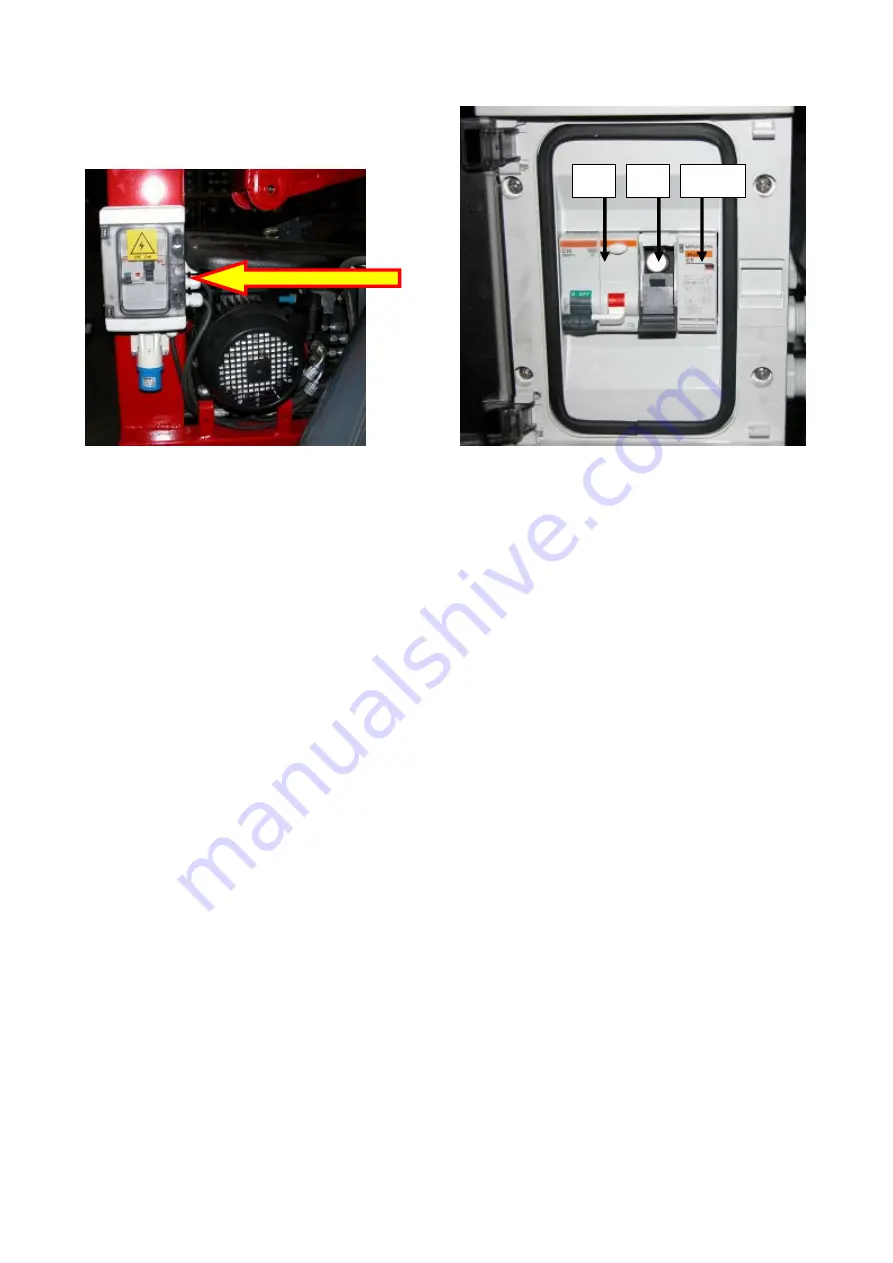
26
(Attachment 5) Outside the board
there is
the electric plug CEE 2P+T 16A that feeds the electric
engine. Through the cables 230L and 230N you enter the Q1 differential switch. Then the cables L
and N connect in parallel the transformer and the relay KM1, that controls the electric engine. When
the PLC closes the contact Q7, the relay KM1 that closes the circuit is powered, and it feeds the
electric engine. The fuse F4 protects the circuit. After of the transformer there is a rectifier that
changes the alternate current into continuous current and feeds the line at low voltage.
From the cables L and N starts a connection that goes to the electric plug CEE 2P+T 16A in the
basket.
4.4 Starter in the basket (gasoline only)
(Attachments 3 and 5) Pushing the starter button on the control panel in the basket, you feed the
cable 6 that is connected with the solenoid located on the
thermic
engine.
4.5 Operations of the platform.
4.5.1 Translation and stabilization
In order to allow the translation, the machine needs to be aligned.
(Attachment 4) The alignment of the photoelectric cell 1 emitter receiver, powers the
relay KA1 and sends a signal to I8 of the PLC; on the contrary, the alignment of the
reflection photoelectric cell powers the relay KA1-A.
The two relays in series close the circuit on the cable 10 that feeds the electrovalve of
the deviator aerial part / undercarriage part. The tension comes also to the control
panel in the basket, where the cable 10 lights the consent lamp for the translation KL4
(Attachment 3).
The electrovalves of undercarriage, aerial part and Jib are protected by the fuse F2.
4.5.2 Aerial work.
In order to work with the aerial part, the machine needs to be stabilized.
(Attachment 2) On the outriggers there are 4
end of stroke
(stops) ST1; ST2; ST3; ST4
that are equipped with a double contact NC and NA. When the 4 stops are released,
the contacts in parallel NA open, and take the feeding away from the entrances I1; I2;
Q1
KM1
F4
Summary of Contents for GOLD LIFT 1470
Page 1: ...Technical Course GOLD LIFT 1470 ...
Page 3: ...3 ...