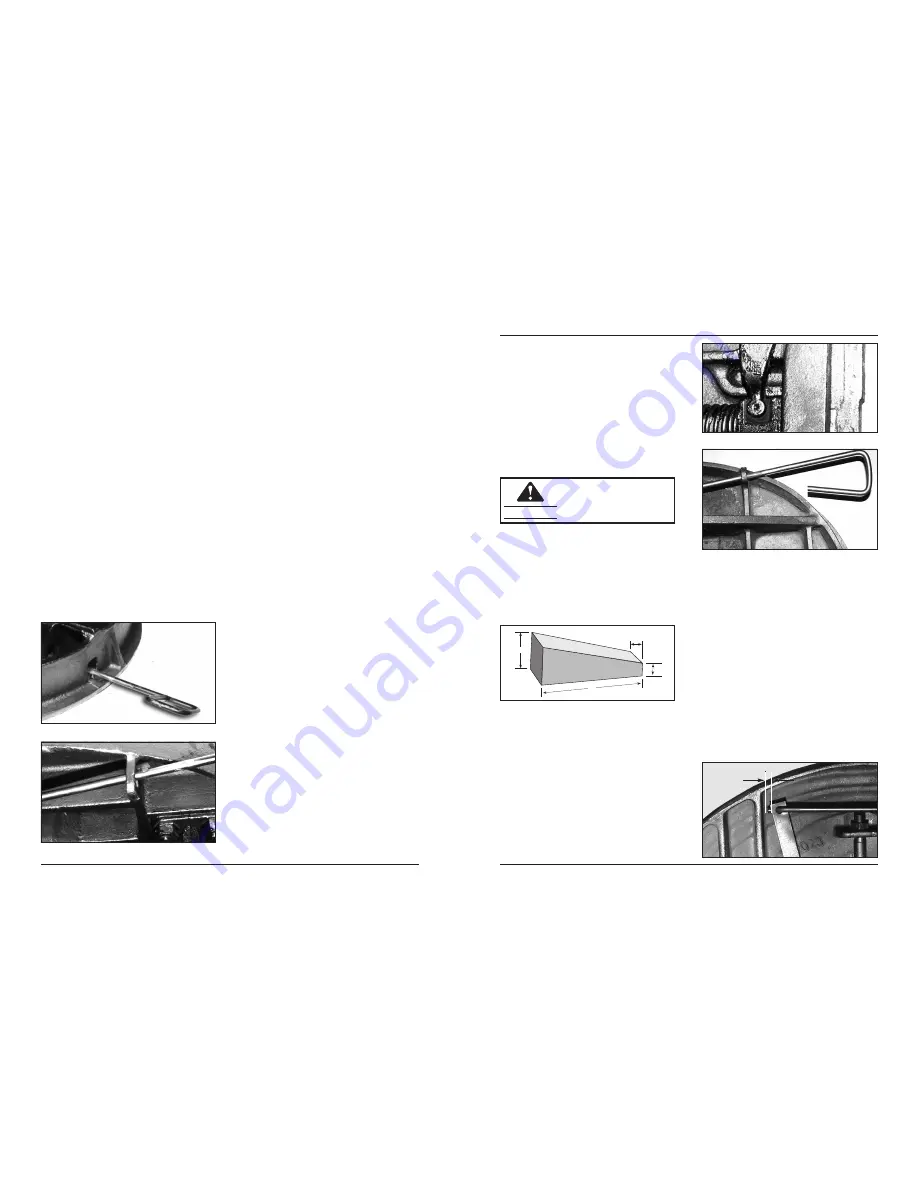
6
Uncoupling:
To uncouple the lock tester, pull the secondary
lock release handle (
9
) out, raise it up and
engage the handle lug with the top plate casting
(
Figure 12
). Then, pull the release handle (
16
) out
and raise it up and engage its handle lug with
the top plate casting (
Figure 13
). This will retract
the plunger (
17
) and hold it in so that the step in
the plunger is not visible in the throat area. As
the kingpin on the lock tester is pulled out
(rearward), the swinging lock (
6
) will open. As
the swinging lock opens, it will push the plunger
back slightly, causing the release handle (
16
) to
extend outward slightly. This action disengages
the release handle from its notch in the casting,
allowing the release handle to move to the
locked position. As the swinging lock (
6
) opens
past the plunger (
17
), the plunger will extend
into the throat area and become visible again.
