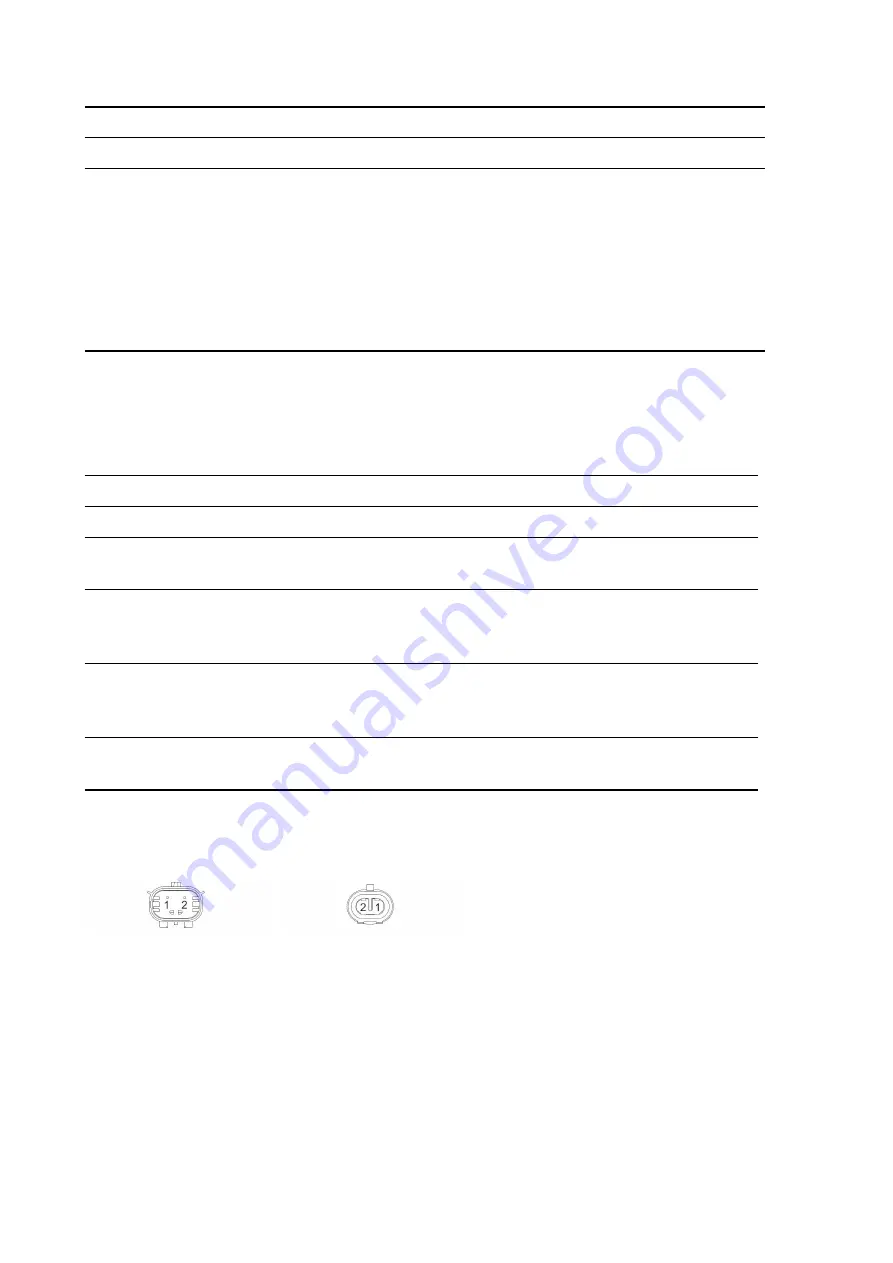
Set-up of Charging Curve
DP1 DP2 DP4 Set Up
Yellow LED
Green LED Flash
OFF OFF OFF IUI0-Pb Flooded
OFF
1
ON
ON
OFF IUoU-Gel Trojan
OFF
2
OFF ON
OFF IUoU-AGM GEL
OFF
3
ON
OFF OFF IUI0-Gel Sonnenschein
OFF
4
OFF OFF ON
IUIa-Pb Flooded
ON
1
ON
ON
ON
IUI0-AGM EV-Discover
ON
2
OFF ON
ON
IUa-AGM Zenith
ON
3
ON
OFF ON
IUIa-Gel Sonnenschein
ON
4
Error Codes of Charger
The charger have an alarm system through successive flashes of the yellow LED.
Error code
Flash
Description
1
Battery not connected or reverse polarity or output short circuit.
Verify the battery connection.
2
Alarm time-out: damaged battery or battery capacity is too high
The alarm is reset disconnecting the main supply. If it persists consult your
service.
3
Faulty battery charger
The alarm is reset disconnecting the main supply. If it persists consult your
service.
4
Overtemperature
The alarm is reset when the charger cools. Verify the ventilation.
Charger Cables Detail
1 Battery -
2 B
1 COM Relay contact
2 N.C. Relay contact
37
Summary of Contents for TRIDENT T26SC PLUS
Page 1: ...SERVICE MANUAL TRIDENT T26SC PLUS Version AB Date November 7 2018 Document Number 10077484...
Page 4: ...Part I Product Introduction 4...
Page 8: ...Part II Anomalies Resolution Guide 8...
Page 28: ...Part III Machine Description 28...