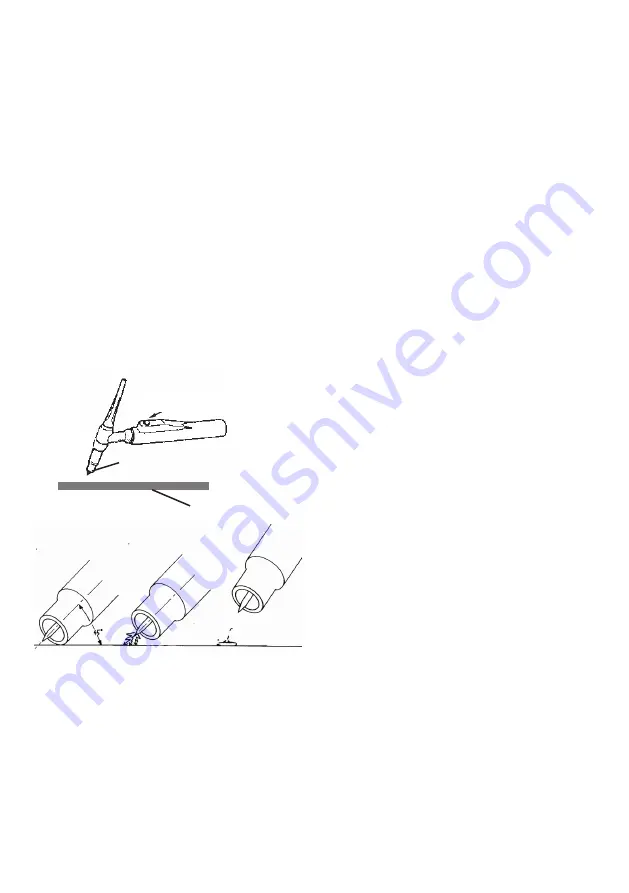
EN-14
FIG.b
FIG.c
FIG.d
- Set the welding current considering the
thickness of the material to be welded and of
the diameter of the tungsten electrode to be
used.
-
Covering your face with a mask or a hel
-
met, touch with the isolating nozzle the work
piece and bring the tungsten electrode of the
torch within 3 or 4 mm keeping it at an an
-
gle of 45° (fig. b). Push the torch trigger (fig.
a).The arc will be light from a high voltage
spark(fig. c ).
NOTES:
a) The arc length generally varies between 3
and 6mm depending on the type of joint, type
and thickness of material, and so on.
b) The torch is advanced in the direction of
welding, without lateral movement, maintai
-
ning the torch angle of 45° to the workpiece.
ORDINARY MAINTENANCE
CAUTION!!!
BEFORE CARRY OUT ANY MAINTENAN-
CE, UNPLUG THE MACHINE FROM THE
MAINS POWER SUPPLY.
The efficiency of the welding system over
time is directly related to the frequency of
maintenance jobs, such as:
For welding machines only need to be ta
-
ken care inside. The dustier the working en
-
vironment is, the more often this should be
done.
- Take off the lid.
- Remove all traces of dust in the inner
parts of the generator with a jet of compres
-
sed air at a pressure under 3Kg/cm.
- Check all electrical connections, making
sure that nuts and screws have been firmly
tightened.
- Do not delay in replacing worn-out parts.
- Put the lid back on.
- After completing the above operations,
the generator is ready to be restarted fol
-
lowing the instructions given in this manual.
FIG. a
HF Spark
Torch Trigger
Workpiece
SHORT CIRCUIT PROTECTION
FUNCTION
•
In the event that the tungsten electrode
touches the workpiece during welding, the
current will drop to 0 in 1s to protect the elec
-
trode.
•
Protection against the arc interruption; in
the event that the arc is interrupted, the high
frequency will keep the arc stable;