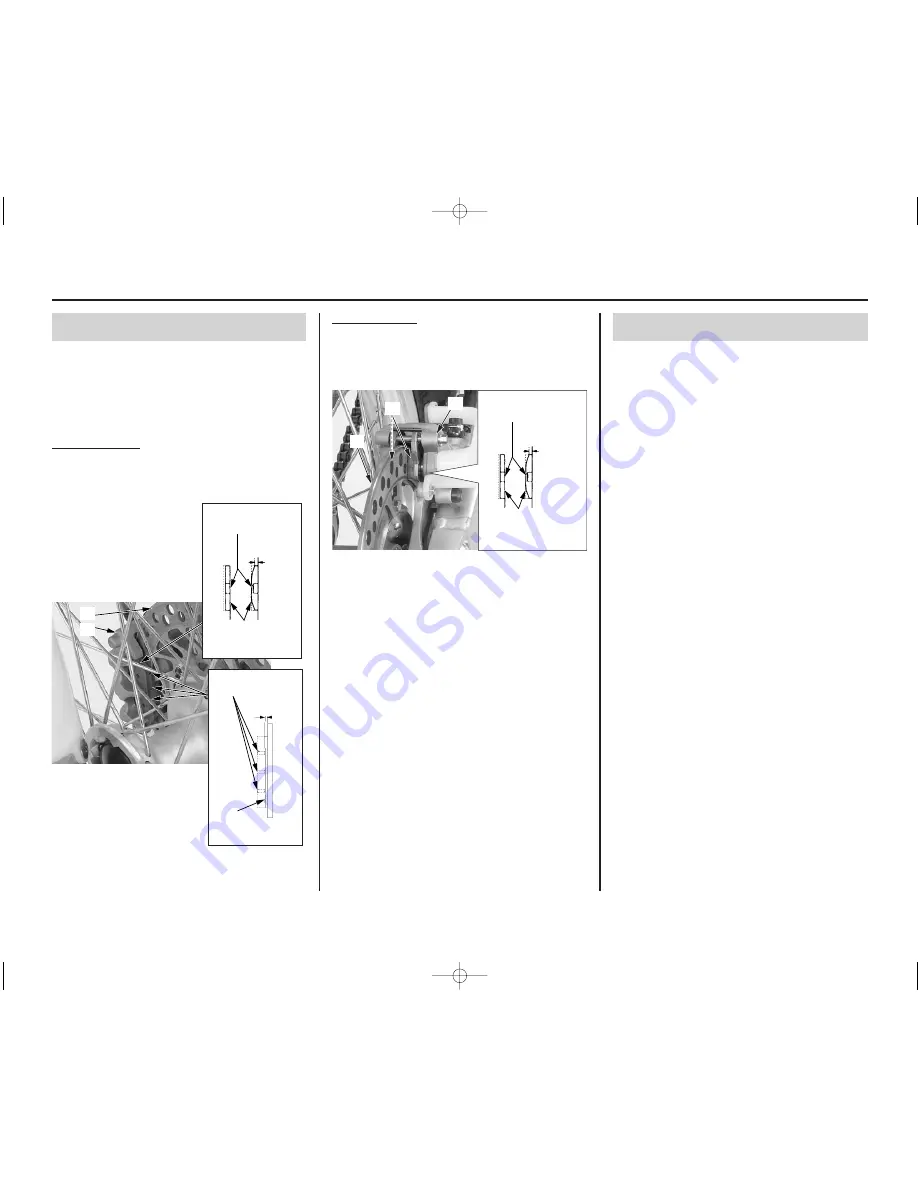
Brakes
Brake Pad Wear
Brake pad wear depends on the severity of usage
and track conditions. (Generally, the pads will
wear faster on wet and dirty tracks) Inspect the
pads at each regular maintenance interval (page
21).
Front Brake Pads
Inspect the pads (1) through the front wheel to
determine the pad wear. If either pad is worn
anywhere to a thickness of 0.04 in (1 mm), both
pads must be replaced.
(1) brake pads
(3) brake disc
(2) front brake caliper
Rear Brake Pads
Inspect the pads (4) from the rear side of the
caliper to determine the pad wear. If either pad
is worn anywhere to a thickness of 0.04 in
(1 mm), both pads must be replaced.
(4) brake pads
(6) brake disc
(5) rear brake caliper
Other Inspections
Check that the front lever and rear pedal
assemblies are positioned properly and the
securing bolts are tight.
Make sure there are no fluid leaks. Check for
deterioration or cracks in the hoses and fittings.
68
Servicing Your Honda
(3)
(2)
minimum thickness
indicator
0.04 in
(1 mm)
replace
(1)
wear indicator
grooves
0.04 in
(1 mm)
(1)
replace
(5)
(4)
replace
0.04 in
(1 mm)
minimum thickness
indicator
(6)
(4)
*CR125R/60-71(31KSR620).qxd 5/6/05 1:13 PM Page 68
Summary of Contents for 2007 CR125R
Page 14: ...10 Before Riding CR125 00 23 31KSR620 qxd 5 6 05 1 10 PM Page 10...
Page 20: ...16 Basic Operating Instructions CR125 00 23 31KSR620 qxd 5 6 05 1 11 PM Page 16...
Page 84: ...80 Servicing Your Honda CR125R 72 80 31KSR620 qxd 5 6 05 1 14 PM Page 80...
Page 120: ...116 Tips CR125R 111 116 31KSR620 5 6 05 1 17 PM Page 116...
Page 133: ...Technical Information 129 Wiring Diagram CR125R 117 140 31KSR620 5 6 05 1 51 PM Page 129...
Page 134: ...130 Technical Information CR125R 117 140 31KSR620 5 6 05 1 51 PM Page 130...