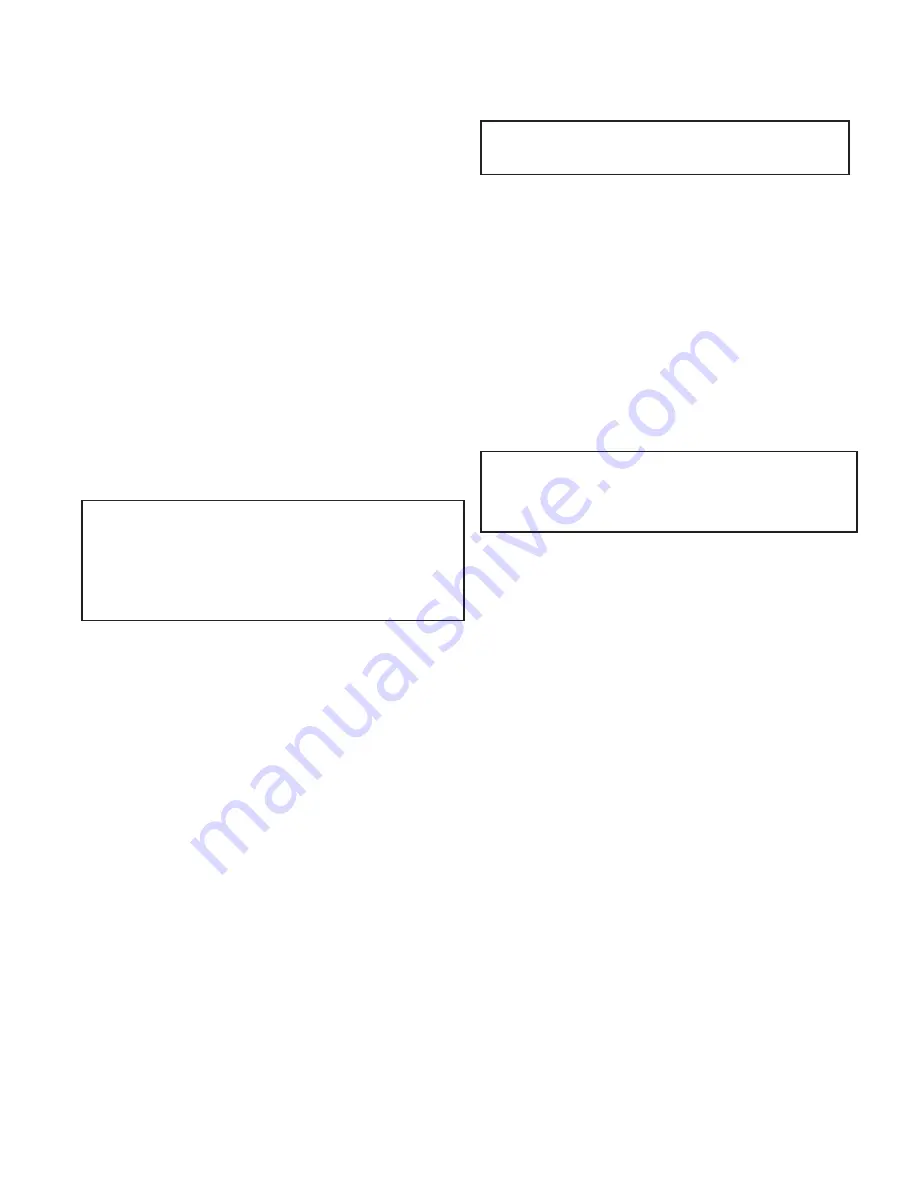
11
Line Insulation
After the final leak test, refrigerant lines exposed to high
ambient conditions should be insulated to reduce heat pickup
and prevent the formation of flash gas in the liquid lines.
Suction lines should be insulated with 3/4" wall Armstrong
“Armaflex” or equal. Liquid lines should be insulated with 1/2
inch wall insulation or better. The insulation located in outdoor
environments should be protected from UV exposure to prevent
deterioration of insulating value.
Leak Testing
After all lines are connected, the entire system must be
leak tested. The complete system should be pressurized
to not more than 150 psig with refrigerant and dry nitrogen (or
dry CO
2
). The use of an electronic type leak detector is highly
recommended because of its greater sensitivity to small leaks.
As a further check it is recommended that this pressure be
held for a minimum of 12 hours and then rechecked. For a
satisfactory installation, the system must be leak tight.
Evacuation and Leak Detection
Due to the smaller molecule size of HFCʼs, they will tend to
leak more readily than CFCʼs. Consequently, it is of the utmost
importance that proper system evacuation and leak detection
procedures be employed.
Copeland recommends a minimum evacuation to 500 microns.
In addition, a vacuum decay test is strongly recommended to
assure there is not a large pressure differential between the
system and vacuum pump. Good evacuation processes include
frequent vacuum pump oil changes and large diameter, short
hose connections to both high and low sides of the system
preferably using bronze braided hose.
Leak detection can be carried out in the conventional manner.
If HCFC or CFC tracer gas is used, care must be taken to
completely remove all traces of the gas prior to introducing
HFCʼs.
Electronic leak detectors are now available that will sense
HFCʼs. This is considered preferable since it removes the
possibility of chlorine remaining in the system after leak testing
with HCFCʼs and/or CFCʼs. There is a view that even small
quantities of chlorine may act as a catalyst encouraging copper
plating and/or corrosion and should therefore be avoided.
WARNING: HFC-134a has been shown to be combus-
tible at pressure as low as 5.5 psig (at
350˚F) when mixed with air at concen
trations more than 60% air by volume. At
lower temperature, higher pressures are
required to support combustion. Therefore,
air should never be mixed with HFC-134a
for leak detection.
Within the last several years, manufacturers have developed
fluorescent dye leak detection systems for use with refrigerants.
These dyes mix with the lubricant and, when exposed to an
ultraviolet light “fluoresce,” indicates the location of leaks.
Copeland has tested and approved the Rigid “System Safe” dye
and found it to be compatible with the compressor materials in
systems.
Evacuation
CAUTION: Do not use the refrigeration compressor
to evacuate the system. Do not start the
compressor while it is in a vacuum.
A good, deep vacuum pump should be connected to both the
low and high side evacuation valves with copper tube or high
vacuum hoses (1/4" ID minimum). If the compressor has service
valves, they should remain closed. A deep vacuum gauge
capable of registering pressure in microns should be attached to
the system for pressure readings.
A shut off valve between the gauge connection and vacuum
pump should be provided to allow the system pressure to be
checked after evacuation. Do not turn off vacuum pump when
connected to an evacuated system before closing shut off valve.
The vacuum pump should be operated until a pressure of 1,500
microns absolute pressure is reached — at which time the
vacuum should be broken with the refrigerant to be used in the
system through a drier until the system pressure rises above
“0” psig.
NOTE: Refrigerant used during evacuation cannot
be vented. Reclaim all used refrigerant.
EPA regulations are constantly being
updated to ensure your procedure follows
correct regulations.
Repeat this operation a second time.
Open the compressor service valves and evacuate the entire
system to 500 microns absolute pressure. Raise the pressure to
2 psig with the refrigerant and remove the vacuum pump.
Summary of Contents for H-IM-FL1A
Page 18: ...18 Control Circuit Wiring Diagram for BACU51 and BACU59 ...
Page 19: ...19 Submittal ...
Page 20: ...20 Submittal ...
Page 22: ...22 Notes ...
Page 23: ...23 Notes ...