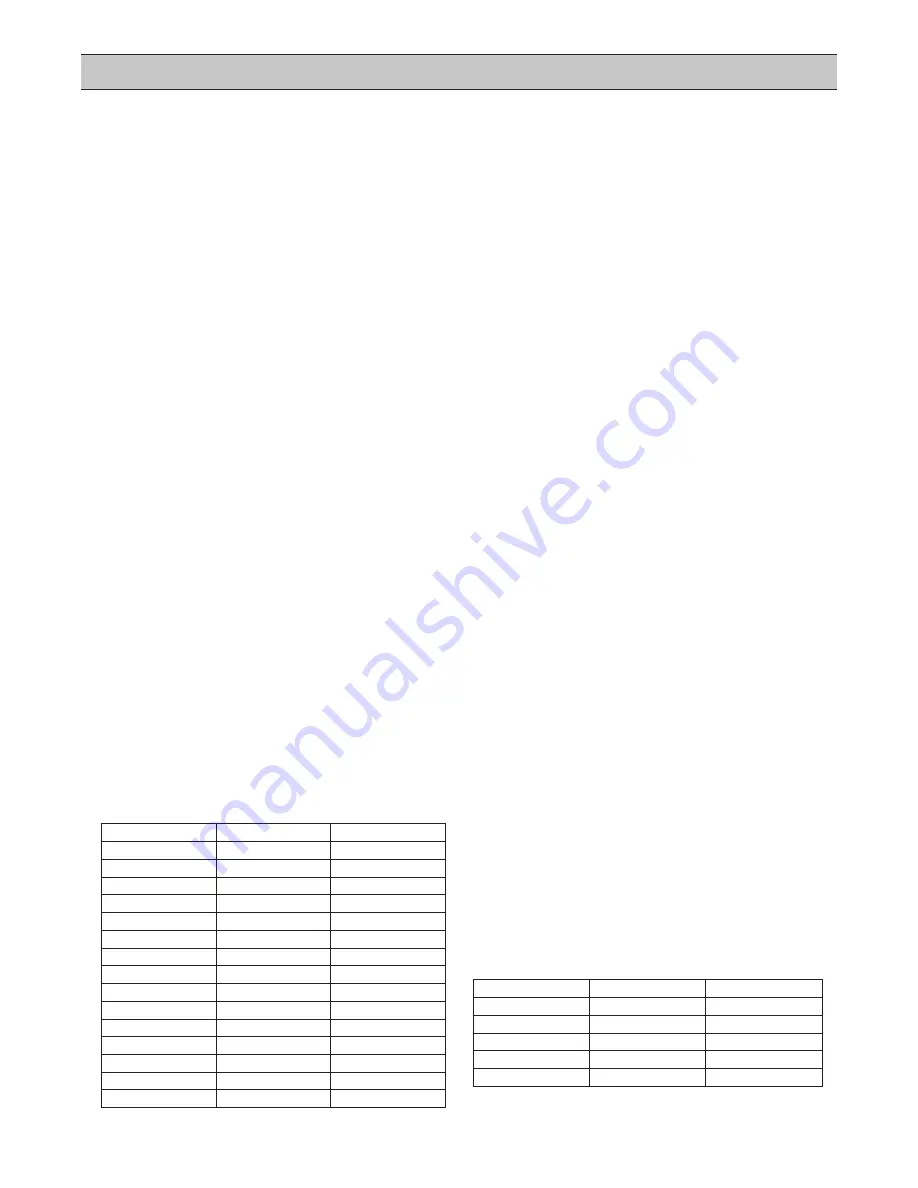
18
APPENDICES B & C
A
B
̴
H
V
W
:
Natural
cord wood does not come with a speci
fi
ca on sheet like
the building materials described in Appendix C. Manu-
factured products can be made to strict, repeatable tol-
erances. Natural wood, on the other hand, varies con-
siderably depending on where it grows, the climate, the
mineral composi on of the soil, and more. Even s ll,
considerable research and scien
fi
c data is available on
di
ff
erent varie es of wood. Added to the varia ons in
the wood itself is the fact that
fi
re wood is sold by vol-
ume; most typically by the cord. As discussed in Appen-
dix A, a cord measures 4' wide X 4' high X 8' long or 128
cubic feet. Beyond those facts it begins to get murky.
The amount of burnable wood that will be available in
a given cord can vary greatly on how it is cut, whether
it is split, the sizes of the whole or split logs, and the
skill (or perhaps the integrity) of the person stacking
the wood. An apocryphal story a ributed to a Vermont
wood burner avers that well stacked wood will have spac-
es large enough for a mouse to crawl through but not
large enough for the cat chasing him. Well stacked wood
should be @ 85% wood and 15% air space. The air spac-
es are necessary to ensure proper drying. (FYI there is a
lively debate amongst experienced wood burners wheth-
er the bark side of the split wood should be up or down.)
Bark up or down the wood must be well seasoned (@
20% moisture) to be considered good
fi
rewood. Burning
green wood is ine
ffi
cient and disappoin ng; cu ng the
BTU values given below approximately in half.
Below is an abbreviated chart that gives some approxi-
mate weight and BTU values for various species of wood.
