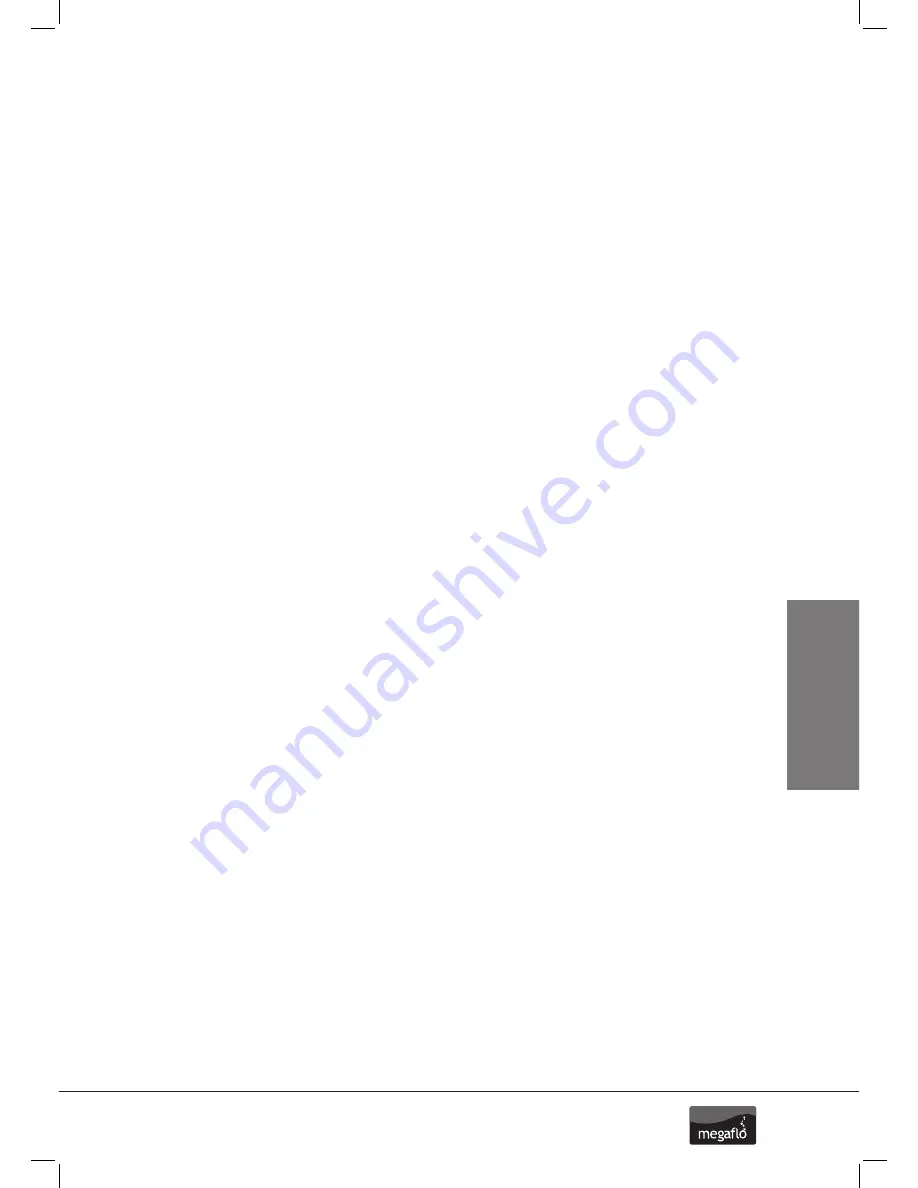
MAINTENANCE
37
Maintenance
Maintenance requirements
To ensure the continued optimum performance of the Megaflo Eco SolaReady it should be regularly maintained. This is of particular
importance in hard water areas or where the water supply contains particulate matter. Maintenance should be carried out by a
competent person and any replacement parts used should be authorised Megaflo Eco SolaReady spare parts. It is recommended
that maintenance is carried out every 12 months and includes the checks detailed below.
