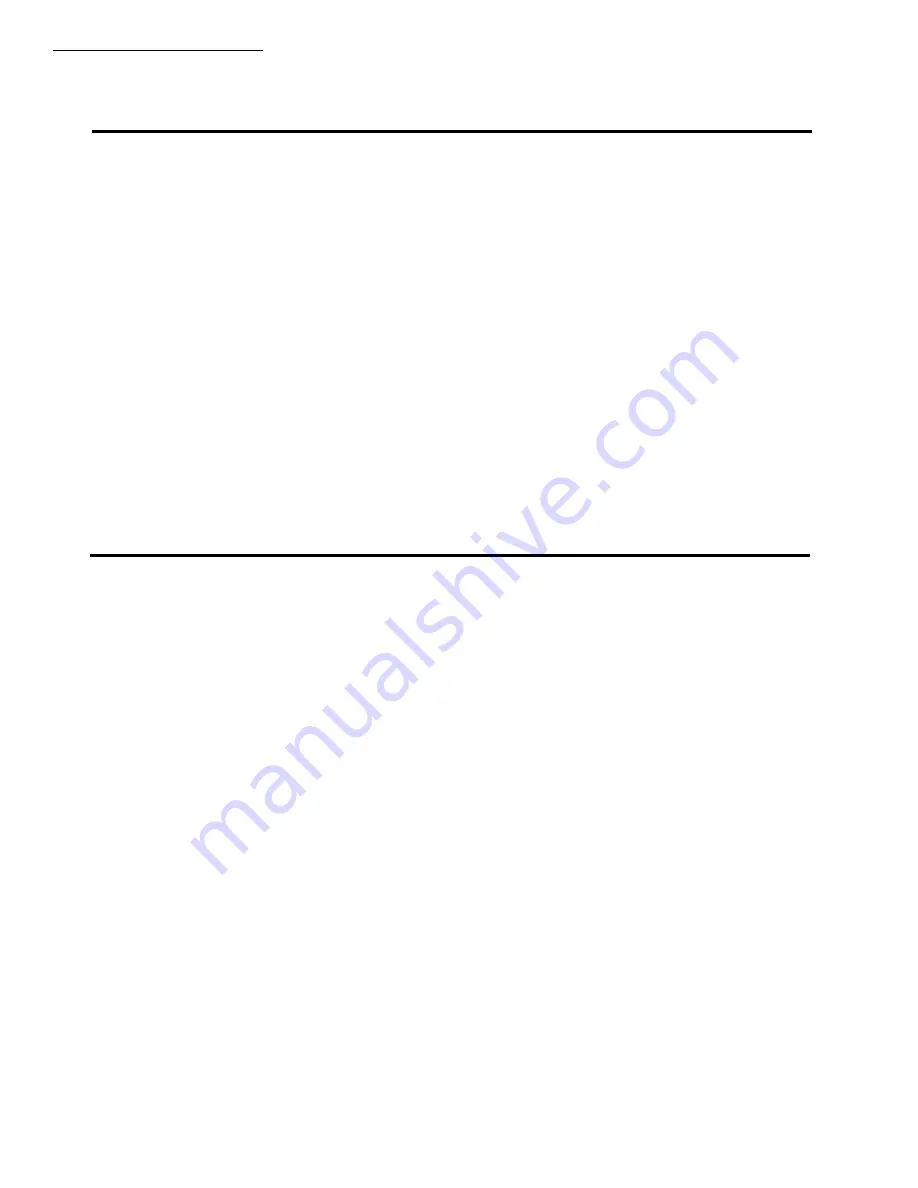
68-0046—4
12
VR8200, VR4200
MAINTENANCE • OPERATION
Maintenance
Regular preventive maintenance is important in applica-
tions that place a heavy load on system controls such as in
the commercial cooking and agricultural and industrial
industries because:
• In many such applications, particularly commercial
cooking, the equipment operates 100,000-200,000
cycles per year. Such heavy cycling can wear out the
gas control in one to two years.
