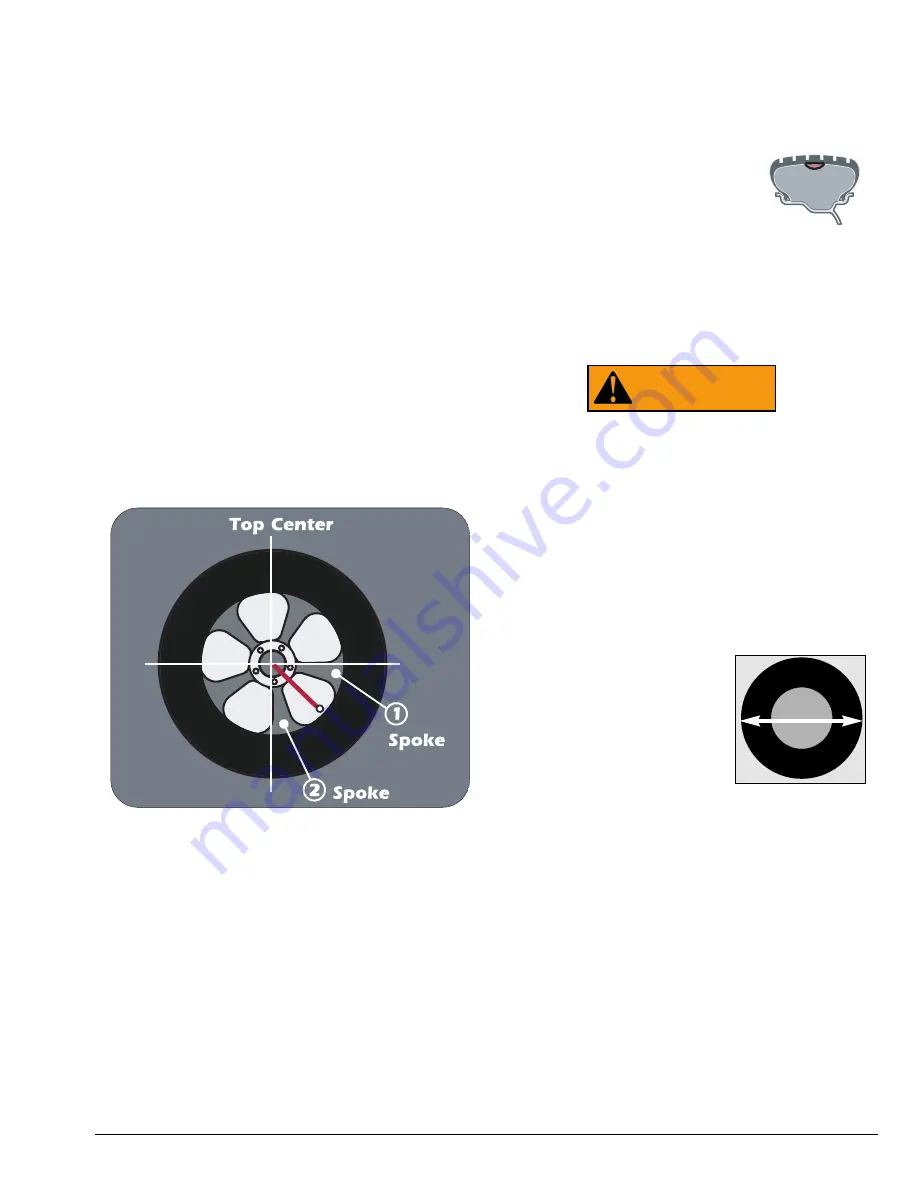
Important: Always read and follow the information box instructions.
• 13
Begin by following the Laser Guided Operation™ pro-
cedure, steps 1 through 4 on page 7.
1.
When the unbalance is displayed, rotate the wheel
until the left plane center bar blinks. Attach the left
plane corrective weight at top-dead-center.
2.
Next, rotate the wheel until the right plane center
bar blinks and the two bars on either side blink.
Note:
The laser locator dot will stop blinking.
3.
Select the BEHIND SPOKE mode option.
Important:
Be sure that the Spoke 1 and Spoke 2
locations are on either side of the original right plane
corrective weight location, as shown in figure 14.
4.
Rotate the wheel toward front so the laser locator
dot is behind the first spoke; press SPOKE 1 (LED illu-
minates).
5.
Rotate the wheel toward rear so the laser locator
dot is behind the second spoke; press SPOKE 2 (LED
illuminates). Now at the spoke 2 location, the right
plane center bar stops blinking and the two bars on
either side blink.
Note:
The laser locator dot will stop blinking.
Figure 14 - Spoke 1 And Spoke 2 Locations On Either Side Of
Original Right Plane Weight Location
6.
Center and attach the spoke 2 right plane correc-
tive weight at the laser locator dot location (see figure
10 page 7).
7.
Next, rotate the wheel toward the spoke 1 location
until the right plane center bar stops blinking and the
two bars on either side blink.
Note:
The laser locator dot will stop blinking.
8.
Center and attach the spoke 1 right plane correc-
tive weight at the laser locator dot location (see figure
10 page 7).
9.
Respin tire/wheel to check balance.
Patch Weight Balance -
Use a static patch weight bal-
ance when there is a very large unbalance in a tire
assembly or if a very large tire has a large unbalance. A
weighted balance pad (patch weight) is placed inside the
tire in the center to compensate for the large unbalance.
Direct Select Weight position
Patch
Static
(weight LED illuminates). At this
location place the corrective weight
amount at top-dead-center.
Have the following items handy: measuring tape and
various patch weight sizes.
Note:
Before proceeding with Patch Weight Balance,
it is recommended that you use the Match Balance
(Optimization) procedure first, see page 16, in order to
use the smallest patch weight.
The Patch Weight Balance involves the loos-
ening of tire beads and the inflation of a tire.
Training is necessary in tire changer opera-
tion and understanding the dangers
involved during bead seating and tire infla-
tion before attempting this stage of the
Patch Weight Balance procedure. Read the
operators manual supplied with the tire
changer and consult a supervisor.
The patch weight balance steps are as follows:
1.
Direct Select Weight position PATCH STATIC. The
balancer automatically sets itself for a STATIC balance.
2.
Measure the outside tire
diameter, see figure 15, and enter
this diameter manually using the
keypad.
Figure 15 - Measure Outside Tire
Diameter
3.
Move the offset arm tip to the inside of rim to set
weight location. Wait for beep.
4.
Spin the wheel.
5.
Rotate the wheel until the center weight position
LED bar is blinks. Next, mark the tire and rim at 12
o’clock. Then remove the wheel assembly from the
machine.
6.
Disassemble the tire and rim. Place patch weight
in the tire at location marked on the tire. Reassemble
tire and rim matching the marks on the tire and rim.
7.
Complete by balancing the wheel assembly fol-
lowing normal procedures.
WARNING
Outside
Diameter