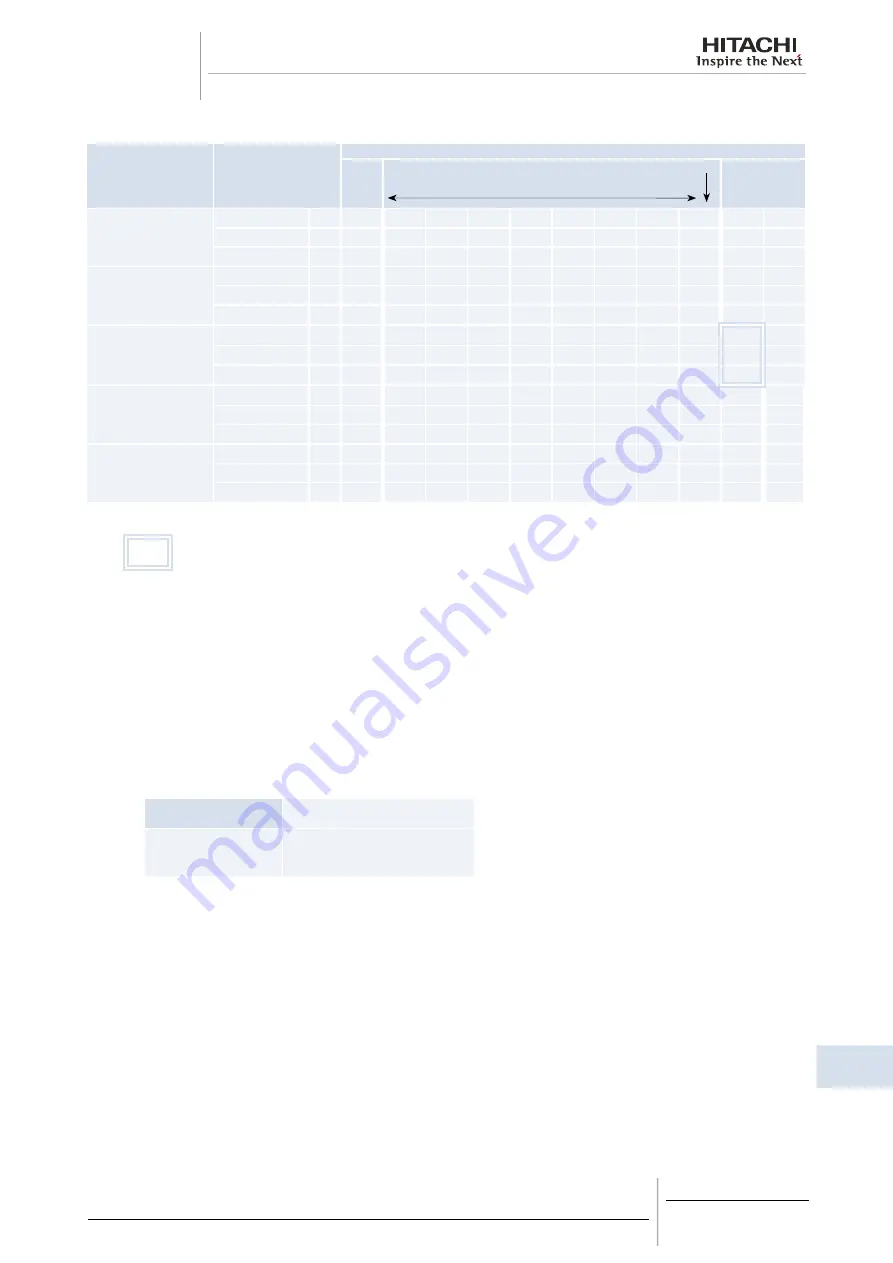
Application Data
Technical Catalogue
16
109
TCGB0051 rev 0 - 09/2009
¡
Model: RCUE80CLG2, RCUE100CLG2 and RCUE120CLG2
Condensing
Temperature
Performance
Compressor Load
7.5*
%
15~99%
Full
55°C
Capacity
%
10
20
30
40
50
60
70
80
90
92
Input
%
22
43
52
59
68
77
89
103
119
123
EER
%
47
47
58
68
74
78
79
78
76
75
50°C
Capacity
%
10
20
30
40
50
60
70
80
90
96
Input
%
19
37
46
53
60
68
77
88
104
112
EER
%
54
54
65
75
83
88
91
91
87
86
45°C
Capacity
%
10
20
30
40
50
60
70
80
90
100
Input
%
17
33
39
46
53
59
66
76
87
100
EER
%
61
61
77
87
94
102
106
105
103
100
40°C
Capacity
%
10
20
30
40
50
60
70
80
90
100
104
Input
%
14
28
35
40
45
51
58
66
73
85
89
EER
%
71
71
86
100
111
118
121
121
123
118
117
35°C
Capacity
%
11
21
30
40
50
60
70
80
90
100
109
Input
%
13
25
30
34
39
44
51
54
62
70
78
EER
%
84
84
100
118
128
136
137
148
145
143
140
:Standard Condition
(Condensing temperature: 45°C)
(Cooler Water Inlet/Outlet: 12/7°C)
NOTE:
1. Capacity: Cooling Capacity (kW)
Input: Compressor Input Power (kW)
EER: Capacity/Input (kW/kW)
2. Operating Conditions:
Chilled Water Outlet Temperature: 7°C
Water Flow Rate: Constant
3. Above Table shows the percentage of Capacity, input and EER based on the standard condition.
Therefore, each value can be calculated as below example:
Example: Model RCUE100 CLG2
Standard Condition
Condensing Temperature 40 °C,
Capacity 80%
Capacity:
290 kW
Capacity:
290 × 0.8 = 232 kW
Input:
84.8 kW
Input:
84.8 × 0.66 = 56.0 kW
EER:
3.42
EER:
3.42 × 1.21 = 4.14
4. Control marked (*) is available by the optional selection switch DSW7-3 / ON: Minimum Load Extension.
Summary of Contents for SAMURAI CLG2
Page 2: ......
Page 4: ......
Page 6: ......
Page 10: ......
Page 12: ......
Page 46: ......
Page 62: ......
Page 66: ......
Page 82: ......
Page 94: ...Drawings Technical Catalogue TCGB0051 rev 0 09 2009 94 14 2 4 Main printed circuit board ...
Page 95: ...Drawings Technical Catalogue 14 95 TCGB0051 rev 0 09 2009 14 2 5 Relays printed circuit board ...
Page 98: ......
Page 112: ......
Page 116: ......
Page 117: ......