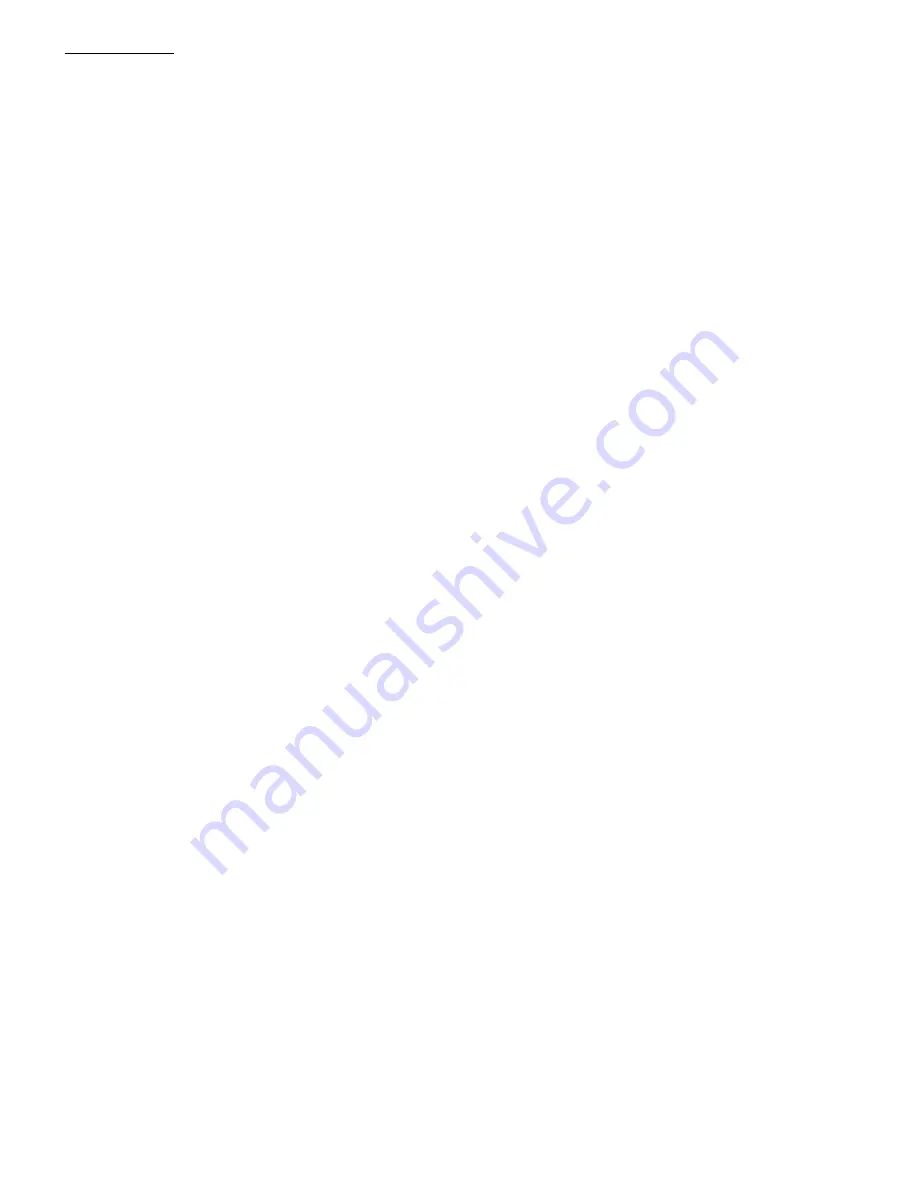
26
RM7895A,B,C,D
CHECKOUT
NOTE: INTERMITTENT PILOT MODELS should con-
tinue with step 6. INTERRUPTED PILOT MODELS
should proceed to step 7.
6. INTERMITTENT PILOT MODELS—After the se-
quence has entered the normal burner run period, turn pilot
gas pressure down very slowly, reading the manometer (or
gauge) as the pressure drops. Stop immediately when the
FLAME LED goes out. Note the pressure at this point.
a. If the Flame Failure Action jumper is not clipped:
allow the RM7895A,B to recycle through
PREPURGE. If the Flame Failure Action jumper is
clipped: push the reset pushbutton and allow the
RM7895A,B to recycle through PREPURGE.
b. As the control attempts to relight the pilot, turn
the pilot gas pressure back up slowly until the
FLAME LED comes on. This step must be com-
pleted within 4 or 10 seconds, depending on the
selected PFEP, or lockout will occur.
c. Turn the pilot back down slightly but not enough
to cause the FLAME LED to go out. (Keep the
pilot gas pressure just above the reading noted in
step 6 above.)