More comprehensive lists are available on line, but a
word or two of cau on. The sta s cs can vary widely
depending on the source or, more likely, on the point
they are trying to make. The numbers can be easily ma-
nipulated by changing assump ons. If a cord of wood is
assumed to have 30% air space then the es mated avail-
able BTU's will be considerably less. Likewise, assuming
that a pound of wood at 20% moisture contains say 8000
available BTU will net an appealing, inaccurate number.
In researching data we found the varia ons considerable.
Use the numbers below as a point of comparison be-
tween species available to you, not as a score card. The
best advice is to
fi
nd an honest wood vendor and rely on
them to deliver a full cord of the best wood available.
Buy your wood well ahead of the burning season, dry it
and keep it dry, and enjoy clean e
ffi
cient wood heat.
W
S
L .
C
BTU
C
American Elm
@ 3000 lbs.
@ 20,000,000
Apple
@ 3800 lbs.
@ 27,000,000
Cherry
@ 2925 lbs.
@ 20,500,000
Hemlock
@ 2700 lbs.
@ 18,000,000
Hickory
@ 4200 lbs.
@ 27,000,000
Red Oak
@ 3500 lbs.
@ 24,500,000
Shagbark Hickory
@ 4325 lbs.
@ 27,500,000
Sugar Maple
@ 3750 lbs.
@ 24,000,000
Tamarack
@ 3250 lbs.
@ 21,000,000
White Ash
@ 3500 lbs.
@ 24,000,000
White Birch
@ 3200 lbs.
@ 20,000,000
White Cedar
@ 1915 lbs.
@ 12,500,000
White Oak
@ 4200 lbs.
@ 29,000,000
White Pine
@ 2250 lbs.
@ 15,000,000
Willow
@ 2100 lbs.
@ 14,500,000
All values are approximate and for comparison only.
A
C
̴
F
W
P
:
UL Stan-
dard 1618; the Standard for Wall Protectors, Floor Protec-
tors, and Hearth Extensions, was adopted as a standard
in 2011. UL-1618 categorizes
fl
oor and wall protectors as
Type 1 or Type 2 protec on. A seemingly minor change
in UL 1618 calls for the actual thermal proper es of
fl
oor
protec on to be speci
fi
ed in R-value in place of k-value.
In fact, that change makes it one step simpler to calculate
thermal protec on if it becomes necessary.
• Type 1: Ember Protec on = No thermal value
• Type 2: Thermal Protec on = R-value speci
fi
ed
Type 1 Ember Protec on is deemed to be a con nuous
non-combus ble material extending under the appliance
and to the front , sides, and back in the size speci
fi
ed. Any
thermal value a Type 1 protector may have is disregarded
under UL-1618. Type 2 Thermal Protec on provides ther-
mal resistance in addi on to ember protec on. Thermal
value is determined by laboratory test. UL-1618 calls for
thermal requirements to be expressed as R-values rather
than as k-values which were used in the past.
If a hearth or
fl
oor protec on is to be built on-site, or
there is an exis ng hearth already in place, then the ther-
mal resistance must be calculated. This is where having
thermal requirements expressed as an R-value vs. k-value
simpli
fi
es calcula ons. R-values can be added together.
• R-value is a unit of measure of Thermal Resistance. It
is best known as the common measure of insula on.
As with insula on, the higher the number, the be er.
• k-value is a unit of measure of Thermal Conduc vity.
k-value is the opposite (inverse) of R-value in that the
smaller the k-value the greater the resistance.
R-values for di
ff
erent materials can be added together to
determine the total R-value of composite layers of mate-
rials and k-values cannot. Conver ng k-value to R-value
is rela ve simple but it tends to add some confusion. (It
should be noted that there are other units of measure,
such as C-value, Thermal Conductance, but they are not as
commonly used in hearth applica ons.) So, again, if only
the k-value is given, then it must be converted to R-value.
(Keep in mind that the
k-value is given per inch of materi-
al.)
To convert k-value to R-value divide 1 by the k-value of
the material and
divide by the thickness of the material.
C-
values can also be converted to R-values (1 ÷ C-value) and
R-values can also be converted to k-value (inches ÷ R) but
by staying with R-values materials can be added together.
Floor protec on requirements were once commonly ex-
pressed as "3/8" of asbestos millboard k = 0.84" or similar.
The conversion is: 1 ÷ 0.84 = 1.19 X 0.375" = 0.45 R-value.
Today, with the R-value given, consider this example:
A wood heater requires R = 1.19. If 4" common brick is the
material of choice; their R-value is 0.80 (0.20 X 4"). Add
1/2" of Durock (R = 0.26) and the protec on is s ll not ad-
equate (R = 1.06). Add one more layer of 1/2" Durock and
the
fl
oor protec on is now acceptable (R = 1.32). (Brick,
le, etc. must be mortared in place, not loose laid.)
M
R-
-
Common Brick
R = 0.20 per inch k = 5.00 per inch
Durock
R = 0.52 per inch k = 1.92 per inch
Hardibacker
R = 0.51 per inch k = 1.95 per inch
Micore 160
R = 2.86 per inch k = 0.86 per inch
Marble
R = @0.09 per "
k = @11 per inch
More complete lists of material speci
fi
ca ons and more detailed
explana ons of calcula ons can be found online.