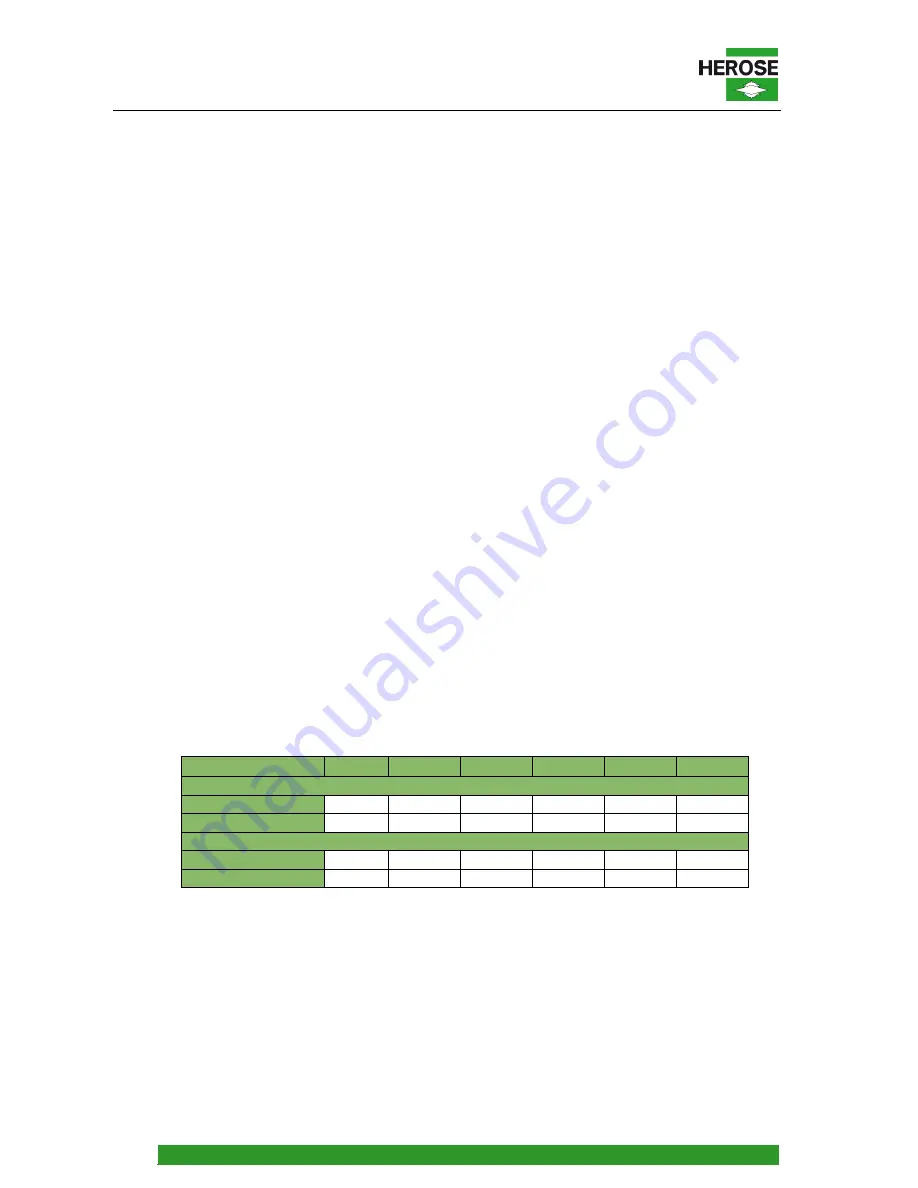
Operating instructions
10
Phone +49 4531 509-0
5
Assembly
5.1
Installation position
Vertical
From 20 to 300 bar in the horizontal installation position, with the outlet facing downwards.
5.2
Notes regarding the installation
Use suitable tools.
Open-ended spanners
Torque wrench
Clean tools before the installation
Open the packaging only directly before the installation. Freedom from oil and grease for oxygen
(O
2
)
Safety valves for oxygen are permanently marked with "O
2
".
Only install the safety valve if the maximum operating pressure and usage conditions correspond
to the marking on the safety valve. Take note of the p-t curve of the valve on the catalogue page
and the resulting areas of use.
Remove protective caps or covers before installing.
Inspect the safety valve for dirt and damage.
DO NOT
install damaged or dirty safety valves.
Remove any dirt and residues from the pipeline in order to avoid leaks.
Use the entire usable thread length for mounting; at least four thread pitches.
Avoid damaging the connections.
The sealing surfaces must remain clean and intact.
Seal the safety valve using suitable seals.
No sealant (sealing tape, liquid sealing tape) may enter the safety valve.
Respect the suitability for use with O
2
.
Connect pipelines in a force-free and torque-free manner.
Stress-free installation.
In order to ensure trouble-free operation, no impermissible static, thermal or dynamic stresses
may be transmitted to the safety valve. Observe reactive forces.
The safety valve is supported by the pipeline system.
The safety valve must be protected against dirt and damage during construction work.
Check leak-tightness after completion of mounting.
Tightening torques
The tightening torques specified by the manufacturer are maximum permissible values at room
temperature and with uniform thread mating. The real torque to be used depends on the screw-in
conditions in the plant and must be specified by the plant operating company.
Thread
1/2"
3/4"
1"
1 1/4"
1 1/2"
2"
Inlet
M
A
[Nm] – max. perm. tightening torque
G
120
230
440
1300
1700
-
R / NPT
150
270
500
800
1000
-
Outlet
M
A
[Nm] – max. perm. tightening torque
G
70
110
220
340
430
640
R / NPT
180
280
530
850
1100
1700