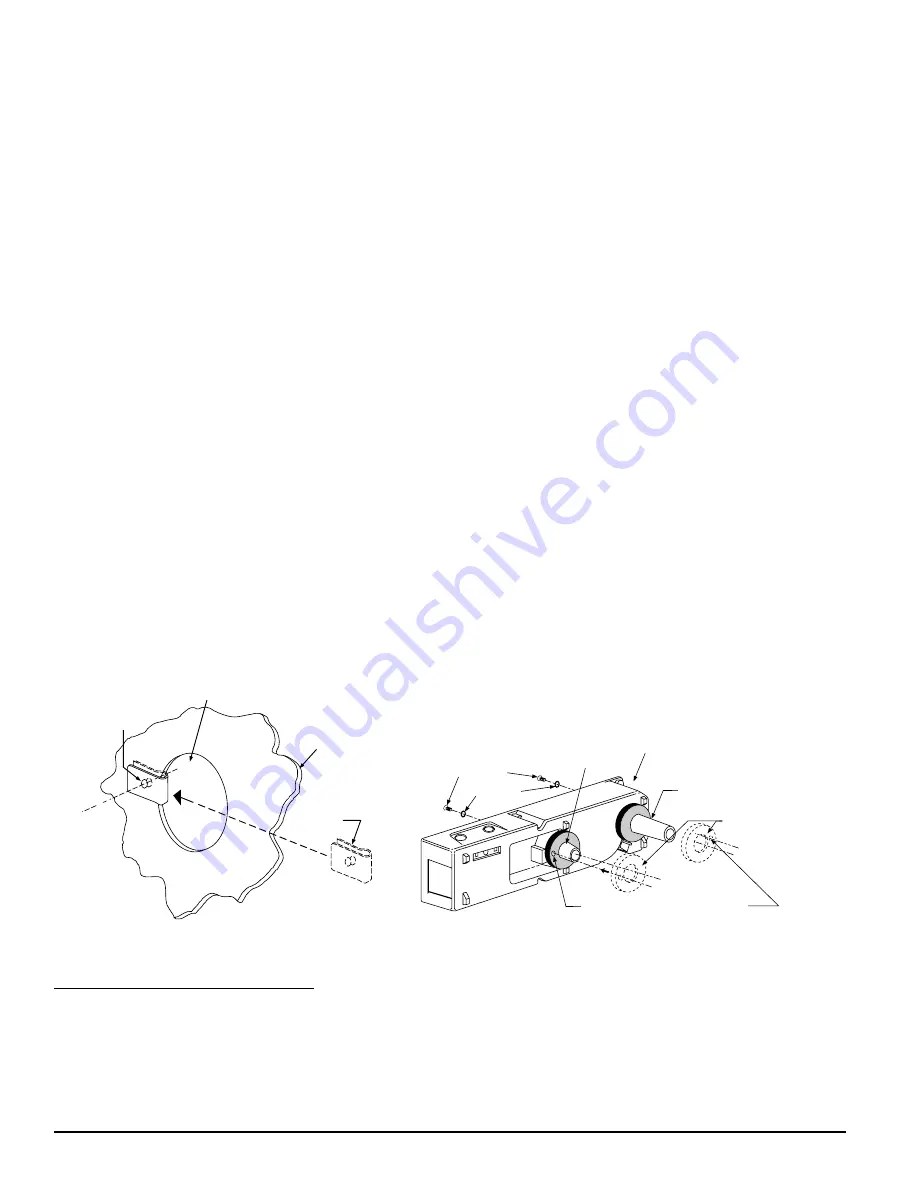
INSTALLATION SEQUENCE
PAGE
Step 1. Verify duct air flow direction and velocity ................................................................................................................2
Step 2. Drill mounting holes ................................................................................................................................................2
Step 3. Mount duct housing ................................................................................................................................................3
Step 4. Install inlet tube ......................................................................................................................................................3
Step 5. Complete field wiring ..............................................................................................................................................5
Step 6. Install filters..............................................................................................................................................................7
Step 7. Perform detector check ..........................................................................................................................................7
Step 8. Install cover ............................................................................................................................................................9
Step 9. Perform final system check (Testing) ......................................................................................................................9
STEP 1. VERIFY DUCT AIR FLOW DIRECTION AND VELOCITY
The 14506873-001 is designed to be used in air handling systems having air velocities of 500 to 4000 ft (152.5 to 1219
m) per minute. Be sure to check engineering specifications to ensure that the air velocity in the duct falls within these
parameters. If necessary, use a velocity meter to check the air velocity in the duct.
STEP 2. DRILL MOUNTING HOLES
Remove the paper backing from the drilling template. Affix the template to the air duct at the desired mounting location.
