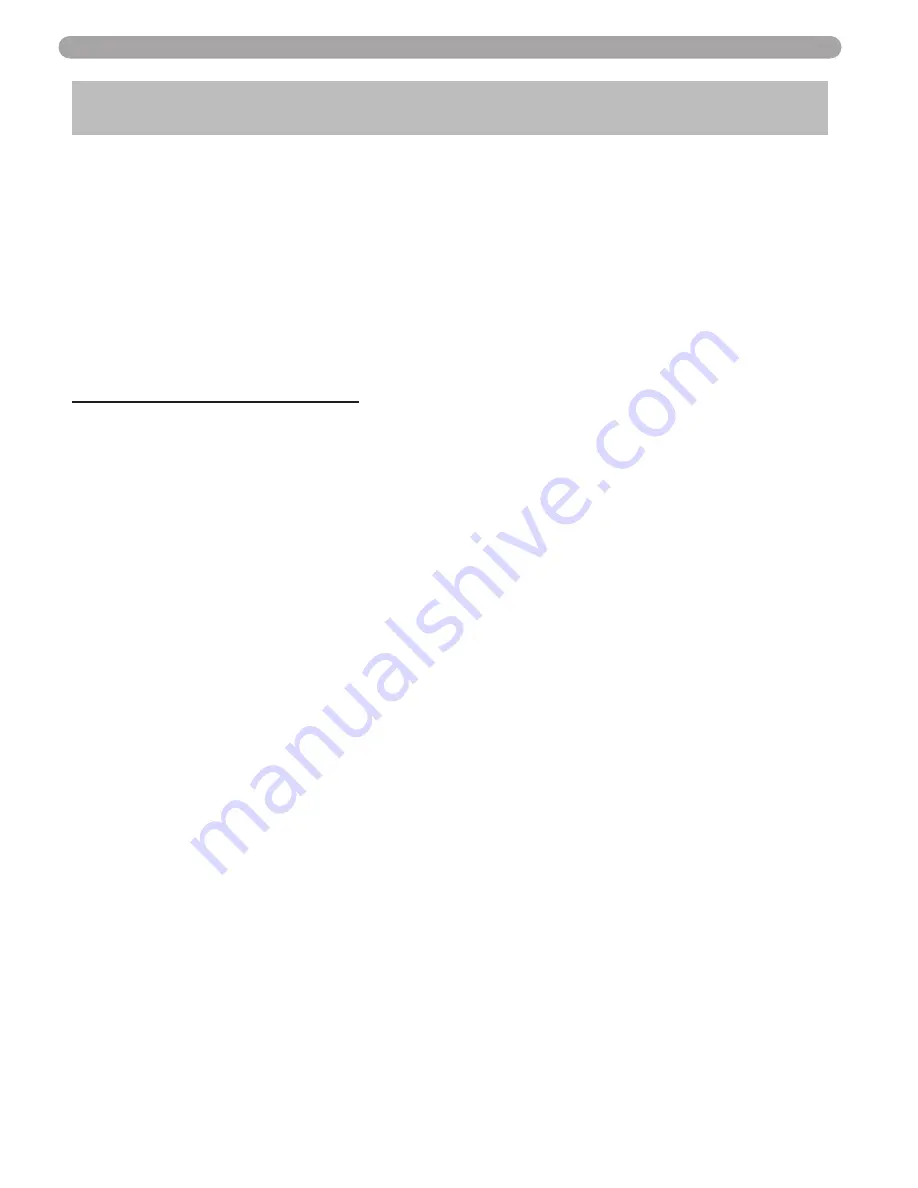
21
VENTING
PART 5: VENTING, COMBUSTION AIR & CONDENSATE REMOVAL
(CONTINUED)
any building.
e. Provide a minimum of 1 foot clearance from the bottom of the exhaust above the expected
snow accumulation level. Snow removal may be necessary to maintain clearance.
f.
Provide 4 feet horizontal clearance from electrical meters, gas meters, gas regulators, relief
equipment, exhaust fans and inlets. In no case shall the exit terminal be above or below the
aforementioned equipment unless the 4 foot horizontal distance is maintained.
g. When adjacent to a public walkway, locate exit terminal at least 7 feet above grade.
h. Do not locate the exhaust directly under roof overhangs to prevent icicles from forming.
i.
Provide 4 feet clearance from the inside corner of vertical walls, chimneys, etc., as well as
horizontal corners created by roof overhangs.
2. Determine air intake vent location.
a. Provide 1 foot clearance from the bottom of the intake air vent and the level of maximum snow
accumulation. Snow removal may be necessary to maintain clearances.
b. Do not locate intake air vent in a parking area where machinery may damage the pipe.
c. When venting with a two pipe system, maximum distance between intake air vent and exhaust
vent is 6 feet (1.8 m). Minimum distance between exhaust vent and intake air vent on single
water heater is 8” (0.2 m) center-to-center. Minimum distance between exhaust vents and
intake air vents on multiple water heaters is 8” (0.2 m) center-to-center.