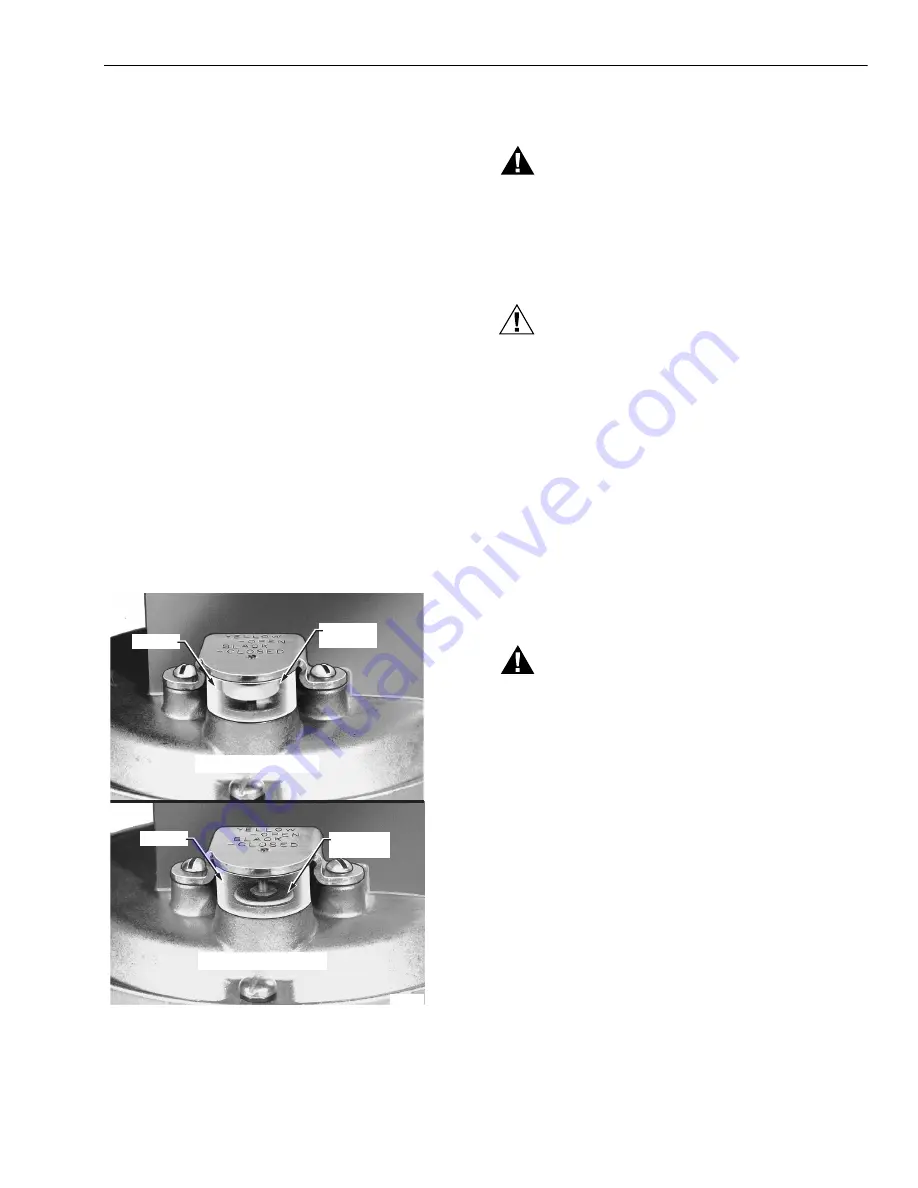
V48A,F,J; V88A,J DIAPHRAGM GAS VALVES
9
60-2080—9
of the valve flows out through the bleed port. This reduces the
pressure on top of the diaphragm, allowing the gas pressure
below to lift the diaphragm and open the valve.
When all the gas has bled off the top of the diaphragm, the
valve is fully open, permitting gas flow to the main burner.
After the controller is satisfied, the procedure is reversed. The
controller contacts open so the coil is de-energized. The
plunger is released, moving to the DOWN position. This
closes the bleed port and opens the supply port so gas flows
again into the top port of the valve. As the gas pressure on top
of the diaphragm increases, the diaphragm begins to close.
When the pressures on both sides of the diaphragm are
balanced, the valve will be closed. The weight and spring help
to close the valve. If the gas supply fails and there is no
pressure below the diaphragm, the weight and spring will
close the valve.
In the event of a power failure during automatic operation, all
V88 and V48 valves will close. Normal operation will be
resumed upon power restoration.
Operation of the Valve Position Indicator
(Fig. 11)
An optional valve position indicator is available in the 1-1/4 in.
V48A2227 and 2 in. V48F1103 Valves. When the valve is
open, a yellow disk shows in the window. When the valve is
closed, only the black top of the disk is visible.
Fig. 11. Valve position indicator (optional).
CHECKOUT AND TROUBLESHOOTING
WARNING
Explosion Hazard.
Can cause severe injury, death or property
damage.
Do not allow fuel to accumulate in the combustion
chamber. If fuel is allowed to enter the chamber for
longer than a few seconds without igniting, an
explosive mixture could result.
CAUTION
Equipment Damage Hazard.
Can cause equipment damage and improper
operation.
1. Do not put the system into service until you have
satisfactorily completed all applicable tests
described in the Checkout section of the
instructions for the flame safeguard control, and any
other tests required by the burner manufacturer.
2. Close all manual fuel shutoff valves as soon as
trouble occurs.
Checkout
Start the system and observe its operation through at least
one complete cycle to be sure the valve functions as
described in the Operation section.
Troubleshooting
WARNING
Electrical Shock Hazard.
Can cause severe injury or death.
Use utmost care during troubleshooting. Line voltage
is present at the actuator for a V48 Valve, and is
present in all controller circuits for all V48 and V88
Valves.
IMPORTANT:
Do not assume that the valve must be replaced until
all other sources of trouble have been eliminated.
If the valve will not open when the thermostat or
controller is calling for heat:
1.
Check that there is voltage at the valve actuator (black
leadwires, Fig. 7). Be careful—there should be line
voltage at the actuator of a V48.
2.
If there is no voltage at the actuator, first make sure line
voltage power is connected to the master switch, the
master switch is closed, and overload protection (circuit
breaker, fuse, or similar device) has not opened the
power line.
3.
For a V88 only: If a line voltage power is okay, check the
transformer. Replace it if necessary.
WINDOW
YELLOW
DISC
BLACK TOP
OF DISC
VALVE OPEN
VALVE CLOSED
WINDOW
M18856