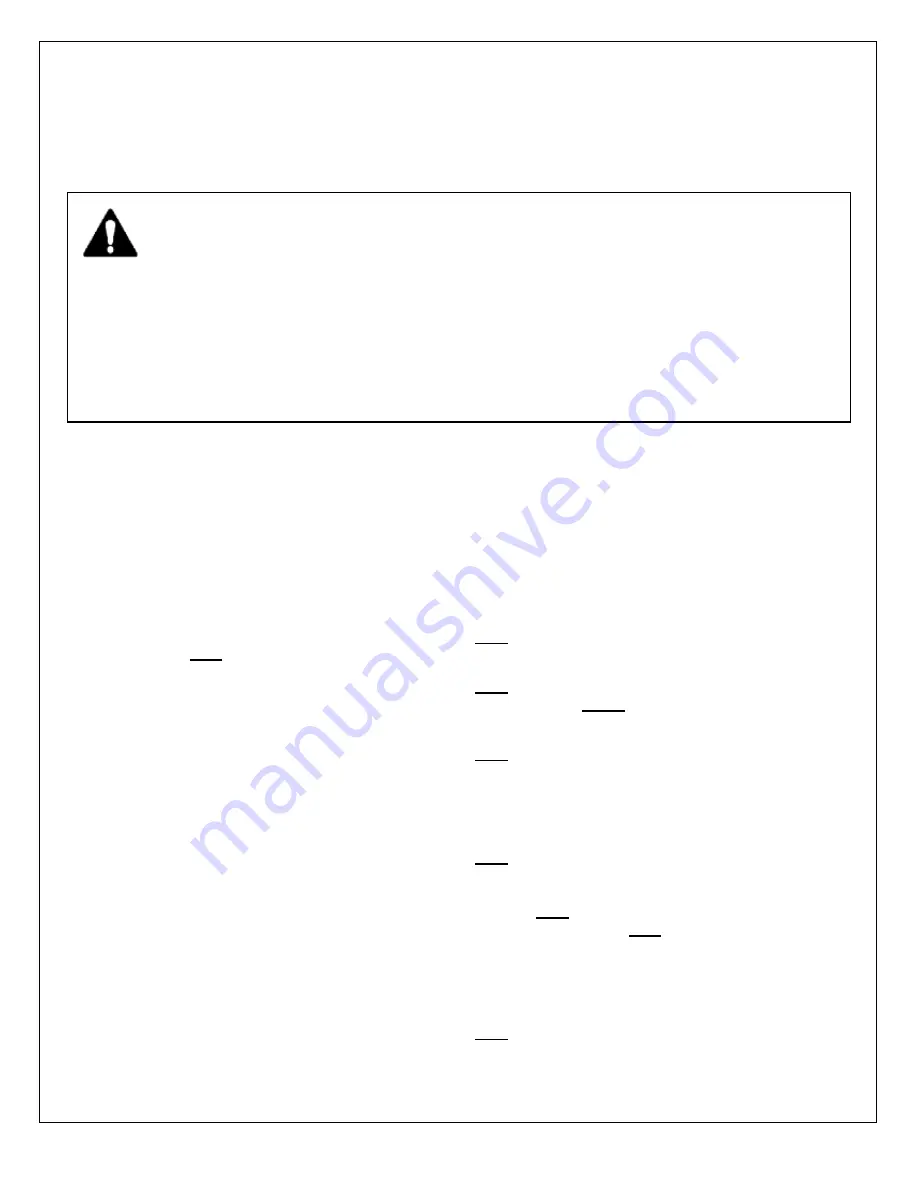
- 3 -
SAFETY
DEFINITION OF SAFETY TERMS AND SYMBOLS
Throughout this manual, the terms
DANGER, WARNING and CAUTION
are used to indicate the degree of hazard to
personnel if proper safety procedures are not followed. These words will be used in conjunction with the Safety Alert
Symbol: a dark triangle containing a white exclamation mark.
The safety information given in this manual does not replace any safety codes, insurance needs, federal, state and local
laws.
The Safety Alert Symbol means:
-
ATTENTION! - BECOME ALERT!
- YOUR SAFETY IS INVOLVED!
DANGER
Indicates an imminently hazardous situation, which, if not avoided,
WILL result in death or serious injury.
WARNING
Indicates a potentially hazardous situation, which, if not avoided,
Could result in death or serious injury.
CAUTION
Indicates a potentially hazardous situation, which, if not avoided,
May result in minor or moderate injury;
OR
May also be used to alert against unsafe practices, which
may result in damage to property.
ACCIDENTS CAN BE PREVENTED WITH
YOUR HELP!
The best safety device is a careful operator. HLA and
your dealer ask that
YOU
be that careful, responsible
equipment operator.
Pay attention to the job at hand. Do not let your mind
lose concentration on what you are doing. No accident
prevention program can be successful without the
wholehearted cooperation of the person who is directly
responsible for the operation of the equipment.
If accidents are to be prevented (
and accidents can be
prevented
), that prevention will come from equipment
operators who accept their complete responsibility and
anticipate the results of their actions.
The designer, the manufacturer, and the safety engineer
all help create a safe product, but their combined efforts
can be wiped out with a single careless act by the
operator of that product.
Do not attempt to operate this equipment under the
influence of drugs or alcohol.
YOU
ARE THE KEY TO SAFETY BECAUSE:
YOU
are responsible for the SAFE operation and
maintenance of
YOUR
rotary broom
.
YOU
are responsible to familiarize yourself, and anyone
else who will assemble, operate, maintain, or work around
this product, with the safety information contained in this
manual.
YOU
are responsible to read ALL information contained
in this manual to any operators or maintenance personnel
who are not fully able to read the written English language.
Whether
YOU
read the manual as written or translate it
into another language,
YOU
must make certain that all
operators and maintenance personnel have complete
understanding of the full and exact contents of this
manual.
YOU
can reduce the risk of injury or death by following all
safety precautions and by using good safety practices.
Summary of Contents for BR Series
Page 19: ...Notes ...