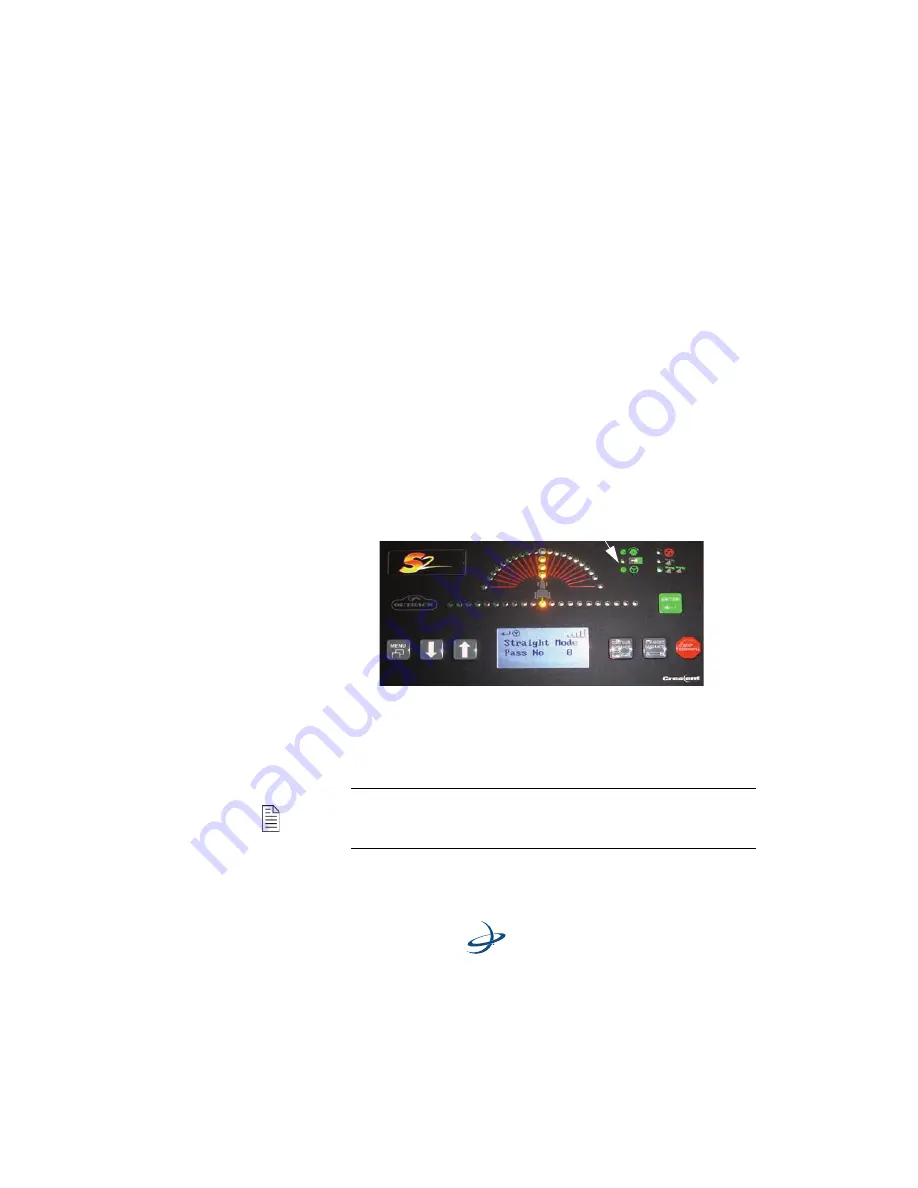
eDriveTC User Guide
29
Auto-Engage
The Auto-Engage
TM
feature is optional. It allows the vehicle operator to
turn around at the end of one pass, line up on the next guideline, and
automatically re-engage eDriveTC
without pressing the ENTER button.
The auto-engage feature may be turned on or off through the eDriveTC
setup menu.
To operate with the auto-engage:
1.
Initiate guidance and manually engage the eDriveTC, using the
normal operating procedure.
2.
At the end of the pass, manually steer off the guideline to auto-
disengage eDriveTC. The eDriveTC indicator light will begin
flashing.
3.
Turn the vehicle around and manually steer to the next pass. Center
both the current position and steering guide
TM
lights for one
second. The eDriveTC
will automatically re-engage and the
eDriveTC indicator light will turn on solid.
Note:
If you continue to manually steer after the vehicle is on
the guideline, the eDriveTC will sense the movements in the
steering wheel and disengage.
eDriveTC indicator light
Summary of Contents for eDriveTC
Page 1: ...Outback eDrive User Guide Part No 875 0171 Rev C1 ...
Page 3: ......
Page 9: ...iv ...
Page 10: ...1 Overview Product Overview What s Included Parts Listing ...
Page 13: ...4 1 Overview Parts Listing ...
Page 15: ...6 1 Overview ...
Page 16: ...2 Getting Started Overview Installing the eDriveTC Powering the Unit System Configuration ...
Page 32: ...3 eDriveTC Operation Guidance Overview Auto Disengage Auto Engage ...
Page 40: ...4 Troubleshooting Fine Tuning Performance Troubleshooting Tips Vehicle Type Setup Table ...
Page 65: ...56 Appendices ...
Page 66: ...www hemispheregps com e mail info hemispheregps com ...