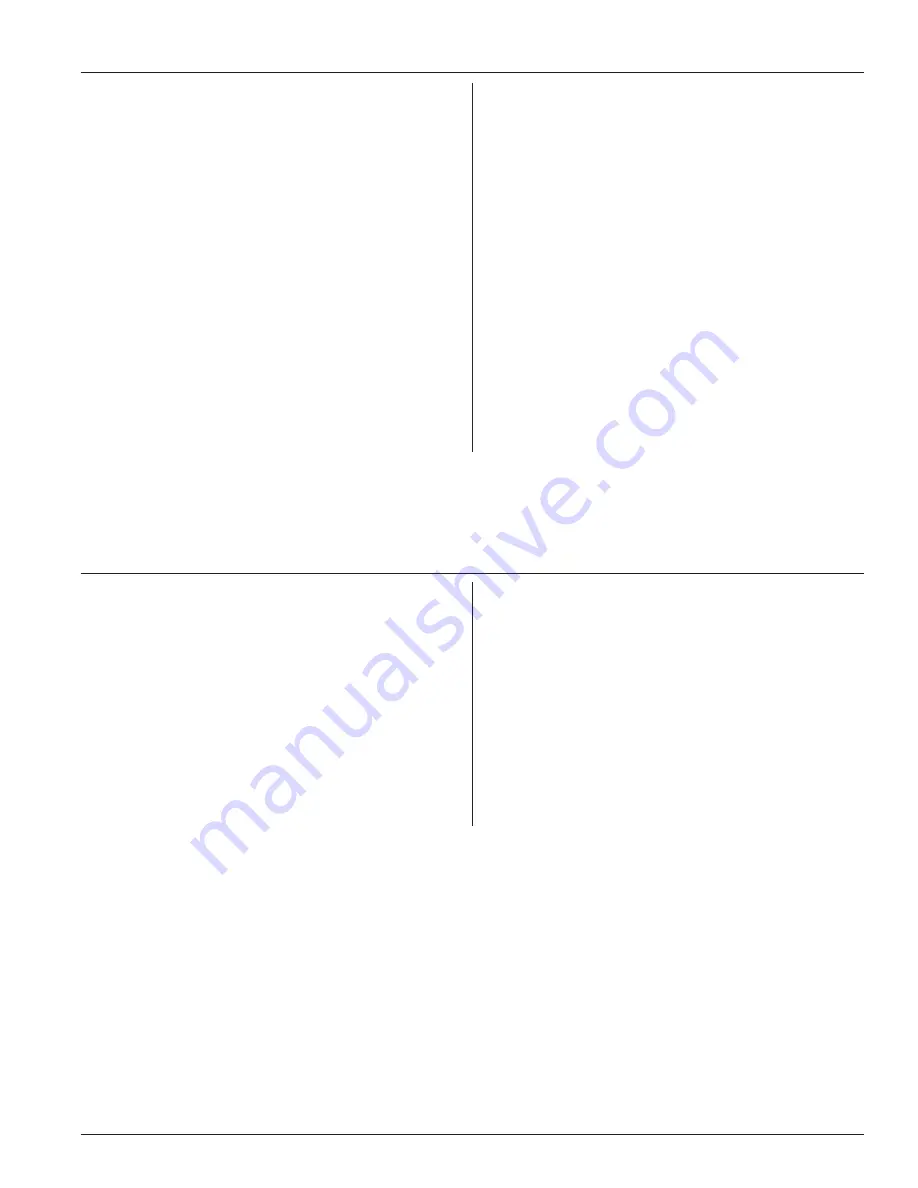
XL-FW232-02
9
CHECKING THE OPERATION OF THE FIFTH WHEEL
continued
Check the Mounting Brackets Before
Remounting the Top Plate:
1.
Inspect the brackets for cracks or damage, and
replace if necessary.
2.
Check the rubber bushings for wear.
Replace if necessary.
3.
Apply grease to the top bearing surface of the
mounting bracket before remounting the top plate.
4.
Inspect the bracket pins (or bolts, depending on the
construction of your fifth wheel) for wear. Replace,
if necessary, using the same configuration as
was removed when the fifth wheel was disassembled.
Periodic Maintenance and Adjustment:
1.
Lubricate the lock periodically by greasing through the
fittings in the lock pins.
2.
Lubricate the top plate and brackets by greasing
through the two fittings on the sides of the fifth wheel.
3.
For maximum service life, the fifth wheel should be
steam cleaned, inspected, and adjusted — as necessary
— every 30,000 miles (50,000 km).
For additional specific instructions, refer to
HOLLAND publication XL-FW303-XX “Fifth Wheel
Maintenance Procedures.”
Adjustment Procedure:
IMPORTANT:
Adjustment must be performed with a lock
tester — using a kingpin with SAE approved dimensions —
appropriate for your fifth wheel.
1.
Close the locks using the lock tester.
2.
Tighten the Allen head adjustment screw in the throat
of the top plate by turning clockwise until tight.
3.
Loosen the adjustment screw by turning
counterclockwise 1
1
⁄
2
turns. The fifth wheel is
now properly adjusted.
4.
Verify this adjustment by locking and unlocking
several times.
GENERAL INFORMATION
1.
All fifth wheel maintenance, adjustment and
rebuilding must be performed by a qualified person
using proper tools and safe procedures. For more
information, refer to HOLLAND publication
XL-FW303, “Fifth Wheel Maintenance Procedures.”
2.
Do not modify or add to the product.
3.
Use only genuine HOLLAND parts.
4.
Wear safety goggles during installation, removal
and rebuilding.
5.
Never strike any part of the item with a steel hammer.
6.
Do not weld on this product without written permis-
sion from the factory.
7.
Observe standard precautions when lifting.
8.
Do not deviate from these instructions. Any changes or
deviations will void all warranties, expressed or
implied, unless written consent is first obtained from
the factory.
9.
Check to see that all parts included in the kit are
enclosed in the box.
10. This equipment must not be used or maintained in a
careless manner.
These products are covered by HOLLAND’S Commercial
Products Warranty. HOLLAND reserves the right,
without giving prior notice, to change specifications and
dimensions as designs are altered or improved.
Summary of Contents for Hitch XA-71 Series
Page 11: ...XL FW232 02 11...