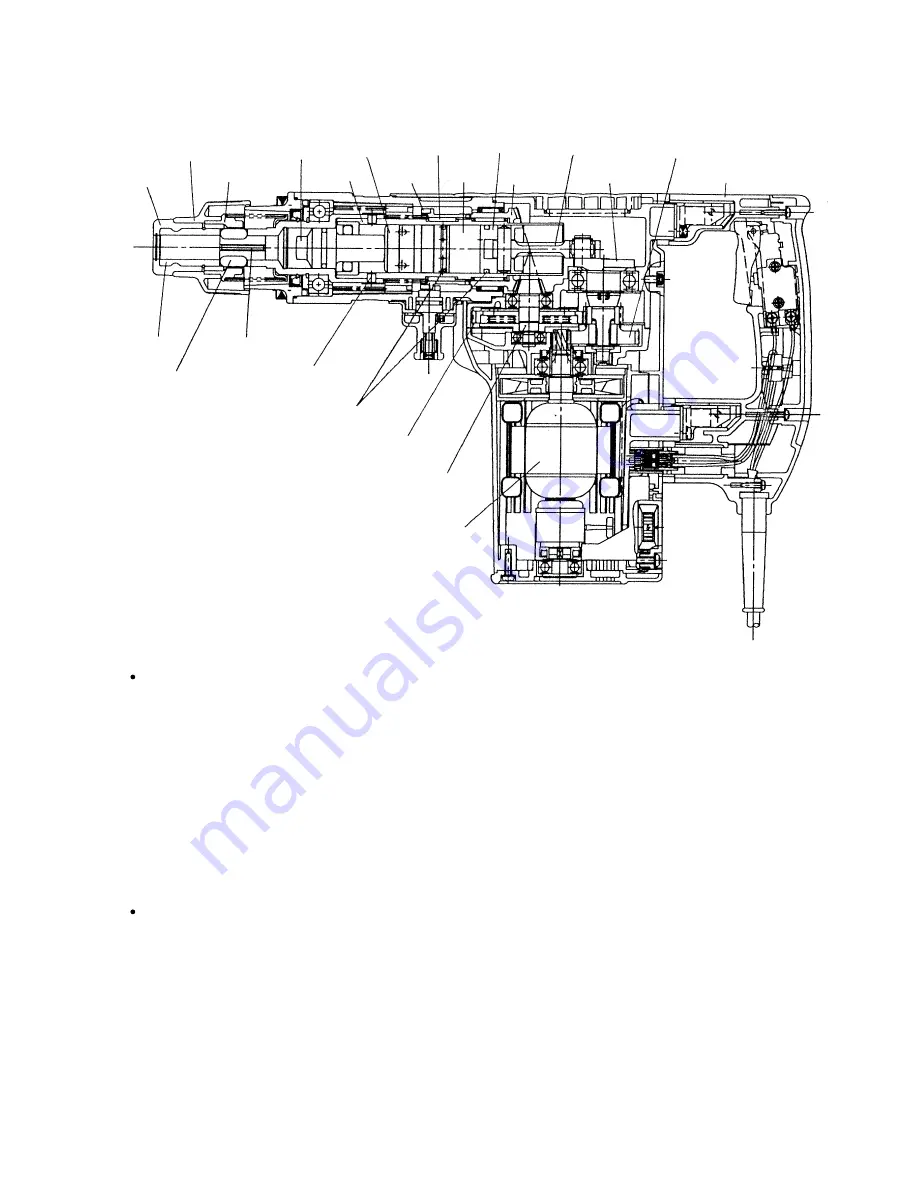
--- 15 ---
Front cap
8-3. Structure of the DH 50MB Hammer Drill
Grip
Bevel
gear
Cylinder
Needle
holder
Second
hammer
Striker
Air
chamber
Key
Piston
Connecting
rod
Crank shaft
First gear
Needle
roller
Retainer
sleeve
O-ring
Second gear
Bevel pinion
Armature
Key slot
Fig. 6
Torque transmission
Rotation transmission is described below with reference to Fig. 6. The gear arrangement of the Model
DH 50MB has the armature shaft positioned between the crank shaft and bevel pinion shaft. Rotation of the
armature shaft is transmitted to the second gear through the first gear of the crank shaft and the second
pinion. Then the rotation is transmitted from the second gear through the slip mechanism disposed between
the second gear and the bevel pinion shaft to turn the bevel gear. The bevel gear is keyed to the cylinder
through the clutch to rotate together. Rotation of the cylinder is transmitted to the retainer sleeve coupled
together by means of four needle pins, and then to the drill bit inserted into the retainer sleeve by way of three
key slots and two needle rollers which couple them together.
Hammering
Armature rotation is transmitted to the crank and connecting rod so that the piston moves reciprocally within
the cylinder. Air pressure developing between the piston and the striker changes with movement of the piston.
The internal pressure thus pushes the striker to repeatedly strike the end face of the second hammer. Since
the striker is moved by means of air pressure, the cushioning effect of the air absorbs the hammering shock
experienced by the operator. If air leaks from the air pressure chamber, the cushioning effect will not be
enough to absorb shock. O-rings fitted around the striker and piston for air sealing therefore play an important
role for the intended function of this hammer drill.
Handle
Needle
pin
Clutch