The release handle (
16
) will move inward. As the
swinging lock (
6
) opens fully, it will contact the
retracted secondary lock (
10
), pushing the
secondary lock release handle (
9
) slightly
outward, causing its handle lug to disengage
and allowing the handle to drop slightly.
WARNING:
If the top plate assembly does not
operate properly,
DO NOT USE IT.
Review the
troubleshooting hints and rebuilding procedures
or contact your local HOLLAND representative
for assistance.
Check the Rocker Assembly and Brackets
Before Remounting the Top Plate:
1.
Inspect the rocker assembly and brackets for
cracks or damage and replace if necessary.
2.
Apply grease to the brackets and rocker
assembly through the grease fittings located
on the fifth wheel brackets and rocker
assembly, as shown in Holland Publication
“
FW2080 Series Installation, Operation and
Maintenance Instructions
”
; form number
FW 246.
Periodic Maintenance and Adjustment:
1.
Lubricate lock periodically by greasing
through the fittings in the lock pins.
2.
Lubricate the brackets and rocker by
applying grease through the fittings
provided.
3.
For maximum service life, the fifth wheel
should be steam cleaned, inspected and
adjusted as necessary every 30,000 miles
(50,000 km). For additional specific
instructions, refer to HOLLAND publication
FW-TE-14C “Fifth Wheel Maintenance
Procedures.”
Adjustment Procedure:
IMPORTANT:
Adjustment must be performed
with a lock tester having a kingpin to the SAE
dimensions appropriate for your fifth wheel.
1.
Close the locks using the lock tester.
2.
Tighten the Allen head adjustment screw in
the throat of the top plate by turning
clockwise until tight.
3.
Loosen the adjustment screw by turning
counterclockwise 1
1
⁄
2
turns. The fifth wheel is
now properly adjusted.
4.
Verify this adjustment by locking and
unlocking several times.
Figure 12
Figure 13
3
1.
Before attempting to rebuild, review each
troubleshooting hint on the front page of this
manual. You may find that rebuilding is not
necessary.
2.
If rebuilding is required, check the front page
of this manual to be sure you have the
correct kit for the fifth wheel you are about
to rebuild.
3.
Totally disassemble and clean the top plate.
4.
Inspect the top plate for cracks and a loose
lock pin hole. If the plate is cracked, or if the
lock pin hole is elongated, the top plate must
be discarded.
NOTE:
When rebuilding, use only HOLLAND
rebuilding kits and replace all roll pins, cotter pins,
springs, bolts, nuts and washers. Also, check the
rebuild kit and verify that all parts are present.
Before starting to reassemble the fifth wheel, it
may be necessary to fabricate a helper block. It
can be made from hardwood or steel. Refer to
Figure 1
for proper dimensions.
1.
Install the adjusting screw (
20
) through the
hole located in the throat of the fifth wheel
casting. Install compression spring (
23
) over
the screw, then slide the adjusting wedge (
22
)
over the screw. Compress the spring and
install lock nut (
21
). Tighten screw with 1⁄2˝
Allen wrench until nut is flush with the end
of the bolt.
2.
Lubricate the tail and faces of the plunger
with a light grease. Install spring (
18)
over
the tail of the plunger (
17
), insert through
plunger slots in the casting. Use the helper
block to hold the plunger (
17
) in place with
the spring compressed.
3.
Check the fit-up of the release lever (
15
) and
plunger (
17
). The rounded end of the release
lever must fit freely into the slot in the
plunger. If the parts do not fit together freely,
it will be necessary to deburr the rounded
end of the release lever (
see Figure 2
).
4.
Install the release handle (
16
) through the
guide slot in the casting. Install the release
lever (
15
) on the handle (
16
). The open end
of the release handle must face the rear of
the casting, as shown in
Figure 3
.
5.
Install nylon bushing (
24
) in the release lever
(
15
) so that the flange is between the casting
and lever. Install the release arm (
15
) in the
slot on the plunger (
see Figure 2
), install
washer (
13
) on cap screw (
12
) and insert
through release lever (
15
) and screw into
casting.
CAUTION: DO NOT OVERTIGHTEN
as
release arm (
15
) must move freely. Install
hex head lock nut (
14
) on cap screw (
12
)
and tighten.
8"
1"
1.5"
-2"
3"
Figure 1
Figure 3
REBUILDING PROCEDURES
WARNING
Do not attempt to repair or
rebuild if the top plate is cracked
or distorted, or the lock pin does
not fit tightly, as the top plate may
fail or the locks may malfunction.
Figure 2
Figure 4
1/2” MAX.