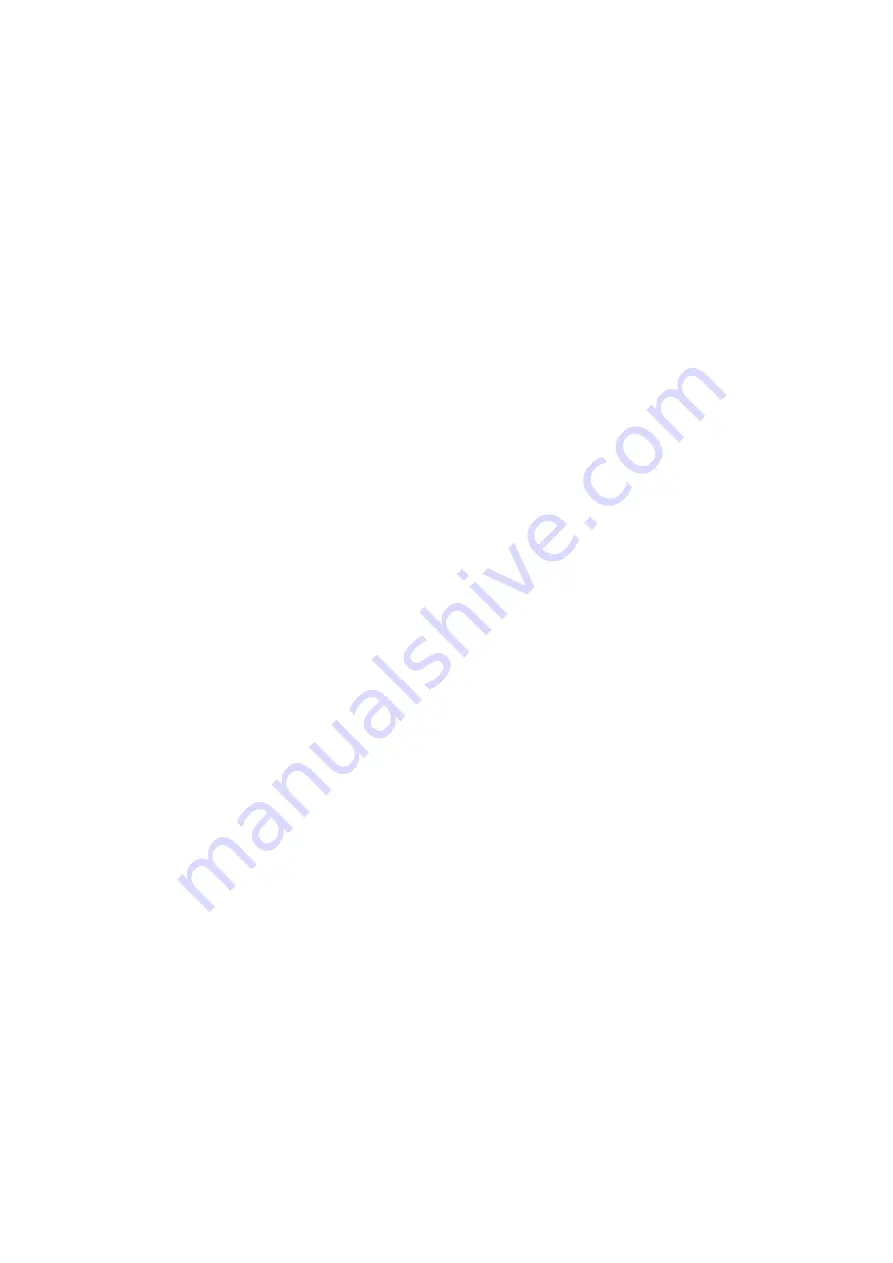
Operation
ABC
3–2
Edition September 2005
Automatic Startup
Note: When switched on, the Suprasetter 74/105
needs approx. 30 minutes to reach its operating tem-
perature. For that reason, it has an automatic startup
mechanism that can be used to switch on the device
at defined periods, for example, a half an hour before
shift work starts. The startup time is set at the work-
station.
Prerequisites:
0
The power switch of the Suprasetter 74/105 is set
to 'I'.
0
The Suprasetter 74/105 GUI is running.
Operation:
1. Click the "Device" button in the Suprasetter 74/105
GUI.
2. Click "Configuration" in the vertical menu bar.
3. Select the "Timer" tab.
4. Select "Switch on Timer".
5. Set the startup cycle you want in "Schedule" in the
"Settings" box.
6. Set the switch-on time you want in "Start Time" in the
"Settings" box.
Note: If you selected "Once" in "Schedule", you can also
set the startup day in addition to the start time in
"Schedule Once".
7. Click "Apply". The startup time is saved and the Supra-
setter 74/105 will switch itself on at this time.
2
5
2
Summary of Contents for Suprasetter 106
Page 6: ......
Page 16: ......
Page 22: ......
Page 70: ...Technical Data ABC 5 12 Edition September 2005 Image 1 ...
Page 71: ...ABC Technical Data Suprasetter 74 105 Operation 5 13 Image 2 11 ...
Page 72: ...Technical Data ABC 5 14 Edition September 2005 Image 3 13 12 ...
Page 73: ...ABC Technical Data Suprasetter 74 105 Operation 5 15 Image 4 14 15 ...
Page 74: ...Technical Data ABC 5 16 Edition September 2005 Image 5 16 17 ...
Page 75: ...ABC Technical Data Suprasetter 74 105 Operation 5 17 Image 6 18 25 ...
Page 76: ...Technical Data ABC 5 18 Edition September 2005 Image 7 19 26 20 ...
Page 77: ...ABC Technical Data Suprasetter 74 105 Operation 5 19 Image 8 22 23 21 ...
Page 81: ...6 7 1 5 2 3 6 8 1 6 4 ...
Page 82: ......
Page 83: ......
Page 84: ......
Page 90: ......