Make sure the template lies flat and smooth on the air duct. Center punch hole targets and remove the template. Drill the
holes as indicated on the template. Slide the two speed nuts over the two small holes (Hole A) next to the sampling tube
bushing holes (Hole B) previously drilled in the duct. (See Figure 2.)
Location of detectors mounted in or on air ducts should be at least six duct widths downstream from any duct openings,
deflection plates, sharp bends, or branch connections.
Exception: Where it is physically impossible to locate the detector accordingly, the detector can be positioned closer than
six duct widths, but as far as possible from the opening, bend, or deflection plates.
STEP 3. MOUNT DUCT HOUSING
Remove the duct housing cover. Slide the foam gaskets over the tube bushings as shown in Figure 2A. Make sure the
two small holes in the gaskets line up with the two duct housing mounting holes. Put one 5/16-inch O-ring over each of
the two #10 sheet metal screws. Use the two sheet metal screws to secure the duct housing to the duct.
CAUTION: Do not overtighten the screws.
A78-2046-00
A78-2449-00
Figure 2. Speed Nut Mounting Location.
Figure 2A. Installation of Foam Gaskets Over
Sampling Tube Bushings.
TABLE 1. SAMPLING (INLET) TUBES
TUBE
OUTSIDE DUCT WIDTH
SSDST-1.5
1 to 2 ft.
(30 to 61 cm)
SSDST-3
2 to 4 ft.
(61 to 122 cm)
SSDST-5
4 to 8 ft.
(1.2 to 2.4 m)
SSDST-10
8 to 12 ft.
(2.4 to 3.7 m)
SCREW HOLES FOR ATTACHING
DETECTOR HOUSING TO DUCT
FOAM GASKETS
EXHAUST TUBE
(EXTENSION BUSHING)
DUCT DETECTOR
HOUSING
O-RINGS
MOUNTING
SCREWS
INLET SAMPLING
TUBE BUSHING
HOLE B
HOLE A
DUCT
WALL
SPEED
NUT
A78-2454-00
Figure 10. Photo Head Exploded View
REMOVABLE
COVER
REPLACEABLE
SCREEN
COVER
REMOVAL
SLOT
VANED
SENSING
CHAMBER
PHOTO UNITS
a. Remove detector cover by inserting a small-bladed screwdriv-
er into the cover removal slot located approximately 90
degrees from the test module socket, twisting cover counter-
clockwise to remove. See Figure 10.
b. Lift the screen from the photo chamber. Vacuum the screen
and cover before using clean, compressed air to loosen and
blow out any remaining debris. (Replacement screens, part no.
SSDRS24, are available.)
c. Vacuum photo chamber, then use clean compressed air to
blow area clean.
d. Replace screen by aligning arrow on top with the field test slot
on the base of the detector. Push screen into place. Screen
should fit tightly to chamber.
ION UNITS
a. Remove the detector cover and screen assembly by depress-
ing the three lock prongs on the top of the cover and rotating
the cover counterclockwise. The SSDCRT400 Cover Removal
Tool makes cover removal easier. See Figure 11.
b. Carefully pull the screen out of the cover.
c. Clean the screen thoroughly with a soft brush or vacuum.
(Replacement screens, part no. SSDRS14.)
d. Brush or vacuum the inside of the cover. Cover may then be
blown out using clean, compressed air.
e. Vacuum sensing chamber before using clean, compressed air
to loosen and blow out any remaining debris.
f.
Press the screen back into the cover.
g. Replace the detector cover on the sensing chamber. Rotate it
clockwise to lock it into place.
BOTH TYPES OF UNITS
5. Reinstall the detector in its housing.
6. Restore system power.
7. Put detector into alarm using appropriate method as described
in STEP 7. PERFORM DETECTOR CHECK.
8. Notify the proper authorities that testing has been completed
and the smoke detector system is back in service.
9. Other checks that should be made during maintenance proce-
dures:
— Holes or cracks in duct work near vicinity of detector.
— Air leaks where detector housing or sampling tubes are
attached to duct.
— Dust accumulations in or on sampling tubes.
— Screw terminal tightness.
SPECIFICATIONS
Length:
14.5 inches (36.7 cm.)
Width:
5 inches (12.7 cm.)
Depth:
4 inches (10.2 cm.)
Weight:
4 lbs. (1.8 kg.)
Operating Temperature Range:
32° to 120°F (0° to 49°C)
Operating Humidity Range:
10% to 93% Relative Humidity
Duct Air Velocity:
500 – 4000 ft./min. (157.5 – 1219.2 m/min.)
A78-2455-00
Figure 11. Ion Head Exploded View
LOCK PRONG
REMOVABLE SCREEN
REMOVABLE
COVER
FOR
CLEANING
SENSING CHAMBER
H500-03-00
10
I56-475-09R
H500-03-00
3
I56-475-09R