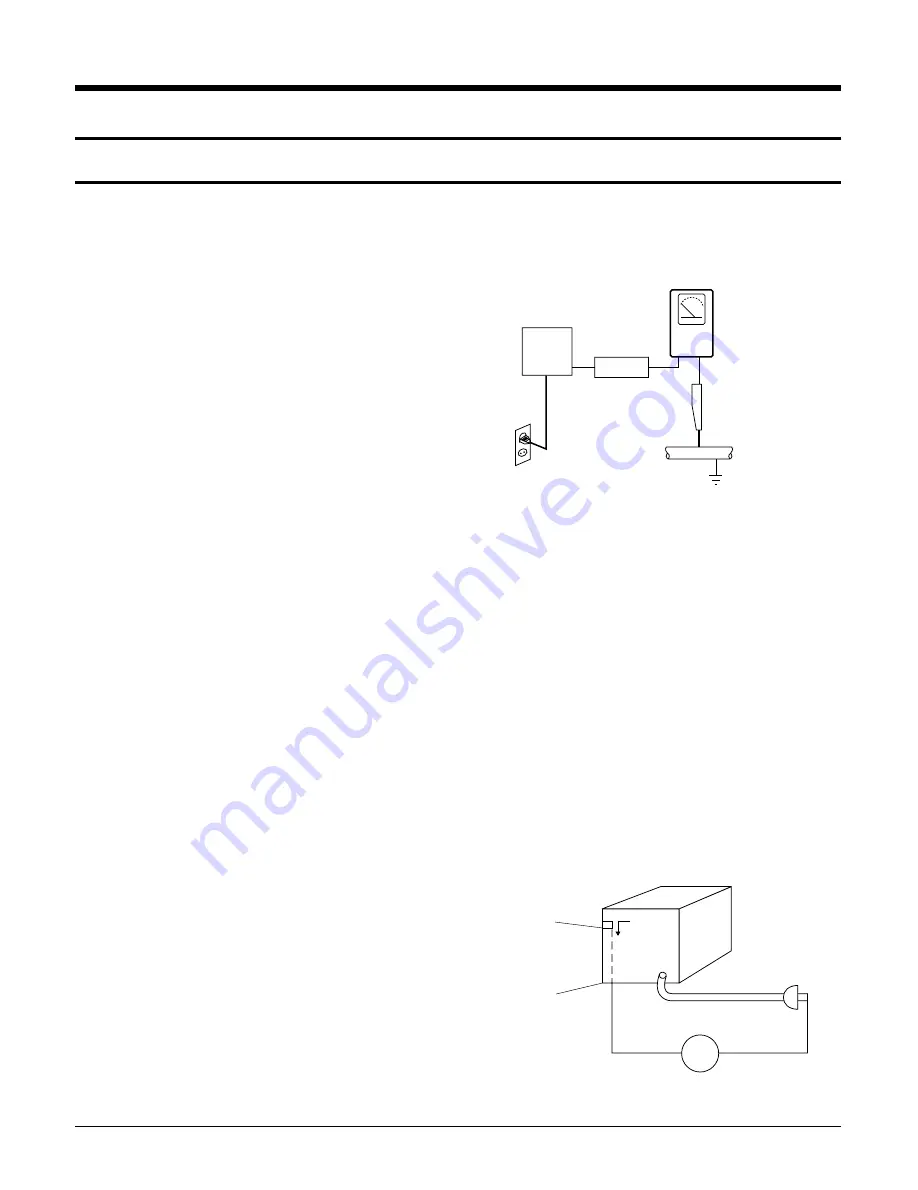
1. Precautions
1-1 Safety Precautions
1) Before returning an instrument to the customer,
always make a safety check of the entire
instrument, including, but not limited to, the
following items:
(1) Be sure that no built-in protective devices are
defective or have been defeated during servicing.
(1)Protective shields are provided to protect both
the technician and the customer. Correctly replace
all missing protective shields, including any
remove for servicing convenience.
(2)When reinstalling the chassis and/or other as-
sembly in the cabinet, be sure to put back in place
all protective devices, including, but not limited to,
nonmetallic control knobs, insulating fish papers,
adjustment and compartment covers/shields, and
isolation resistor/capacitor networks. Do not
operate this instrument or permit it to be operated
without all protective devices correctly installed
and functioning.
(2) Be sure that there are no cabinet openings through
which adults or children might be able to insert
their fingers and contact a hazardous voltage. Such
openings include, but are not limited to,
excessively wide cabinet ventilation slots, and an
improperly fitted and/or incorrectly secured
cabinet back cover.