In hard water areas consideration should be given to periodically descaling the immersion heater elements. To do this the Megaflo
Eco SolaReady unit will need to be drained, details below list how to drain the unit and remove the immersion heater(s).
Inspection
The immersion heater boss can be used as an access for the inspection of the cylinder internally.
Check operation of Safety Valves
Slowly open the Temperature and Pressure Relief Valve by twisting its cap for a few seconds. Check water is discharged and that it
flows freely through the tundish and discharge pipework. Check valve reseats correctly when released.
NOTE: The water discharged may be very hot.
Repeat the procedure for the 8 Bar Pressure Relief Valve.
Clean the strainer
The strainer is incorporated within the Pressure Reducing Valve housing of the Cold Water Combination Valve (see Figure 28, page
43). To inspect and clean the strainer:
Turn off the isolating valve on the 3 Bar Pressure Reducing Valve by turning the blue handle (if fitted in this position) so it lies 90º to
the direction of flow or main stop cock to the house.
Open the lowest hot tap in the system to relieve the system pressure.
Using a spanner unscrew the pressure reducing cartridge and remove the moulded housing. The strainer will be removed with the
cartridge.
Wash any particulate matter from the strainer under clean running water.
Replace the strainer and screw the Pressure Reducing Valve cartridge into the moulded housing.
Close hot tap, turn on isolating valve by turning handle so it lies parallel to the direction of flow. Check for leaks.
Draining the Megaflo Eco SolaReady unit
Switch off the electrical supply to the immersion heater(s) and shut down the boiler on indirect units. Turn off the mains water
supply to the Megaflo Eco SolaReady unit. Attach a hosepipe to the drain cock having sufficient length to take water to a suitable
discharge point below the level of the unit, at least one metre below the unit is recommended. Open hot water tap nearest to the
Megaflo Eco SolaReady to relieve the system pressure. Open drain cock. If water fails to drain from the Megaflo Eco SolaReady vent
the unit by manually opening the Temperature / Pressure Relief Valve.
Descaling immersion heater(s)
Open the cover(s) to the immersion heater housing(s) and disconnect wiring from immersion heater(s). Disconnect the two wires
to the element tabs. Remove the thermostat capillaries, 2 or 4 depending on which unit being serviced. Unscrew immersion heater
backnut(s) and remove immersion heater from the unit. A key spanner is supplied with the Megaflo Eco SolaReady unit for easy
removal / tightening of the immersion heater(s). Over time the immersion heater gasket may become stuck to the mating surface.
To break the seal insert a round shafted screwdriver into one of the pockets on the immersion heater and gently lever up and down.
Carefully remove any scale from the surface of the element(s). DO NOT use a sharp implement as damage to the element surface
could be caused. Ensure sealing surfaces are clean and seals are undamaged, if in doubt fit a new gasket.
Replace immersion heater(s) ensuring the lower (right angled) element hangs vertically downwards towards the base of the
unit. It may be helpful to support the immersion heater using a round shafted screwdriver inserted into one of the thermostat
pockets whilst the backnut is tightened. Replace the thermostat(s) by carefully plugging the two male spade terminations into the
corresponding terminations on the element.
Rewire the immersion heater(s) in accordance with Figure 14, page 17 or Figure 15, page 18. Close and secure terminal cover(s).
Expansion Vessel Charge Pressure
Remove the dust cap from the top of the expansion vessel. Check the charge pressure using a tyre pressure gauge.
The charge pressure (with the system depressurised) should be 0.3MPa (3 bar). If it is lower than the required setting it should be
re-charged using a tyre pump (schrader valve type). DO NOT OVER CHARGE. Re-check the pressure and when correct replace the
dust cap.
Summary of Contents for Megaflo Eco SolaReady
Page 49: ...SERVICING 49...
Page 51: ...SERVICING 51...