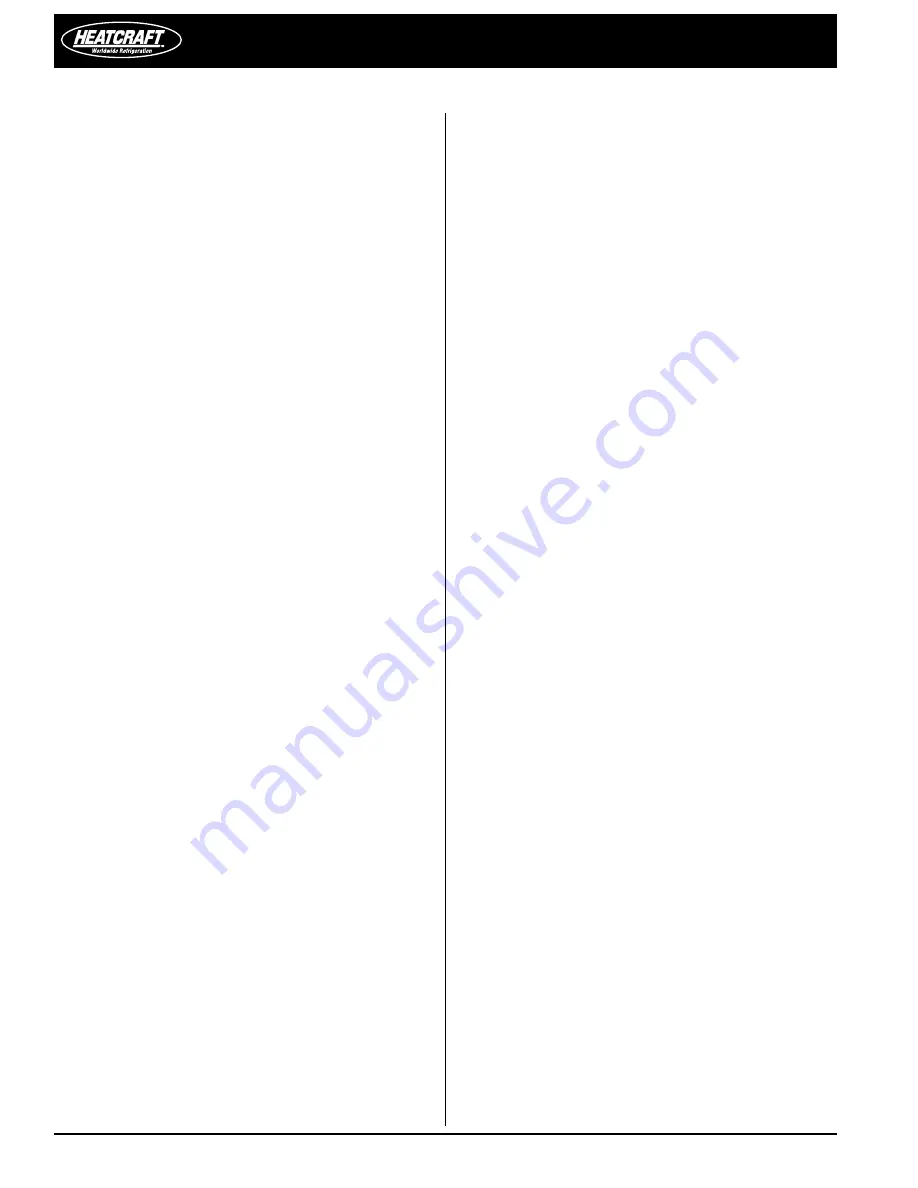
2
Part # 25000102
Table of Contents
Introduction .............................................................................................................. 3
Inspection
Unit Designation
Model Definition
System Warranty ....................................................................................................... 4
Rigging
Location of Equipment - INDOOR
Clearances
Floor & Foundation Requirements
Vibration Mounts
Figure 1. Vibration Pad & Spring Isolator
Figure 2. Vibration Pad Locations
Location of Equipment - OUTDOOR ........................................................................ 5
Ground Mounting
Roof Mounting
Unit Vibration Isolation
Compressor Spring Vibration Isolators
Figure 3. Spring Mount
Unit Access ................................................................................................................ 6
Vertical Clearance
Lateral Clearance
Decorative Fences
Units in Pits
Multiple Units
Ventilation Requirements ........................................................................................ 7
Electrical
Refrigerant Piping
Suction P-Traps
Figure 4. P-Trap requirements
Figure 5. P-Trap construction
Figure 6. Double Suction Risers ............................................................................... 8
Figure 7. Inverted Trap
Refrigerant Line Insulation
Refrigerant Line Support
Figure 8. Pipe Support
Expansion Loops ....................................................................................................... 9
Figure 9. Offsets
Table 1. Expansion Chart
Table 2. Pressure Loss of Liquid Refrigerants ....................................................... 10
Table 3. Equivalent Feet of Pipe
Table 4. Weight of Refrigerants in Copper Lines During Operation ................... 11
Table 5A. Recommended Line Sizes for R-404A and R-507 ................................ 12
Table 5B. Recommended Line Sizes for
R-404A and R-507 (continued) .............................................................. 13
Table 6A. Recommended Line Sizes for R-22 ........................................................ 14
Table 6B. Recommended Line Sizes for R-22 (continued) ................................... 15
Table 7. Recommended Remote Condenser Line Sizes ....................................... 16
Leak Checking, Evacuation, and Start-up ............................................................. 17
Refrigerant Distribution ........................................................................................ 18
Off-Cycle
Electric Defrost
Priority I Hot Gas Defrost
Head Pressure Control System
Electronic Control System ...................................................................................... 19
System Balancing
System Superheat (NOTE: Superheat is not preset at factory)
Evaporator Superheat
Alternative Superheat Method
Compressors ........................................................................................................... 20
Copeland Compressors
Table 8. 3D/4D/6D Solid State Modules
Table 9. Typical Voltage Ranges
Table 10. Unloader Factors
Table 11. Oil Safety Switch ..................................................................................... 21
