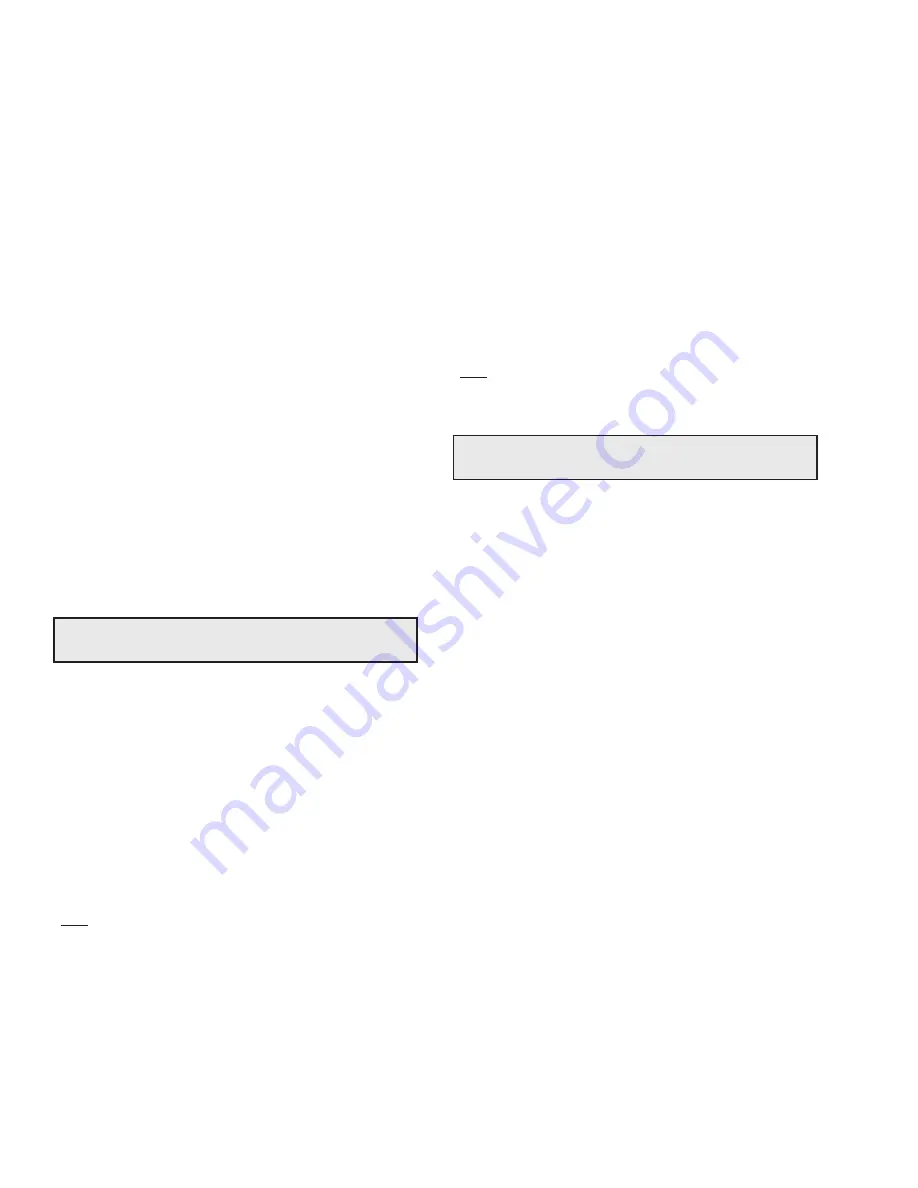
10
© 2015 Heatcraft Refrigeration Products, LLC
Evacuation and Leak Detection
Due to the smaller molecule size of HFC’s, they will tend to leak more readily than
CFC’s. Consequently, it is of the utmost importance that proper system evacuation and
leak detection procedures be employed.
Manufacturer recommendation is a minimum of 500 micron evacuation. In addition,
a vacuum decay test is strongly recommended to assure there is not a large
pressure differential between the system and vacuum pump. Good evacuation
processes include frequent vacuum pump oil changes and large diameter, short hose
connections to both high and low sides of the system preferably using bronze braided
hose. Leak detection can be carried out in the conventional manner. If HCFC or CFC
tracer gas is used, care must be taken to completely remove all traces of the gas prior
to introducing HFC’s.