NOTE: Step d requires two people, one to open the manual
main fuel valve(s) and one to watch for ignition.
d. With the sequence in the normal burner run mode,
make sure the automatic main fuel valve(s) is
open. Smoothly open the manual main fuel shutoff
valve(s) and watch for main burner lightoff.
e. If the main flame is not established within five
seconds or the normal lightoff period specified by
the burner manufacturer, close the manual main
fuel shutoff valve(s) and open the master switch.
Return to step 6. If the burner flame is established
in the normal lightoff period, proceed to step 16.
7. INTERRUPTED PILOT MODELS—When the PI-
LOT IGN begins, set the Run/Test Switch to TEST posi-
tion to stop the sequence. The FLAME LED will come on
when the pilot ignites.
NOTE: If the sequence does not stop, reset the system and
make sure you set the Run/Test Switch to TEST within the
first three or eight seconds of the PILOT IGN sequence.
IMPORTANT: You have eight seconds or three seconds,
depending on the PFEP selected, to position the Run/
Test Switch in the TEST position to stop the sequence
after the start of the PILOT IGN period.
8. Turn the pilot pressure down very slowly, reading the
manometer (or pressure gauge) as it will drop. Stop instantly
when the FLAME LED goes out. Note the pressure at the
RM7895 flame relay dropout point. The pilot is at the
minimum turndown position. Immediately, turn up the pilot
pressure until the FLAME LED comes on again.
NOTE: If there is no flame for fifteen seconds with the
sequence stopped at this point, the RM7895 will lockout.
9. Repeat step 8 to verify the pilot gas pressure reading
at the exact point the FLAME LED light goes out.
10. Increase the pilot pressure immediately until the
FLAME LED comes on, and then turn it down slowly to
obtain a pressure reading just above the dropout point.
NOTE: Step 11 requires two people—one to open the
manual valve(s) and one to watch for ignition.
11. Set the Run/Test Switch in the RUN position and let the
sequence proceed. At ten seconds into the Ignition Trial
period, make sure the automatic main fuel valve(s) open;
then smoothly open the manual main fuel shutoff valve(s)
(or any other manually opened safety shutoff valve(s), if
used) and watch for main burner ignition. If the main burner
flame is established, proceed to step 16.
12. If the main burner flame is not established within five
seconds, or within the normal lightoff time specified by the
equipment manufacturer, close the manual main fuel shutoff
valve(s) and open the master switch. If the lightoff was
rough, the pilot flame size is too small.
13. Recycle the burner and stop the sequence in the
PILOT IGN period by using the Run/Test Switch.
14. Increase the pilot flame size by increasing its fuel
flow until a smooth main flame is accomplished.
15. Reposition the flame scanner sight tube or use orifices
until the pilot flame signal voltage is approximately 1.25 -
1.50 Vdc.
16. When the main burner lights reliably with the pilot at
turndown, disconnect the manometer (or pressure gauge) and
turn the pilot gas flow up to that recommended by the
equipment manufacturer.
17. If used, remove the bypass jumpers from the subbase
terminals, limits/controls or switches.
18. Run the system through another cycle to check for
normal operation.
19. Return the system to normal operation.
IGNITION INTERFERENCE TEST (All Flame Rods)
Test to be sure that a false signal from a spark ignition
system is not superimposed on the flame signal.
Ignition interference can subtract from (decrease) or
add to (increase) the flame signal. If it decreases the flame
signal enough, it will cause a safety shutdown. If it increases
the flame signal, it could cause the FLAME LED to come
on when the true flame signal is below the minimum accep-
table value.
Start the burner and measure the flame signal with both
ignition and pilot (or main burner) on, and then with only the
pilot (or main burner) on. Any significant difference (greater
than .5 Vdc) indicates ignition interference.
TO ELIMINATE IGNITION INTERFERENCE
1. Be sure there is enough ground area.
2. Be sure the ignition electrode and the flame rod are
on opposite sides of the ground area.
3. Check for correct spacing on the ignition electrode:
a. 6,000V systems - 1/16 to 3/32 in. [1.6 to 2.4 mm].
b. 10,000V systems - 1/8 in. [3.2 mm].