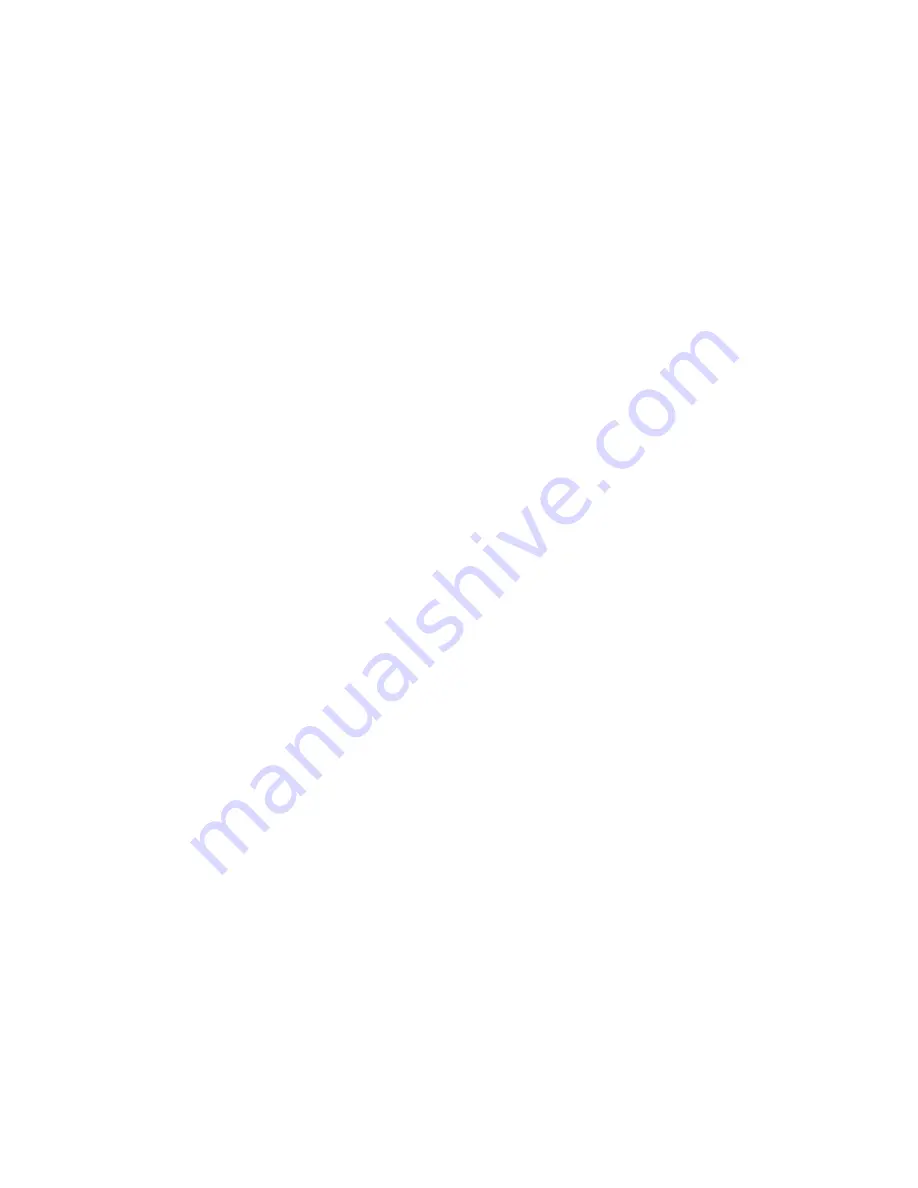
(b) Control unit
The control unit
(5, Fig. 3)
is a box containing a compact assembly of solid state components.
It receives an AC signal from the magnetic pickup and senses speed changes in the engine.
It provides a voltage signal to the actuator which causes the actuator to move the fuel control
lever as required to maintain a predetermined engine speed. Its power is received from the
12-V DC battery system.
(c) Actuator
The actuator
(12, Fig. 3)
supplies the force needed to move and position the fuel lever as re-
quired to maintain a constant engine speed. The actuator is operated by a DC signal from
the control unit.
(2) Engine electrical system
Items in the 12-volt engine electrical system that are provided by Hobart Brothers are:
(a) A heavy-duty motor starter
(b) Alternator with voltage regulator
(c) Starting switch
(d) Wiring harness
(3) Engine protective devices
(a) High coolant temperature switch
A high coolant temperature switch is mounted in the back of the cylinder block to monitor the
coolant temperature. If the coolant temperature reaches 210 degrees F
(99 degrees C)
, this
normally closed switch opens and actuates the fuel valve solenoid which shuts down the en-
gine.
(b) Oil pressure switch
A diaphragm-type switch monitors the pressure in the lubricating oil system. It is mounted in
the side of the cylinder block
(18, Fig. 3)
. If the pressure in the lube oil system falls to 10 psi
(69 kPa)
, this switch opens and actuates the fuel valve solenoid which shuts down the engine.
