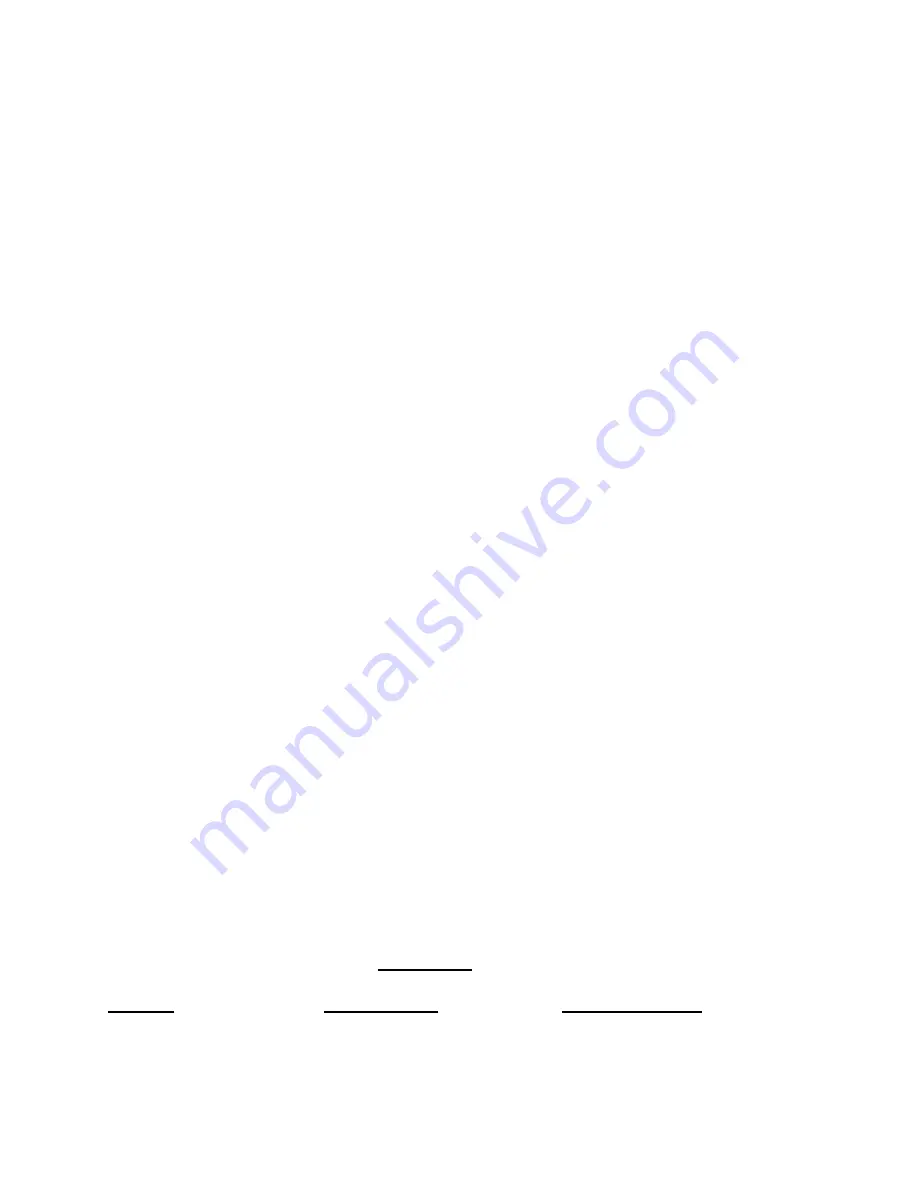
1-360008/G
21
3.
On a quarterly basis lightly lubricate the basket assembly lift-out rail. This is done by placing no
more than 2 or 3 drops of a light duty oil (not grease) on your finger and rubbing the oil up and
down the rail. Apply the thin coat of lubrication to each of the 4 sides on both lift-out rails.
Troubleshooting
Main Power
Problem Possible
Cause
Action to be taken
Unit does not turn on
- Circuit breaker activated
- Reset circuit breaker
- Faulty outlet connection
- Verify power outlet is good