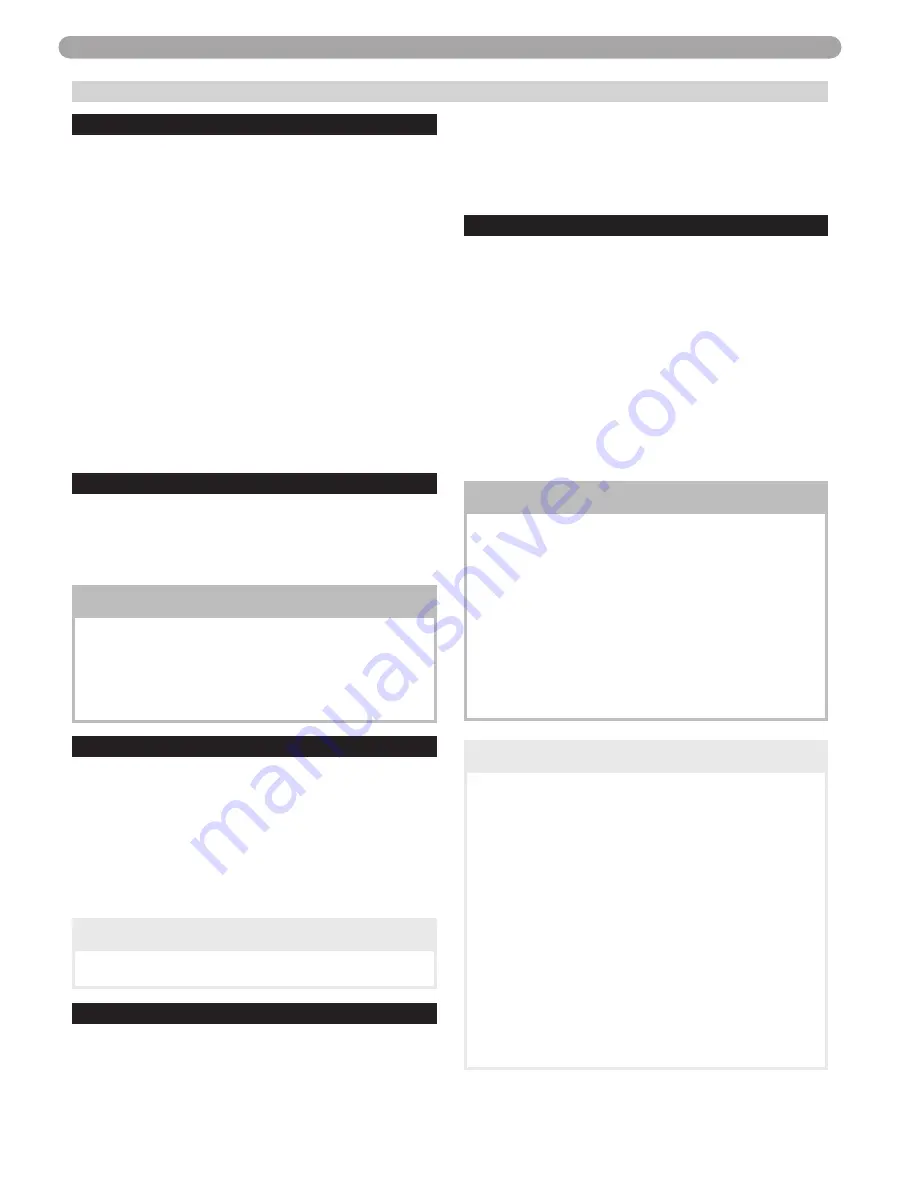
8
GENERAL INFORMATION
GENERAL
1. Munchkin VWH is supplied completely assem-
bled as a packaged boiler. The package should
be inspected for damage upon receipt and any
damage to the unit should be reported to the
shipping company and wholesaler. This boiler
should be stored in a clean, dry area.
2. Carefully read these instructions and be sure to
understand the function of all connections prior
to beginning installation. Contact your Heat
Transfer Products, Inc. Representative or the
Heat Transfer Products, Inc. Customer Service
Department for help in answering questions.
3. This boiler must be installed by a qualified
contractor. The boiler warranty may be voided
if the boiler is not installed correctly.
4. This boiler needs to be installed on a level
floor. This will assure the proper flow to the
condensate drain in the bottom of the boiler.
CODES & REGULATIONS
Installation and repairs are to be performed in strict
accordance with the requirements of state and local
regulating agencies and codes dealing with boiler
and gas appliance installation.
ACCESSIBILITY CLEARANCES
1. The Munchkin VWH is certified for closet
installations with zero clearance to com-
bustible construction. In addition, it is design
certified for use on combustible floors.
2. Refer to Figure 1.1 for the recommended clear-
ance to allow for reasonable access to the boil-
er. Local codes or special conditions may
require greater clearances.
COMBUSTION AND VENTILATION AIR
1. The Munchkin VWH is designed only for oper-
ation with combustion air piped from outside
(sealed combustion). PVC pipe must be sup-
plied between the air inlet connection at the
rear of the boiler through an outside wall.
2. No additional combustion or ventilation air is
required for this appliance.
3. Refer to Section 4 of this manual, Venting, for
specific instructions for piping combustion air.
PLANNING THE LAYOUT
1. Prepare sketches and notes showing the lay-
out of the boiler installation to minimize the
possibility of interferences with new or exist-
ing equipment, piping, venting and wiring.
2. The following sections of this manual should
be reviewed for consideration of limitations
with respect to:
a.
Electrical Wiring: Part 2
b. Gas Connection: Part 3
c.
Venting: Part 4
f.
Piping the Munchkin VWH to the
Storage Tank: Part 5
n
WARNING
Liquefied Petroleum (LP) Gas or Propane is
heavier than air and, in the event of a leak, may
collect in low areas such as basements or floor
drains. The gas may then ignite resulting in a
fire or explosion.
CAUTION
Do not install this boiler on carpeting.
C. PRE-INSTALLATION REQUIREMENTS
n
WARNING
The Munchkin is certified as an indoor
appliance. Do not install the Munchkin
outdoors or locate where it will be
exposed to freezing temperature. This
includes all related piping and
components. If the Munchkin is
subjected to flood water or submersed
in water, the Munchkin must be
replaced.
n
NOTICE
Service clearance of the Munchkin
1. The front of the appliance needs
24" of clearance for service
minimum. It may have a non-rated
or combustible door or access
panel and must have a minimum
of 24" clearance.
2. The left side of the heater is 12"
clearance
3. The right side of the heater is 12"
clearance
4. The top of the heater is 15"
clearance.