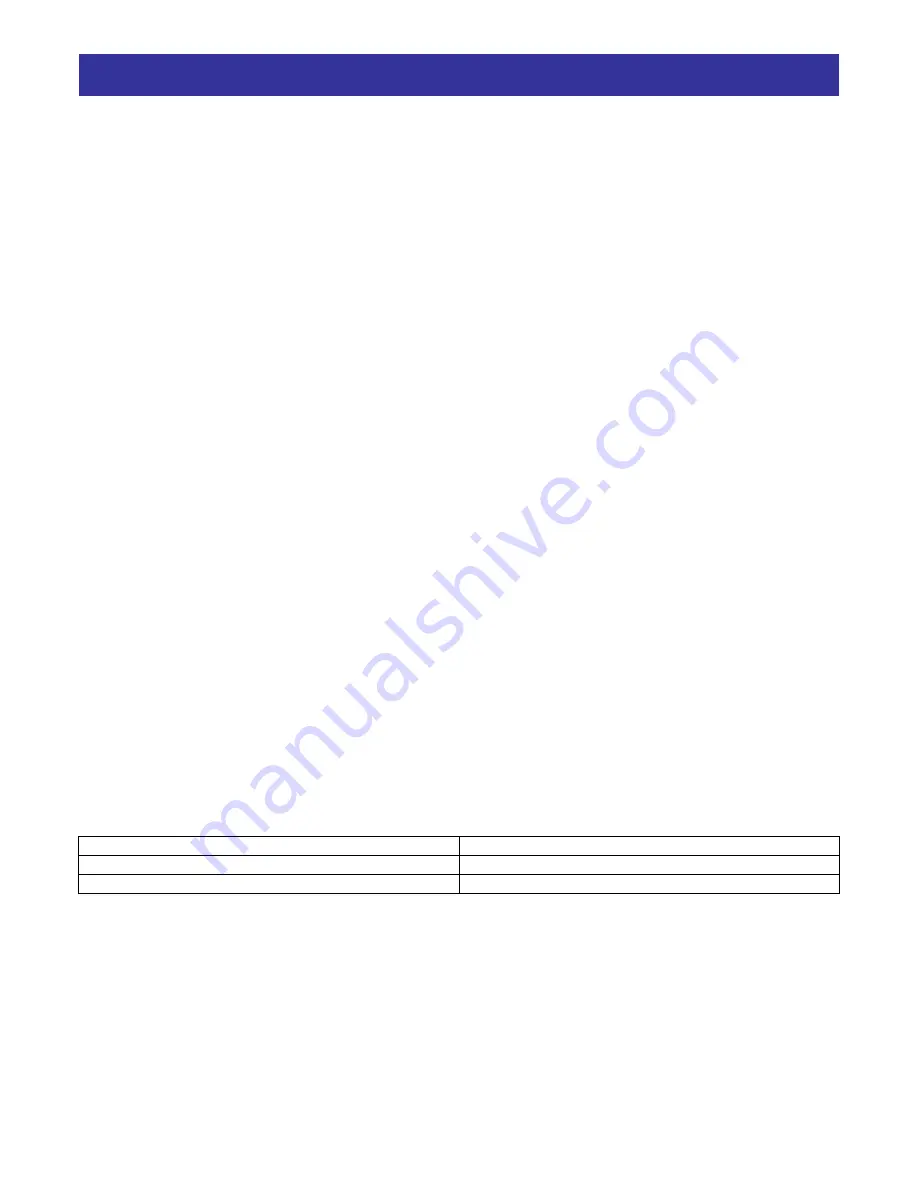
Chapter 4
Page 13 of 16
Chapter 4 – Operation
Normal Operation
Once the inverter parameters are set as described in Chapter 3, you are ready to verify proper operation. It is
recommended to first test the system with the motor mechanically disconnected from the crane or hoist, to
ensure that any unexpected behavior will not damage the equipment or risk injury.
Energize the inverter and the pendant or other external control circuit power supplies, and press the pushbutton
connected to input terminal AC1. This is the UP hoist or FORWARD/LEFT traverse input. Observe motor
rotation. If direction is NOT correct, remove power from the inverter and wait 10 minutes for the capacitors to
discharge. Then interchange any two motor leads. Restore power and repeat the initial test. Direction should
now be correct.
With the AC1 pushbutton pressed to the first detent, the motor will accelerate in the forward direction,
(corresponding to UP motion for the hoist), to the frequency set in A062 (MIN speed), and remain at that speed,
unless:
•
The pushbutton is released, in which case the motor will come to a stop, OR
•
Ramp to a higher speed, while pushbutton is pushed to the second detent (AC3). If AC1 is maintained,
and AC3 is subsequently released, the speed attained at that time will be maintained.
•
Releasing AC1 at this point will cause the motor speed to ramp down.
•
If AC1 remains off long enough, the motor will come to a stop.
•
If AC1 is re-activated at any speed above the MIN speed, then that speed will be maintained for the
duration. If AC1 is reactivated at a speed below the MIN speed, the motor will accelerate to MIN speed
and maintain that speed until one of the above events occurs.
The function of AC2 pushbutton is the same as the AC1 pushbutton, with the exception that rotation direction is
reversed (corresponding to DOWN operation for a hoist).
In addition to its normal function, the AC2 (DOWN) pushbutton input doubles as the FAULT RESET if the
inverter should enter an alarm (trip) condition for any reason. This eliminates the need to access the inverter
keypad itself to clear a fault.
Troubleshooting
Symptom Remedy
Inverter will not accelerate beyond minimum speed
Input AC4 is not jumpered to HOT
Inverter will only turn the motor in one direction Input
AC5
is
not jumpered to HOT
Note: For other troubleshooting tips, refer to Chapter 6 of the pertinent inverter Instruction Manual
Electrical Specifications
The board is internally powered from the inverter’s internal 24 Vdc power supply, drawing approximately 21
mA. The AC inputs are optically isolated, and draw approximately 2 mA each. The outputs to the inverter have a
100 mA maximum capacity.