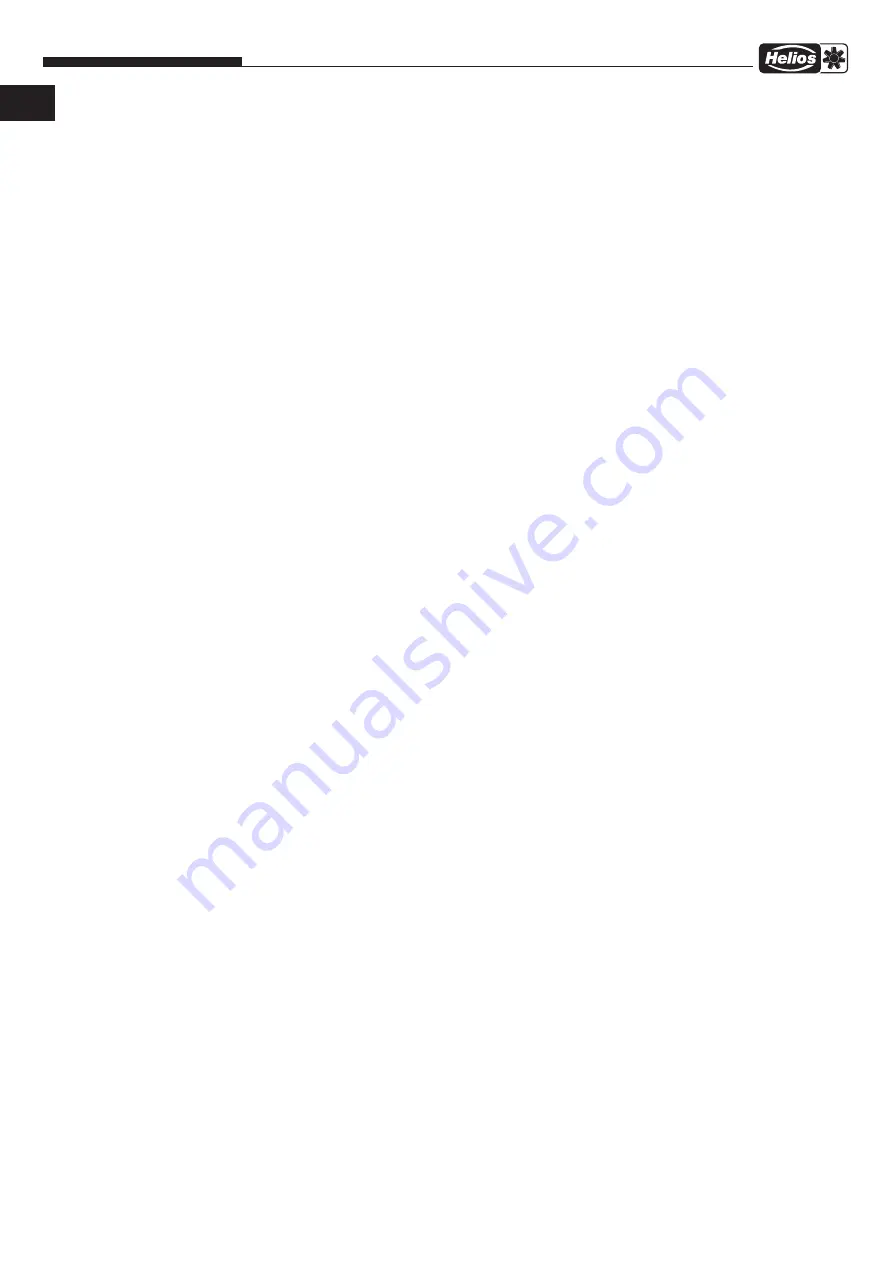
26
Smoke exhaust fan control system –
EVS
Installation and Operating Instructions
–
Reactivate smoke detector again.
The system deactivates and the signal lamp “Ready” lights up again.
Test plan:
Quarterly : Functional inspection by the operator or instructed personnel
5 .1 Maintenance
Mechanical smoke extraction systems must undergo functional inspections as well as tests and maintenance at regular
intervals. These measures to ensure the functionality of mechanical smoke extraction systems are essential for the use of
buildings or the operation of systems. This also includes the accessories used for the system, controlled elements as well as
components and parts for system activation and the energy supply devices, etc.
The system operator is responsible for the timely implementation of functional inspections, tests and maintenance.
The operator of a mechanical smoke extraction system that has not been regularly maintained can be held responsible for
negligent personal injury or involuntary manslaughter among other things.
