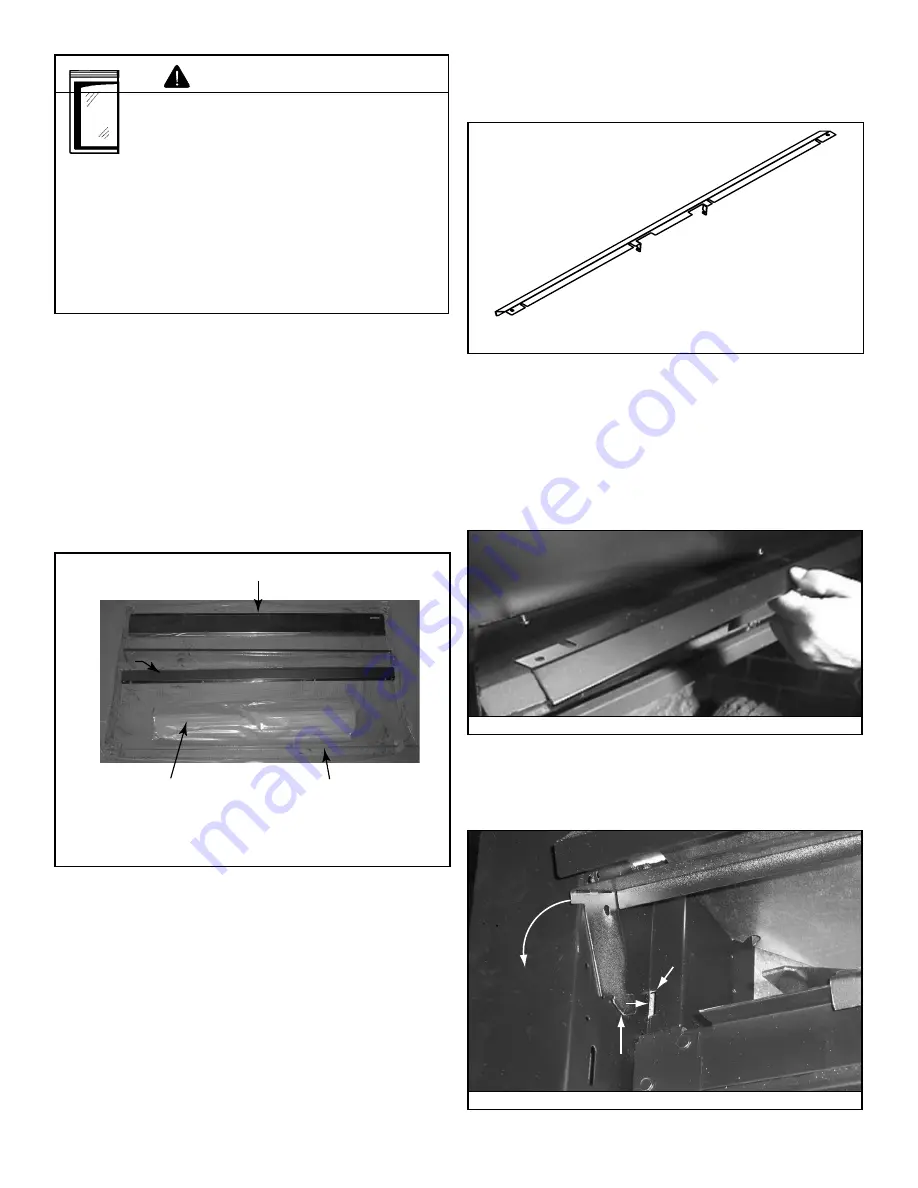
Heatilator • Novus Mesh DV • 4031-552 Rev I • 11/07
45
Figure 12.5 Installing the Hood
Bottom Latch Cover
Firescreen
(Lower Floor Cover-not shown-
shipped underneath)
Firescreen Rod
Hood
Top Latch Cover
Figure 12.3 Clean Face Components/Skin Pack
G. Replace Glass Assembly
• Set the glass panel on the lower two or four glass assembly
latches, ensuring the glass panel is centered in the
opening.
• Pull out and latch all four or seven glass assembly latches
into the groove on the glass frame.
Handle glass with care.
• Inspect the gasket to ensure it is
undamaged.
• Inspect the glass for cracks, chips or
scratches.
• Do NOT strike, slam or scratch glass.
• Do NOT operate appliance with glass
assembly removed, cracked, broken or
scratched.
• Replace glass assembly as a complete
assembly.
WARNING
H. Install Clean Face Components
Carefully remove components from skin pack. See Figure
12.3 for identi
fi
cation of components.
Install Hood
• Bend screen rod tabs down at a 90-deg. angle. See Figure
12.4.
Figure 12.4 Screen Rod Tab
• Install above the glass panel.
• Hood must be attached or a
fi
re hazard may result.
• Locate the four screws just inside the upper section of the
appliance.
• Position hood and slide notches over screw heads.
• Tighten the four screws.
• See Figure 12.5.
Install Top Latch Cover
• Insert top latch cover tabs into slots. See Figure 12.6.
• Rotate top latch cover down till the tabs lock in place.
Top Latch
Cover Tab
Slot
Figure 12.6 Installing Top Latch Cover
Summary of Contents for ND4842MI
Page 65: ...Heatilator Novus Mesh DV 4031 552 Rev I 11 07 65 This page intentionally left blank...
Page 84: ...84 Heatilator Novus Mesh DV 4031 552 Rev I 11 07 This page intentionally left blank...
Page 85: ...Heatilator Novus Mesh DV 4031 552 Rev I 11 07 85 This page intentionally left blank...
Page 86: ...86 Heatilator Novus Mesh DV 4031 552 Rev I 11 07...