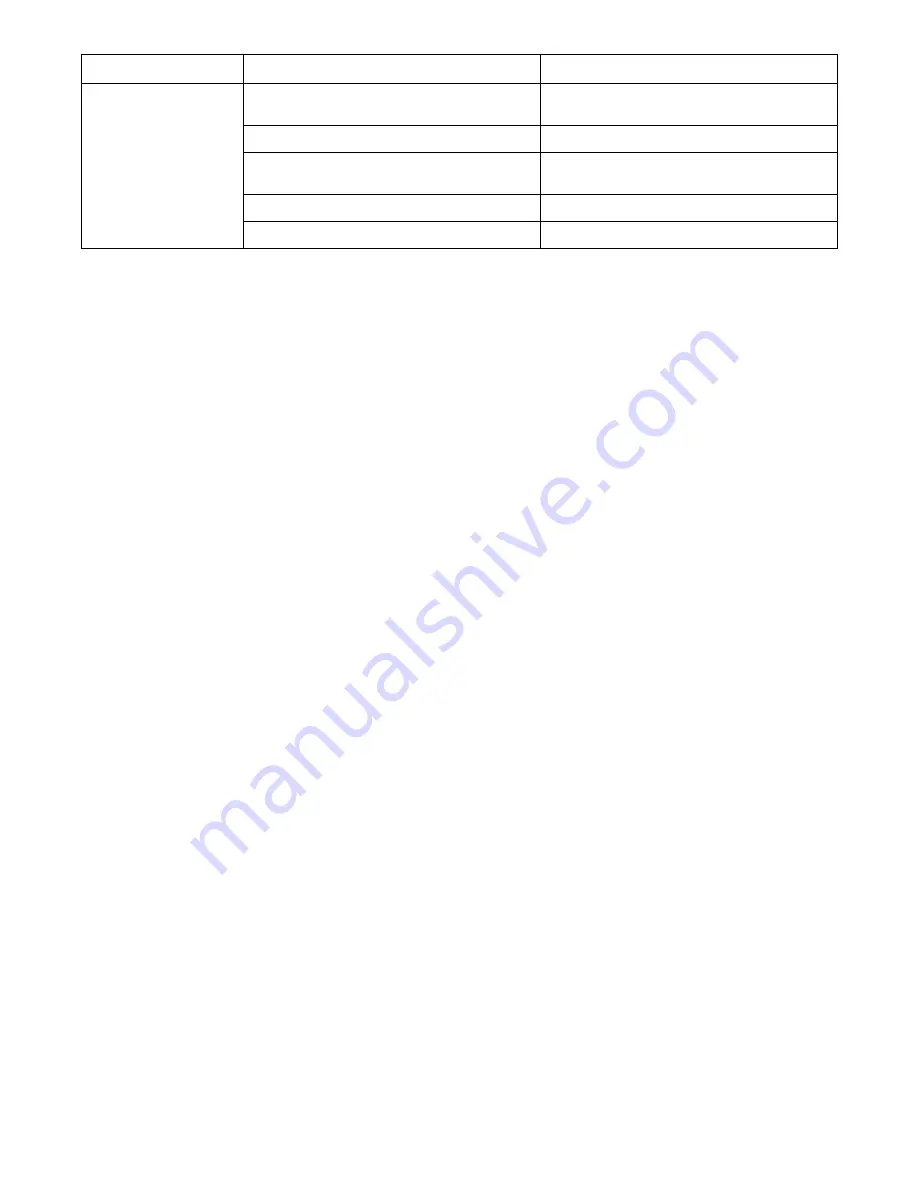
OM-927 Page 39
Problem
Remedy
Probable Cause
Welding arc not stable.
Wire slipping in drive rolls.
Adjust pressure setting on wire feed rolls. Replace worn
drive rolls if necessary.
Wrong size gun liner or contact tip.
Match liner and contact tip to wire size and type.
Incorrect voltage setting for selected wire feed speed on
welding power source.
Readjust welding parameters.
Loose connections at the gun weld cable or work cable. Check and tighten all connections.
Gun in poor shape or loose connection inside gun.
Repair or replace gun as necessary.
Summary of Contents for IronMan 210
Page 44: ...OM 927 Page 40 Notes ...
Page 54: ...Notes ...