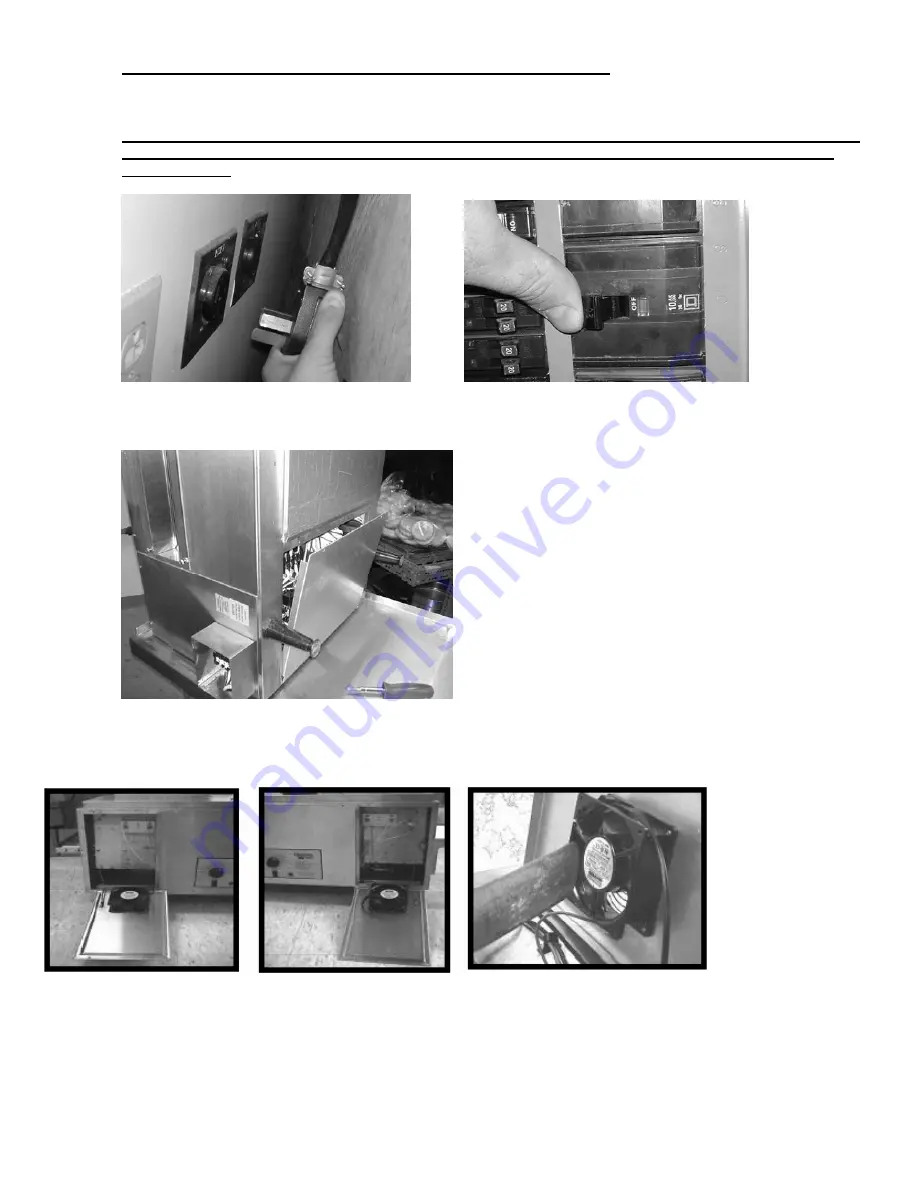
IF FURTHER ASSISTANCE IS REQUIRED:
CONTACT STAR/HOLMAN FACTORY SERVICE TEAM AT 1-800-807-9054
12
LONG TERM CLEANING PROCEDURES (every 6 months)
Turn power off and allow cooling fans to run until the control box is cooled off. The fans are controlled by a
thermostat in the control box.
DISCONNECT UNIT FROM POWER SUPPLY OR TURN POWER OFF AT WALL BREAKER. BE SURE THE
SANDWICH WARMER IS COMPLETELY COOLED BEFORE PERFORMING ANY OF THE FOLLOWING
PROCEDURES.
1. With the power off, allow the unit to cool completely. Place Sandwich Warmer on non-extension end.
Remove screws holding control box covers in place and remove.
NOTE:
TO PREVENT DAMAGE TO CONTROLS
OR ELEMENTS, DO NOT SET THE
MACHINE ON SIDE PANELS.
TO PREVENT DAMAGE TO
ACCESSORIES, REMOVE CRUMB
TRAYS AND UNLOAD TRAY BEFORE
LIFTING OVEN TO UPRIGHT POSITION
2. Remove screws holding control box covers in place and remove.
3. Using a vacuum, clean the inside of control box. Wipe any buildup that cannot be vacuumed with a dry towel.
4. Replace control box covers and fasten with screws. Put the machine back on its feet.
5. Remove side panels and vacuum compartments as performed under monthly cleaning procedures.
Summary of Contents for qt14
Page 21: ......