(4) Air cleaner
The diesel-engine air cleaner
(Fig. 4)
is a dry-cartridge type. It is equipped with a moisture elimi-
nator and a service indicator. The indicator functions to signal the operator when the cartridge
needs changing. A red cylindrical “flag”
(2)
is forced upward in a glass enclosed viewing chamber
(1)
when air pressure within the air cleaner housing drops below the outside air pressure. As the
cartridge becomes loaded with dirt and air pressure within the cleaner lessens, the “flag” gradu-
ally rises higher in the glass viewing chamber. When the “flag” reaches the top of the chamber, it
locks in that position to warn the operator that the cartridge must be changed. The “flag” is reset
(unlocked)
by pushing the reset button
(3)
located on the bottom of the indicator.
NOTE: The service indicator is mounted on the engine control panel and connected to the air cleaner
by a rubber hose. The indicator flag is visible only when the engine is running, or when the flag is locked
in WARNING position.
(5) Exhaust system
The exhaust system consists of a special noise reducing muffler
(2, Fig. 5)
connected by a pipe
(1)
to the exhaust manifold. The tail pipe
(3)
directs exhaust and noise downward.
OM-2028
May 1/91 Revised
1-1
Page 9
Summary of Contents for 6910
Page 2: ...This page intentionally left blank ...
Page 14: ...This page intentionally left blank OM 2028 Introduction June 20 89 Revised Page 2 ...
Page 40: ...This page intentionally left blank OM 2028 1 1 May 1 91 Revised Page 26 ...
Page 66: ...Engine Control Panel in Tilt out Position Figure 6 OM 2028 2 1 August 31 90 Revised Page 12 ...
Page 72: ...This page intentionally left blank OM 2028 2 2 June 20 89 Revised Page 6 ...
Page 128: ...Generator Set Figure 1 OM 2028 4 3 May 1 91 Revised Page 2 ...
Page 130: ...Canopy Assembly Figure 2 OM 2028 4 3 May 1 91 Revised Page 4 ...
Page 132: ...This page intentionally left blank OM 2028 4 3 May 1 91 Revised Page 6 ...
Page 134: ...Generator Set Without Canopy Figure 3 OM 2028 4 3 May 1 91 Revised Page 8 ...
Page 136: ...This page intentionally left blank OM 2028 4 3 May 1 91 Revised Page 10 ...
Page 138: ...Radiator and Cooling System Group Figure 4 OM 2028 4 3 May 1 91 Revised Page 12 ...
Page 142: ...Electric Governor Kit Figure 6 OM 2028 4 3 May 1 91 Revised Page 16 ...
Page 144: ...Fuel Lines Assembly Figure 7 OM 2028 4 3 May 1 91 Revised Page 18 ...
Page 146: ...Oil Line Assembly Figure 8 OM 2028 4 3 May 1 91 Revised Page 20 ...
Page 148: ...Stator Terminal Panel Assembly Figure 9 OM 2028 4 3 May 1 91 Revised Page 22 ...
Page 150: ...Power Module Panel Assembly Figure 10 OM 2028 4 3 May 1 91 Revised Page 24 ...
Page 152: ...Control Box Assembly Figure 11 OM 2028 4 3 May 1 91 Revised Page 26 ...
Page 154: ...Generator Controls Tray Assembly Figure 12 OM 2028 4 3 May 1 91 Revised Page 28 ...
Page 156: ...Protective Relays Tray Assembly Figure 13 OM 2028 4 3 May 1 91 Revised Page 30 ...
Page 158: ...Control Box and Internal Components Group Figure 14 OM 2028 4 3 May 1 91 Revised Page 32 ...
Page 160: ...Engine Control Panel Assembly Figure 15 OM 2028 4 3 May 1 91 Revised Page 34 ...
Page 162: ...This page intentionally left blank OM 2028 4 3 May 1 91 Revised Page 36 ...
Page 164: ...Output Terminal Board Assembly Figure 16 OM 2028 4 3 May 1 91 Revised Page 38 ...
Page 166: ...Generator Assembly Figure 17 OM 2028 4 3 May 1 91 Revised Page 40 ...
Page 168: ...Mounting Frame Assembly and Lifting Yoke Figure 18 OM 2028 4 3 May 1 91 Revised Page 42 ...
Page 170: ...Water Heater Figure 19 OM 2028 4 3 May 1 91 Revised Page 44 ...
Page 172: ...This page intentionally left blank OM 2028 4 3 May 1 91 Revised Page 46 ...
Page 174: ...This page intentionally left blank OM 2028 5 0 May 1 91 Revised Page 2 ...
Page 176: ...This page intentionally left blank OM 2028 6 0 June 20 89 Revised Page 2 ...
Page 177: ... I I I I I l zE I I 01 39NVN jlOVlQ t __ ...
Page 178: ......
Page 179: ......
Page 180: ......
Page 181: ......
Page 182: ......
Page 183: ......
Page 184: ......
Page 186: ......
Page 187: ......
Page 188: ......
Page 189: ......
Page 190: ......
Page 191: ......
Page 192: ......
Page 193: ......
Page 194: ......
Page 195: ......
Page 196: ......
Page 198: ......
Page 199: ......
Page 200: ......
Page 201: ......
Page 202: ......
Page 203: ......
Page 204: ......
Page 205: ......
Page 206: ......