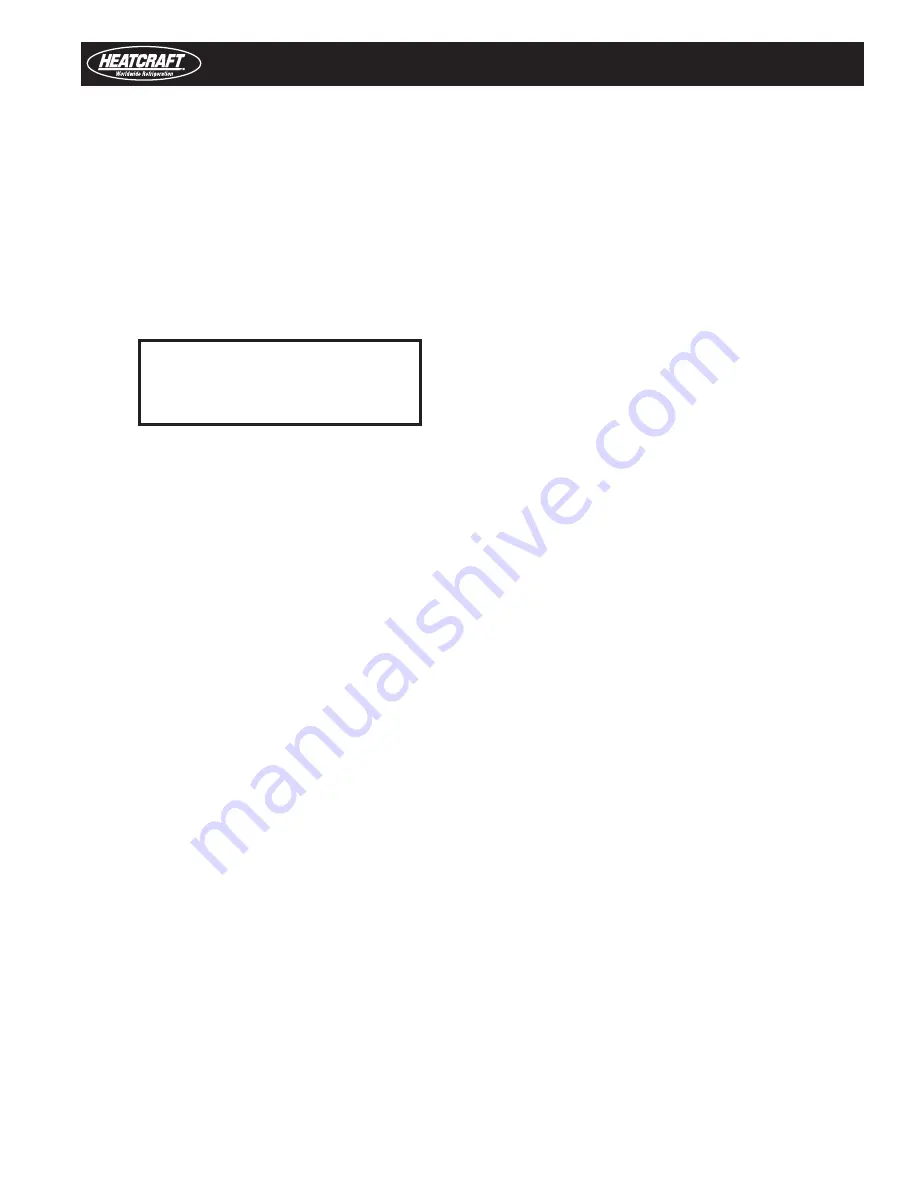
3
Installation Tips
•
Use a minimum 18 gauge wire for all low
voltage connections.
•
The Heatcraft Quick Response Controller board
gets its 24 VAC power supply from a transformer
mounted in the electrical end of each evaporator.
On 208-240 volt systems, the multi-tap transformer
is shipped from our factory wired for 240 volts. If
your supply voltage is 208 volt, you must change to
the 208 volt tap on the transformer.
NOTE:
On multiple evaporators, since a
transformer is in each evaporator, the
voltage tap must be set on each evaporator.
•
Refer to wiring schematic shipped on units for unit
wiring. Schematics in this Installation & Operation
Manual are typical wiring schematics only.
•
Program ALL slave evaporators as SLAVES.
•
Evaporators are shipped from our factory with a
preset box setpoint temperature of 35°F for air
defrost and -10°F for electric defrost. If your box
setpoint temperature requirements are different,
this must be set using directions outlined under
“Room Temperature Control”.
• The suction line temperature sensor MUST be
removed from the suction line before brazing the
suction tubing. The sensor MUST then be reinstalled
on the suction line after brazing is completed and
the tubing has cooled. Insulate when finished.
• If electrical power will be connected prior to
evacuation and charging of system, unplug electric
expansion valve from board until system is ready to
be evacuated, leak tested and charged.
•
There are built-in ground connections on the
Heatcraft Quick Response Controller’s four corner
brass spacers. Use four sheet-metal screws to
mount the board on the evaporator for common-
mode noise filtering. Make sure that the evaporator
ground terminal is earth grounded.
Installation
• Some systems may require the crankcase heater
be energized 24 hours prior to start-up. The
Heatcraft Quick Response Controller should be
de-energized for this period by placing it in the
SERVICE MODE. This is done by pressing the FORCE
SERVICE button twice. To start the system cooling,
press the CLEAR button.
• Room sensors may be left connected on ALL
evaporators. Room sensor must be connected on
the Master Coil.
• A pressure transducer is installed on the evaporator. Do not
leak test system above 150 PSI or damage to transducer
could occur. If leak testing must be greater than 150 psig,
disconnect the transducer from the suction header and
reconnect after testing is complete.
Condensing Unit
Condensing units do not require a Defrost Timer and should
be disconnected if installed. A head pressure control is highly
recommended to be installed in condensing unit.
Condensing unit must be installed using proper refrigeration
practices and codes. Make sure there is sufficient clearances around
unit for adequate air flow and access.
Typical condensing unit wiring is shown on page 31. The wiring
diagram on page 32 shows how to convert a conventional
condensing unit to use Heatcraft Quick Response Controller with the
system.
Evaporator Unit
The evaporator contains the Heatcraft Quick Response Controller
board, electric expansion valve, pressure transducer, distributor,
orifice, transformer and three sensors. These components are all
factory mounted and wired. The three sensors are factory mounted
and provide input to the controller from the following: defrost
temperature, suction temperature, room temperature
Each evaporator unit must be installed using proper refrigeration
practices and codes. Make sure the piping is correctly sized and
properly routed. It is highly recommended that the liquid and suction
lines be insulated. There must also be good clearance around unit.
See H-IM-UC Installation and Operation manual for more details.
(Available on website).
©2018 Heatcraft Worldwide Refrigeration
Summary of Contents for H-IM-QRC
Page 31: ...31 Wiring TYPICAL ELECTRIC DEFROST WIRING DIAGRAM ...
Page 37: ...37 Notes ...
Page 38: ...38 Notes ...
Page 39: ...39 Notes ...