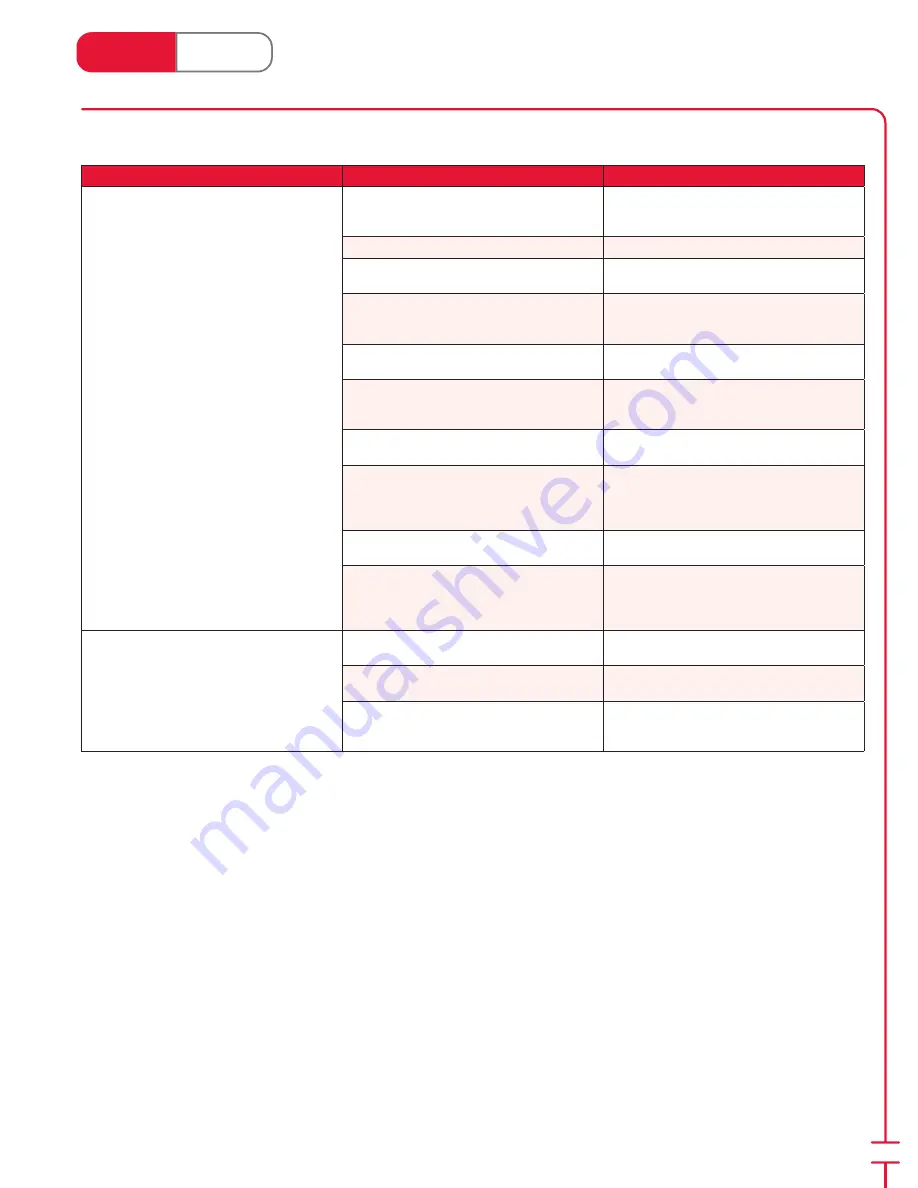
®
Heat
Link
13
www.heatlink.com
TMP040 / TMP070 – 3-Way Mixing Panels
Installation, Operation, and Maintenance
Troubleshooting
Problem
Check / Verify
Possible Cause
Low Temperature Within Room
Misplacement of thermostat location within
room.
Make sure thermostat is not being influenced
by an additional heat source, such as lighting
or air duct.
Low temperature setting of the thermostat.
Adjust the temperature setting on thermostat.
The system fails to turn on if the thermostat is
set to high setting
Thermostat may be out of calibration or
defective. Replace thermostat.
The electronic actuator fails to open during a
call for heat
The electronic actuator may be improperly
seated or may be defective. Replace if
necessary.
Low supply mixed fluid temperature.
Adjust the power box to the appropriate
setting.
Wiring from heat source to panel.
Check that the wiring is done properly. Consult
qualified electrician prior to alteration of wiring
between heat source and panel.
Output of heat source is unable to meet
demand of heating system.
Compare output of heat source to the
requirements of the heating system.
The green LED is not on.
There may be no power being supplied to the
PLC. Consult a qualified electrician to ensure
the PLC is wired correctly. The PLC may be
defective.
Circulator is not on during a call for heat. (Use
a stethoscope or similar device to verify)
The PLC control or circulator may be
defective.
When zone valves are installed outside the
panel a qualified electrician should verify 24V
power is supplied to the thermostats and
actuator.
The 24V transformer may have failed.
High Temperature Within Room
Check current setting of the thermostat.
Adjust the temperature setting on thermostat
to a lower setting.
High supply mixed fluid temperature.
Adjust the Thermostatic Mixing Valve to the
appropriate settings.
Installed electronic actuators remain open
after the thermostat is satisfied.
An obstruction inside the zone valve is not
allowing the actuator to fully close or the
thermostat is still calling for heat.