The system operator must keep a logbook. Information regarding the operation of the system (activations, faults, etc.) as well
as performed maintenance, functional inspections and servicing must be recorded in this logbook.
The causes for fault and/or error signals must be promptly investigated and rectified by specialist companies with qualified
personnel authorised by Helios.
Necessary repair and servicing work must be carried out immediately by specialist companies with qualified personnel au-
thorised by Helios.
In order to guarantee any required or desired response times, it is generally recommended to conclude a corresponding
maintenance agreement with a specialist company with qualified personnel authorised by Helios for these safety-related
systems.
The test and maintenance intervals are regulated in the country-specific inspection directives. Furthermore, the intervals
for functional inspections, tests and maintenance must be observed according to the specifications in the Helios test and
maintenance plan.
A functional inspection, test and maintenance also includes all accessory components, the power supply and controls, etc.,
in addition to the actual system.
All functional inspections, tests and maintenance must be recorded in a logbook, and measured readings must be docu-
mented. All documents must be kept by the system operator.
The performance of tests, maintenance and expert tests must be indicated by a label, stamp, etc. on the control cabinet.
Regularly and properly carried out tests and maintenance must be proved in the event of a warranty claim. In case of the
improper performance or exceedance of time intervals for tests and maintenance, all warranty claims will be lost.
Maintenance plan:
Annually: Maintenance by authorised specialist company with qualified personnel
5 .2 Repairs/Servicing
Necessary repairs and servicing work must be carried out immediately. The responsibility for this lies with the system ope-
rator.
The deactivation of the system in case of servicing may only be carried out by qualified specialist personnel in coordination
with the operator.
The duration of deactivation must not endanger personal safety.
The deactivation of the system in the context of servicing, modification, renovation, change of use, etc. is not permitted
without a risk analysis. Coordination with the competent building authority is essential and must be arranged by the operator.
The operating licence of the building can expire due to the deactivation of the system.
5 .3 Onboard diagnosis and control elements
The status of the system and all detector circuits is displayed via a comprehensive visual onboard diagnosis:
–
Operating mode (ready for operation, activated and fault)
–
Per detector circuit, whether it has been triggered or there is a fault
–
Fault signal to the isolator switch and motor protection device
Control board overview
The control board has an automatic circuit breaker B6A and two microfuses 5 x 20: F1 = 2A M and F2 = 0.4A M.
EN
Summary of Contents for EVS Series
Page 9: ...7 Entrauchungsventilatoren Steuerung EVS Montage und Betriebsvorschrift EVS D DE ...
Page 10: ...8 Entrauchungsventilatoren Steuerung EVS Montage und Betriebsvorschrift EVS D DE ...
Page 11: ...9 Entrauchungsventilatoren Steuerung EVS Montage und Betriebsvorschrift EVS D DE ...
Page 12: ...10 Entrauchungsventilatoren Steuerung EVS Montage und Betriebsvorschrift EVS D DE ...
Page 13: ...11 Entrauchungsventilatoren Steuerung EVS Montage und Betriebsvorschrift EVS SD DE ...
Page 14: ...12 Entrauchungsventilatoren Steuerung EVS Montage und Betriebsvorschrift EVS SD DE ...
Page 15: ...13 Entrauchungsventilatoren Steuerung EVS Montage und Betriebsvorschrift EVS SD DE ...
Page 16: ...14 Entrauchungsventilatoren Steuerung EVS Montage und Betriebsvorschrift EVS SD DE ...
Page 17: ...15 Entrauchungsventilatoren Steuerung EVS Montage und Betriebsvorschrift EVS DA DE ...
Page 18: ...16 Entrauchungsventilatoren Steuerung EVS Montage und Betriebsvorschrift EVS DA DE ...
Page 19: ...17 Entrauchungsventilatoren Steuerung EVS Montage und Betriebsvorschrift EVS DA DE ...
Page 20: ...18 Entrauchungsventilatoren Steuerung EVS Montage und Betriebsvorschrift EVS DA DE ...
Page 21: ...19 Entrauchungsventilatoren Steuerung EVS Montage und Betriebsvorschrift EVS W DE ...
Page 22: ...20 Entrauchungsventilatoren Steuerung EVS Montage und Betriebsvorschrift EVS W DE ...
Page 23: ...21 Entrauchungsventilatoren Steuerung EVS Montage und Betriebsvorschrift EVS W DE ...
Page 62: ...30 Smoke exhaust fan control system EVS Installation and Operating Instructions ...
Page 63: ...31 Smoke exhaust fan control system EVS Installation and Operating Instructions ...