(3) Leakage Current Hot Check-With the instrument
completely reassembled, plug the AC line cord
directly into a 120V AC outlet. (Do not use a
isolation transformer during this test.) Use a
leakage current tester or a metering system that
complies with American National Standards
institute (ANSI) C101.1 Leakage Current for
Appliances and Underwriters Laboratories (UL)
1270 (40.7). With the instrument's AC switch first
in the ON position and then in the OFF position,
measure from a known earth ground (metal water
pipe, conduit, etc.) to all exposed metal parts of the
instrument (antennas, handle brackets, metal
cabinets, screwheads, metallic overlays, control
shafts, etc.), especially any exposed metal parts
that offer an electrical return path to the chassis.
Any current measured must not exceed 0.5mA.
Reverse the instrument power cord plug in the
outlet and repeat the test. See Fig. 1-1.
Any measurements not within the limits specified
herein indicate a potential shock hazard that must
be eliminated before returning the instrument to
the customer.
Fig. 1-1 AC Leakage Test
(4) Insulation Resistance Test Cold Check-(1) Unplug
the power supply cord and connect a jumper wire
between the two prongs of the plug. (2) Turn on
the power switch of the instrument. (3) Measure
the resistance with an ohmmeter between the
jumpered AC plug and all exposed metallic
cabinet parts on the instrument, such as
screwheads, antenna, control shafts, handle
brackets, etc. When an exposed metallic part has a
return path to the chassis, the reading should be
between 1 and 5.2 megohm. When there is no
return path to the chassis, the reading must be
infinite. If the reading is not within the limits
specified, there is the possibility of a shock hazard,
and the instrument must be re-pared and
rechecked before it is returned to the customer. See
Fig. 1-2.
Fig. 1-2 Insulation Resistance Test
1-1
DEVICE
UNDER
TEST
(READING SHOULD
NOT BE ABOVE
0.5mA)
LEAKAGE
CURRENT
TESTER
EARTH
GROUND
TEST ALL
EXPOSED METER
SURFACES
ALSO TEST WITH
PLUG REVERSED
(USING AC ADAPTER
PLUG AS REQUIRED)
2-WIRE CORD
Antenna
Terminal
Exposed
Melal Part
ohm
ohmmeter
Summary of Contents for DVC-605U
Page 59: ...4 24 Disassembly and Reaasembly MEMO ...
Page 79: ...Circuit Descriptions 5 20 MEMO ...
Page 91: ...Troubleshooting 6 12 MEMO ...
Page 92: ...7 1 7 Exploded View 7 1 Cabinet Assembly 7 2 Deck Assembly Page 7 2 7 3 ...
Page 94: ...Exploded Views 7 3 7 2 Deck Assembly 107 906 108 TS16391 ...
Page 95: ...Exploded Views 7 4 MEMO ...
Page 97: ...8 2 Replacement Parts List MEMO ...
Page 99: ...Block Diagram 9 2 MEMO ...
Page 101: ...PCB Diagrams 10 2 10 1 S M P S ...
Page 102: ...PCB Diagrams 10 3 10 2 Main COMPONENT SIDE SOLDER SIDE ...
Page 103: ...PCB Diagrams 10 4 10 3 Jack ...
Page 104: ...PCB Diagrams 10 5 10 4 Front COMPONENT SIDE SOLDER SIDE ...
Page 105: ...PCB Diagrams 10 6 10 5 Key COMPONENT SIDE SOLDER SIDE ...
Page 106: ...PCB Diagrams 10 7 10 6 Deck 10 8 Sensor 10 7 Motor 10 9 Switch ...
Page 107: ...PCB Diagrams 10 8 MEMO ...
Page 108: ...11 1 11 Wiring Diagram ...
Page 109: ...Wiring Diagram 11 2 MEMO ...
Page 111: ...Schematic Diagrams 12 2 12 1 S M P S ...
Page 112: ...Schematic Diagrams 12 3 12 2 Main Micom ...
Page 113: ...Schematic Diagrams 12 4 12 3 Servo ...
Page 114: ...Schematic Diagrams 12 5 12 4 RF ...
Page 115: ...Schematic Diagrams 12 6 12 5 Data Processor ...
Page 116: ...Schematic Diagrams 12 7 12 6 AV Decoder ...
Page 117: ...Schematic Diagrams 12 8 12 7 Video ...
Page 118: ...Schematic Diagrams 12 9 12 8 Audio ...
Page 119: ...Schematic Diagrams 12 10 12 9 Audio 5 1 Channel ...
Page 120: ...Schematic Diagrams 12 11 12 10 AV Interface ...
Page 121: ...Schematic Diagrams 12 12 12 11 Front Micom ...
Page 122: ...Schematic Diagrams 12 13 12 12 Key ...
Page 123: ...Schematic Diagrams 12 14 12 13 Deck ...
Page 124: ...Schematic Diagrams 12 15 12 14 Motor Switch Sensor ...
Page 125: ...Schematic Diagrams 12 16 12 15 Remote Control ...