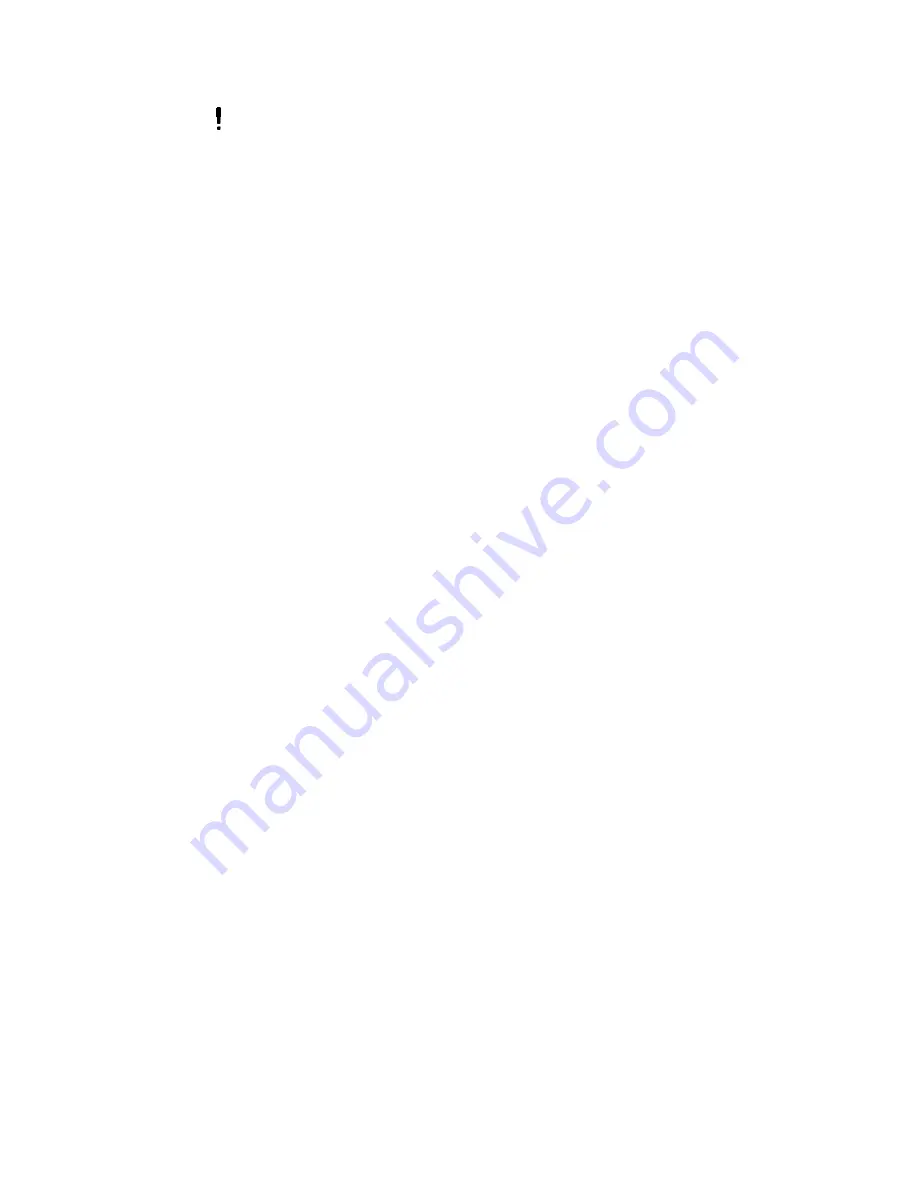
11
Adjustment of this pressure switch should be made with the power off and
appropriate lock-out tag-out measures.
The adjustment is made using the adjustment wheel located in the center of the
pressure switch. Approximate pressure setting can be determined by the markings
on the pressure switch calibration scale. Adjustment of the setting is made by
turning the wheel clockwise and counterclockwise.
A more accurate setting of the pressure switch can be made using a multi-meter.
Set the multi-meter to continuity or resistivity and connect the probes to
terminals 1 and 2 of the level control.
Adjust the indicator toward the pressure connection or beyond the desired
pressure set point by turn the adjustment wheel clockwise.
Start with the regulator adjusted to zero. Multi-meter should have
continuity or read 0 ohms.
Adjust the regulator until the pressure gauge reads the desired set point of
the pressure switch.
Turn the adjustment wheel counterclockwise until the switch actuates.
Multi-meter should not have continuity or read open circuit (infinite ohms).
Adjust the regulator to lower the pressure until the switch actuates on from
the decreasing pressure. Multi-meter should have continuity or read 0
ohms.
For a more precise pressure setting; increase and decrease pressure setting
to cycle the pressure switch a few times while making fine adjustments with
the pressure switch wheel.
5.3 Adjusting Regulator Pressure on Master Level Control
Each Master Level Control has a pressure regulator with filter mounted on the side
of the enclosure. A 0…30 psig gauge provides pressure reading of the regulator
outlet to the level controller flow regulators. Outlet pressure must be at least 5 psig
greater than the maximum downstream pressure from the flow regulator.
5.3 Adjusting Flow Regulator
With supply air pressure on adjust the needle valve to produce the desired bubble
rate. The bubble rate is dependent on the volume of air in the system and fluid
Summary of Contents for 2250048 REV
Page 1: ...E CO Level Control 120 VAC One Two Three and Four Points Operating Manual ...
Page 2: ......
Page 25: ...21 9 3 2251340 REV E CO Level MSTR 2 PT electrical ...
Page 26: ...22 9 4 2251339 REV E CO Level STD 2 PT electrical ...
Page 27: ...23 9 5 8907225 Master Level Control Three Point electrical ...
Page 28: ...24 9 6 8907224 Standard Level Control Three Point electrical ...
Page 29: ...25 9 7 8907227 Master Level Control Four Point electrical ...
Page 30: ...26 9 8 8907226 Standard Level Control Four Point electrical ...
Page 31: ...27 9 9 Level Control Standard and Master Installation Drawing 8907228 ...