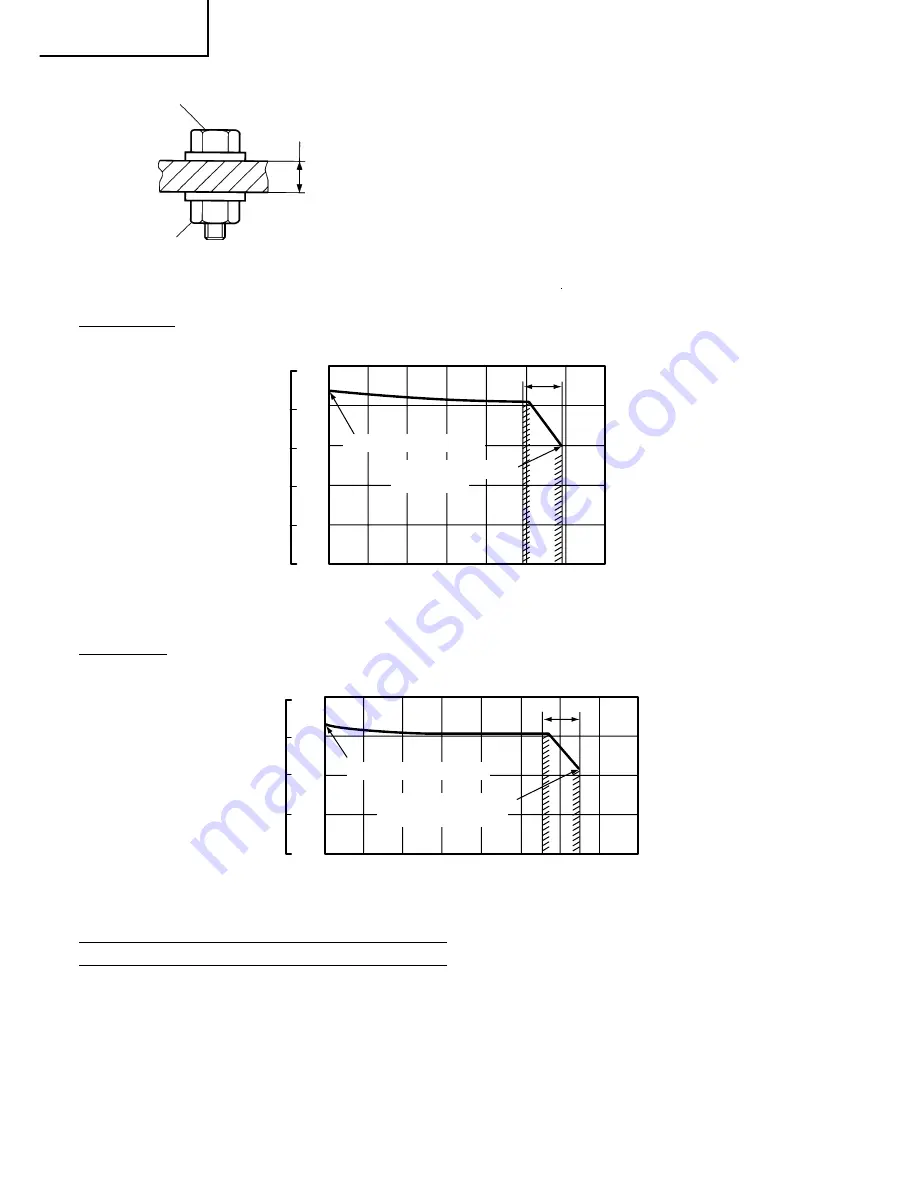
English
17
kgf·cm
1600
1200
800
400
0
0 20 40 60 80 100 120 140 160
N·m
160
120
80
40
0
a
Tightening torque
M16
×
55 F10T (tighening time 3 sec)
2000
1600
1200
800
400
0
0
20
40
60
80
100
120
140
200
160
120
80
40
0
a
kgf·cm
N·m
When full recharged
When completely
discharged
Number of tightenings (PCS)/charging
Fig. 28
For WR12DM2
For WR9DM2
Fig. 29
Tightening torque
Number of tightenings (PCS)/charging
When full recharged
When completely
discharged
M14
×
50 High tension bolt
(tighening time 3 sec)
MAINTENANCE AND INSPECTION
1. Inspecting the driver bit (WH12DM2, WH9DM2,
WH12DMR)
Using a broken bit or one with a worn out tip is
dangerous because the bit can slip. Replace it.
2. Inspecting the socket (WR12DM2, WR9DM2)
A worn or deformed hex. or a square-holed socket
will not give an adequate tightness to the fitting
between the nut or anvil, consequently resulting in
loss of tightening torque. Pay attention to wear of a
socket holes periodically, and replace with a new one
if needed.
3. Inspecting the mounting screws
Regularly inspect all mounting screws and ensure
that they are properly tightened. Should any of the
screws be loose, retighten them immediately. Failure
to do so may result in serious hazard.
4. Maintenance of the motor
The motor unit winding is the very “heart” of the
power tool.
Exercise due care to ensure the winding does not
become damaged and/or wet with oil or water.
Nut
Fig. 27
Explanation of strength grade:
4 — Yield point of bolt: 32 kgf/mm
2
8 — Pulling strength of bolt: 40 kgf/mm
2
*The following bolt is used.
Ordinary bolt: Strength grade 4.8
High tensile bolt: Strength grade 12.9
)
(
Bolt
Steel plate thickness t