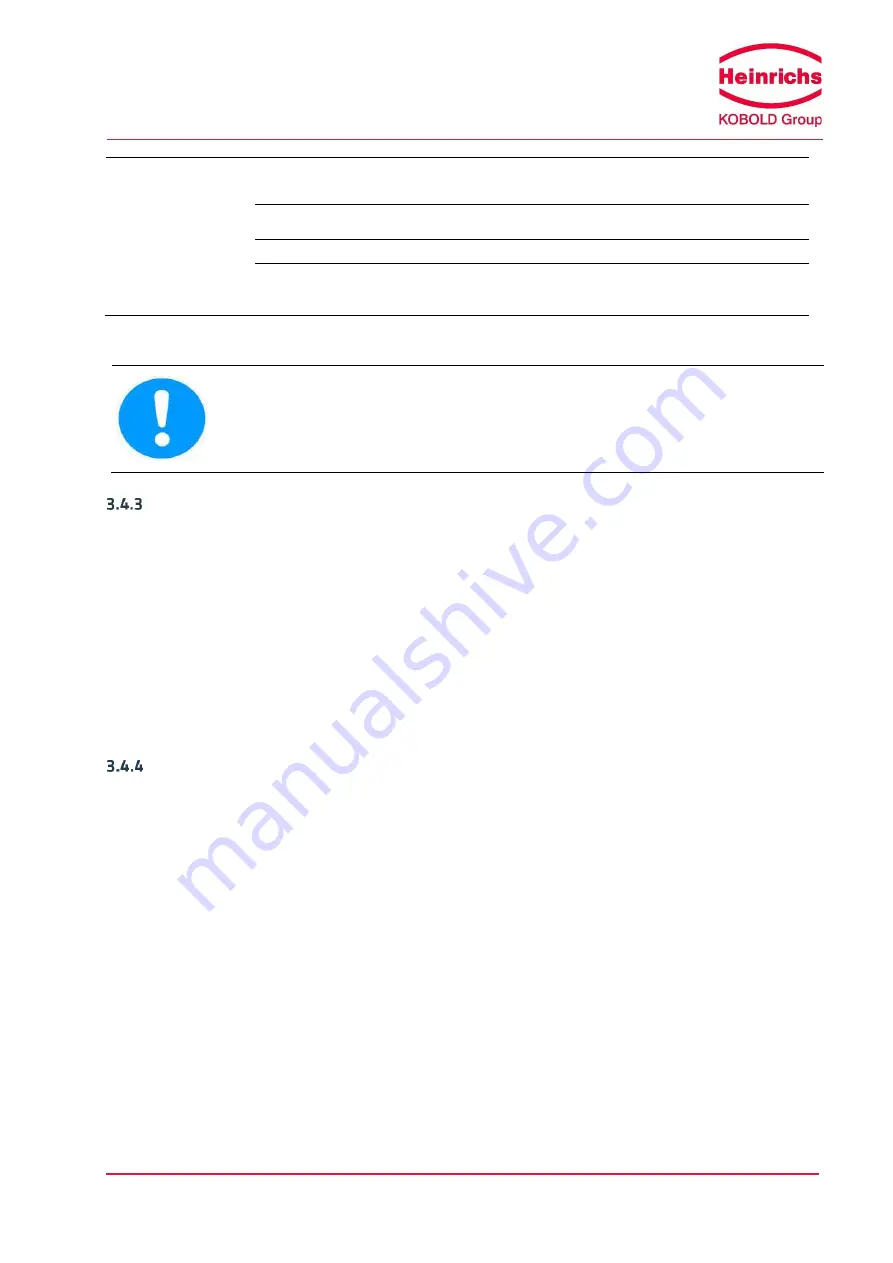
Heinrichs Messtechnik GmbH
OPERATING MANUAL TMU / UMC3
Page 21 of 122
Slurries
Standard installation
position
Optimal installation position
Position A
High density substances could accumulate in the flowmeter
Position B
Gas bubbles could accumulate
Position C
Gas bubbles or high density substances could accumulate in
the flowmeter
Table 5: Sensor Installation Orientations
Caution:
When mounted in the horizontal orientation (B), it is to be ensured that moisture or rain
cannot accumulate on the top surface of the device.
Pressure surges
Pressure surges in a pipe could be provoked by a sudden decrease in flow caused by rapid closing of a valve or
similar factors. This change in pressure can lead to negative-pressure downstream from a valve that has been
closed rapidly and to outgassing. If the valve is mounted directly on the inlet section of the flowmeter, a gas
bubble can form in the flow tube that can cause a measuring signal disturbance that would shift the zero point
of the output signal. In extreme cases, a pressure surge could cause mechanical damage to the sensors and/or
flow tube.
Whenever possible, quick-closing valves should be mounted downstream from the sensor. If this is not
feasible, such valves are to be mounted a minimum of 10 x DIA (
Φ
) from the nearest sensor. Alternatively, valve
closing speed can be reduced.
Using the device with hazardous fluids
The sealing technology used for the standard TMU mass flowmeter renders the device unsuitable for use with
hazardous fluids. Only sensors that meet the standards for safety instruments and which are declared as such
are suitable for use with hazardous fluids.
In such sensors, a pressure-tight duct in the pathway between the sensor and transmitter prevents fluid from
leaking out of a sensor in the event a sensor develops a defect.
In the case of welded containments, a coloured liquid penetration test can be performed on the welds, or the
first seam of the weld can be x-rayed.
Alternatively, an internal pressure-monitoring device can be used to detect ruptured pipes.