Electronic leak detectors are now available that will sense HFC’s. This is considered
preferable since it removes the possibility of chlorine remaining in the system after
leak testing with HCFC’s and/or CFC’s. There is a view that even small quantities of
chlorine may act as a catalyst encouraging copper plating and/or corrosion and should
therefore be avoided.
Leak Testing
After all lines are connected, the entire system must be leak tested. The complete
system should be pressurized to not more than 150 psig with refrigerant and
dry nitrogen (or dry CO
2
). The use of an electronic type leak detector is highly
recommended because of its greater sensitivity to small leaks. As a further check
it is recommended that this pressure be held for a minimum of 12 hours and then
rechecked. For a satisfactory installation, the system must be leak tight.
Line Insulation
After the final leak test, refrigerant lines exposed to high ambient conditions should
be insulated to reduce heat pickup and prevent the formation of flash gas in the liquid
lines. Suction lines must always be insulated with 3/4" wall Armstrong “Armaflex” or
equal. When required, Liquid lines should be insulated with 1/2 inch wall insulation or
better. The insulation located in outdoor environments should be protected from UV
exposure to prevent deterioration of insulating value.
Evacuation
A good, deep vacuum pump should be connected to both the low and high side
evacuation valves with copper tube or high vacuum hoses (1/4" ID minimum). If the
compressor has service valves, they should remain closed. A deep vacuum gauge
capable of registering pressure in microns should be attached to the system for
pressure readings.
A shut off valve between the gauge connection and vacuum pump should be provided
to allow the system pressure to be checked after evacuation. Do not turn off vacuum
pump when connected to an evacuated system before closing shut off valve.
The vacuum pump should be operated until a pressure of 1,500 microns absolute
pressure is reached — at which time the vacuum should be broken with the
refrigerant to be used in the system through a drier until the system pressure rises
above “0” psig.
Repeat this operation a second time.
Open the compressor service valves and evacuate the entire system to 500 microns
absolute pressure. Raise the pressure to 2 psig with the refrigerant and remove the
vacuum pump.
Refrigerant Charging Instructions
1. Install a liquid line drier in the refrigerant supply line between the
service gauge and the liquid service port of the receiver.
2. This extra drier will insure that all refrigerant supplied to the
system is clean and dry.
3. When initially charging a system that is in a vacuum, liquid
refrigerant can be added directly into the receiver tank.
4. Check equipment catalog for refrigerant capacity. System
refrigerant capacity is 90% of receiver capacity. Do not add more
refrigerant than the data tag indicates, unless the line run exceeds
25ft. Then, add additional refrigerant as per the chart on page 30.
Weigh the refrigerant drum before charging so an accurate record
can be kept of the weight of refrigerant put in the system.
5. Start the system and finish charging until the sight glass indicates
a full charge and the proper amount has been weighed in. If the
refrigerant must be added to the system through the
suction side of the compressor, charge in vapor form only. Liquid
charging must be done in the high side only or with
liquid metering devices to protect the compressor.
NOTE:
R-407c should be introduced into the system as a liquid.
Field Wiring
The field wiring should enter the areas as provided on the unit. The wiring diagram for
each unit is located on the inside of the electrical panel door. All field wiring should
be done in a professional manner and in accordance with all governing codes. Before
operating unit, double check all wiring connections, including the factory terminals.
Factory connections can vibrate loose during shipment.
1. The serial data tag on the unit is marked with the electrical characteristic
for wiring the unit.
2. Consult the wiring diagram in the unit cooler and in the condensing unit
for proper connections.
3. Wire type should be of copper conductor only and of the proper
size to handle the connected load.
4. The unit must be grounded.
CAUTION:
Do not use the refrigeration compressor to evacuate the
system. Do not start the compressor while it is in a vacuum.
WARNING:
All wiring must be done in accordance with applicable
codes and local ordinances.
NOTE:
Refrigerant used during evacuation cannot be vented. Reclaim all used
refrigerant. EPA regulations are constantly being updated. Ensure your procedure
follows correct regulations.