Table 12. Oil Charges
Approved Copeland Lubricants
Carlyle Compressors
Approved Carlyle Lubricants
Oil Pressure
Table 13. O6D/E Oil Pressure History
Table 14. Oil Safety Switch ..................................................................................... 22
Table 15. Part Load Performance Multipliers
Table 16. Required Differential Pressure
Three-Phase Voltage Monitor
Sight Glass & Moisture Indicator ........................................................................... 23
Figure 10. Sight Glass
Safety Relief Devices
Figure 11. Direct Type Relief Valves
Figure 12. 3-Way Relief Valve
Table 17. Henry Relief Valve Capacity Ratings ..................................................... 24
Table 18. Discharge Piping Table
Series P100 Pressure Control ................................................................................. 25
Figure 13. P100 Pressure Controls
Auto Reset Models
Manual Reset Models
Liquid Level Switch
S-9400 Level Switch Series
Table 19. Level Switch Table
Figure 14. S-9400
S-9400 Operation
Module Replacement ............................................................................................. 26
Figure 15. Module Replacement
Oil Control
Low Pressure Oil System
Figure 16. Low Pressure Oil System
Oil Separators
Table 20. AC&R Models........................................................................................... 27
Temprite Models
Temprite Valve Adjustment
Table 21. Temprite Models
Figure 17. Temprite Oil System
Oil Level Regulators
Table 22. AC&R Model Regulators ......................................................................... 28
Troubleshooting Oil System
Liquid Filter-Driers & Suction Filters
Table 23. Sporlan Valve Company
Table 24. Alco Controls
Suction Filter ........................................................................................................... 29
Compressor Motor Burnout Clean-up Procedure
Sporlan Valve Company
Superior Valve Company ........................................................................................ 30
Table 25. Type F Filter
Table 26. Type DF (for clean-up)
Alco Controls
Table 27. Type AF Filter
Table 28. Type AFD (for clean-up)
Head Pressure Control
Valve Functions
Liquid Drain Control Method ................................................................................. 31
Recommended Valve Settings
Table 29. Pressure Range, Set Point & Change per Turn
Field Adjustment
Hot Gas Bypass Regulator Adjustment
Sporlan Valve Company
Valve Setting and Adjustment
Alco Controls ........................................................................................................... 32
Valve Setting and Adjustment
Control Settings
Table 30. Control settings for R-404A/R-507
Table 31. Control settings for R-22
Low Pressure Switch Setting for RMCC
General Maintenance Schedule............................................................................. 33
SERVICE DIAGNOSIS CHART .............................................................................34-35
Service Record ........................................................................................................ 36
System Reference Data
© 2007 Heatcraft Refrigeration Products LLC
Installation and Operations Manual