• Exposure to water, dirt, chemicals and heat can dam-
age the gas control and shut down the control system.
The maintenance program should include regular check-
out of the gas control, see the Startup and Checkout section,
and the control system as described in the appliance manufac-
turer literature.
Maintenance frequency must be determined individually
for each application. Some considerations are:
• Cycling frequency. Appliances that may cycle 120,000
times annually should be checked monthly.
• Intermittent use. Appliances that are used seasonally
should be checked before shutdown and again before
the next use.
• Consequence of unexpected shutdown. Where the cost
of an unexpected shutdown would be high, the system
should be checked more often.
• Dusty, wet, or corrosive environment. Since these
environments can cause the gas control to deteriorate
more rapidly, the system should be checked more
often.
Gas valves exposed to high ammonia conditions, i.e.,
those used in greenhouses or animal barns, may fail in one or
two years. Contact your Honeywell sales representative to
request a gas valve with corrosion resistant construction.
The gas control should be replaced if:
• It does not perform properly on checkout or trouble-
shooting.
• The gas control knob is hard to turn or push down, or
it fails to pop back up when released.
• The gas control is likely to have operated for more
than 200,000 cycles.
Operation
The VR8200, VR4200 gas controls provide 3-position
(OFF-PILOT-ON) manual control of gas flow. The OFF
position prevents pilot and main burner gas flow. The
PILOT position allows pilot burner gas flow only. The ON
position allows pilot burner and main burner gas flow under
control of the thermostat and the two automatic valves.
When the thermostat calls for heat, the first automatic
valve and the second automatic valve operator open. The
second automatic valve diaphragm, controlled by the servo
pressure regulator, opens and adjusts gas flow as long as the
system is powered and the pilot is burning. The servo pressure
regulator monitors outlet pressure to provide an even main
burner gas flow. Loss of power closes the automatic valves,
but leaves the pilot lit, ready to return to normal service when
power is restored. Loss of pilot flame or flame too small to
reliably light the main burner, closes the safety shutoff valve
and the second automatic valve. The gas control must be
manually reset. Gas control operation is described in more
detail below.
VALVE POSITION DURING THERMOSTAT OFF
CYCLE
The valve is positioned as shown in Fig. 14 when the:
• manual gas control knob is in the ON position.
• pilot burner is lit.
• thermostat is not calling for heat.
The power unit holds the safety shutoff valve disc off its
seat, so gas can flow into the control. Pilot gas flows
through a port in the bushing around the reset button shaft
to the pilot burner. The first automatic valve is closed. The
second automatic valve operator is de-energized, closing
the channel to the pressure regulator, and opening a channel
to the underside of the second automatic valve diaphragm.
The combination of spring pressure under the second auto-
matic valve diaphragm and the lack of outlet pressure hold
the diaphragm firmly closed. Main burner gas flow is
blocked by both automatic valves.
WHEN THERMOSTAT CALLS FOR HEAT
The gas control allows pilot and main burner gas flow
during the thermostat ON cycle, as shown in Fig. 15. When
the thermostat calls for heat, the first automatic valve and the
second automatic valve operator are energized. The first
automatic valve opens, and the second automatic valve
operator valve disc is lifted off its seal. This diverts gas flow
from the automatic valve diaphragm, and causes a reduction
of pressure on the underside of this diaphragm. The reduced
pressure on the bottom of the automatic valve diaphragm
repositions the diaphragm downward away from the valve
seat, allowing main burner gas flow.
Standard Opening Pressure Regulation (VR8200A,M
and VR4200A,M)
During the ON cycle, the servo pressure regulator pro-
vides close control of outlet pressure, even if inlet pressure
and flow rate vary widely. Any outlet pressure change is
immediately reflected back to the pressure regulator dia-
phragm, which repositions to change the flow rate through
the regulator valve and, thus, through the diaphragm-oper-
ated automatic valve.
If outlet pressure begins to rise, the pressure regulator
diaphragm moves slightly higher, allowing less gas flow to
the gas control outlet. This increases gas pressure under the
automatic valve and repositions the valve disc closer to the