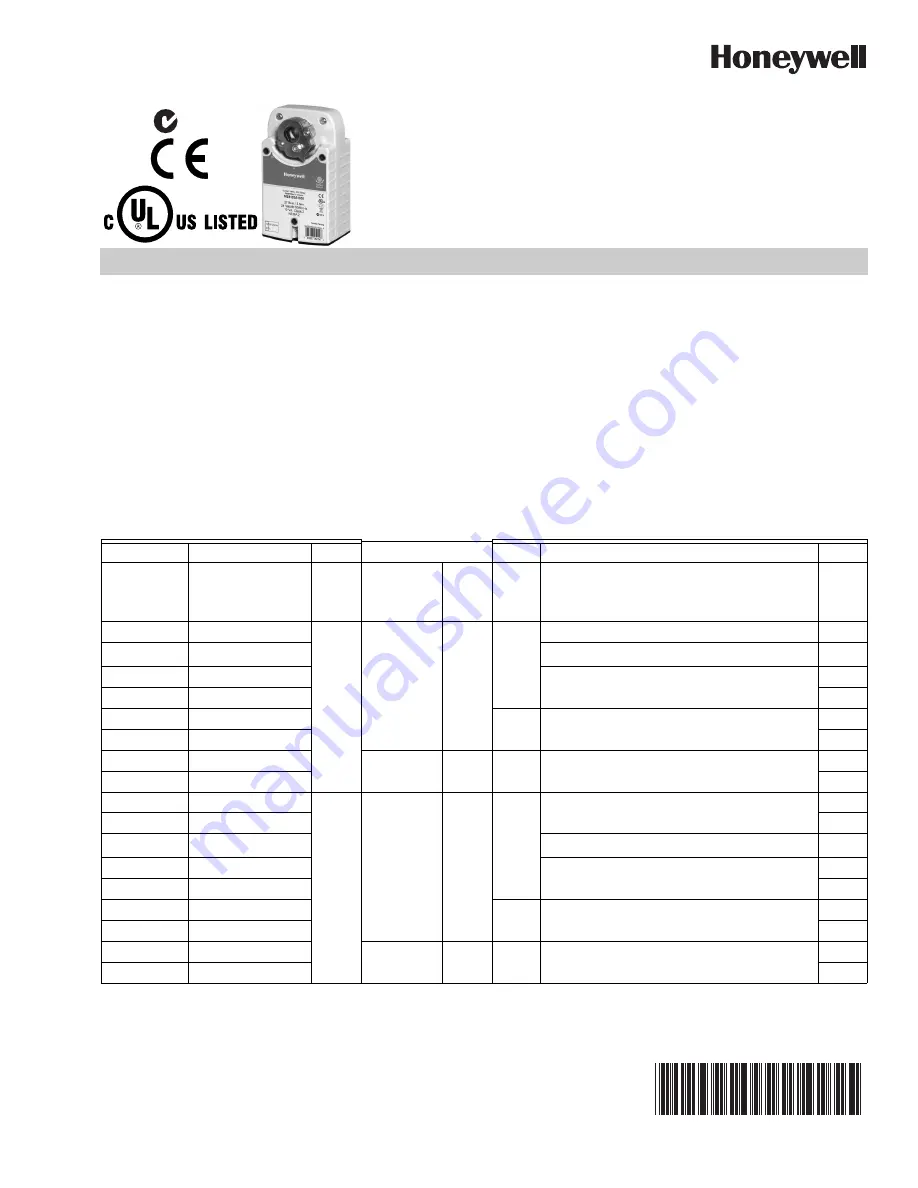
INSTALLATION INSTRUCTIONS
62-0274-07
3 Nm, 5 Nm Series Spring Return
Direct Coupled Actuators
MS3103, MS3105, MS4103, MS4105, MS7403, MS7405, MS7503,
MS7505, MS8103, MS8105
N314
MS3103, MS3105, MS4103, MS4105, MS7403, MS7405,
MS7503, MS7505, MS8103, MS8105 Spring Return Direct
Coupled Actuators (DCA) are used within heating, ventilating,
and air-conditioning (HVAC) systems. They can drive a variety
of quarter-turn, final control elements requiring spring return
fail-safe operation.
Applications include:
• Volume control dampers, mounted directly to the drive
shaft or remotely (with the use of accessory hardware).
• Quarter-turn rotary valves, such as ball or butterfly valves
mounted directly to the drive shaft.
• Linear stroke globe or cage valves mounted with linkages
to provide linear actuation.
• Available with cable on select models
SPECIFICATIONS
Models:
Device Weight:
3.5 lbs (1.60 kg)
Ambient Operating Temperature:
-40° to 150°F (-40° to 65°C)
-22° to 150°F (-30° to 65°C) (Two position only)
Shipping and Storage Temperature:
-40° to +150°F (-40° to +65°C)
1
Number represents range
2
2-10 Vdc
3
0/2-10 Vdc
Table 1. Models.
Power Supply
Model Number
Model Number
(including 3 ft. whip) Torque
Voltage
VA
Driving
1
Drive
(sec)
Control Input/Output Description
SPDT
Aux
Switch
MS3103J1030
27 lb-in
(3 Nm)
24 Vac/dc
@50/60 Hz +/-
20%
24Vdc+/-10%
6/3
90
Sylk-enabled
0
MS7403A2030
Floating, Modulating
2
,Three-Position, Feedback
0
MS7503A2030
Floating, Modulating
3
, and Feedback
0
MS7503A2130
1
MS8103A1030
45
Two-Position (SPST)
0
MS8103A1130
1
MS4103A1030
100-250 Vac
@50/60Hz
6/9
45
Two-Position (SPST)
0
MS4103A1130
1
MS3105J3030
44 lb-in
(5 Nm)
24 Vac/dc
@50/60 Hz +/-
20%
24Vdc+/-10%
6/3
90
Sylk-enabled (5 addresses & Analog Output)
0
MS3105J3130
1
MS7405A2030
Floating, Modulating
2
, Three-Position, Feedback
0
MS7505A2030 MS7505W2030
Floating, Modulating
3
, and Feedback
0
MS7505A2130 MS7505W2130
1
MS8105A1030 MS8105W1030
45
Two-Position (SPST)
0
MS8105A1130 MS8105W1130
1
MS4105A1030
100-250 Vac
@50/60Hz
6/9
45
Two-Position (SPST)
0
MS4105A1130
1