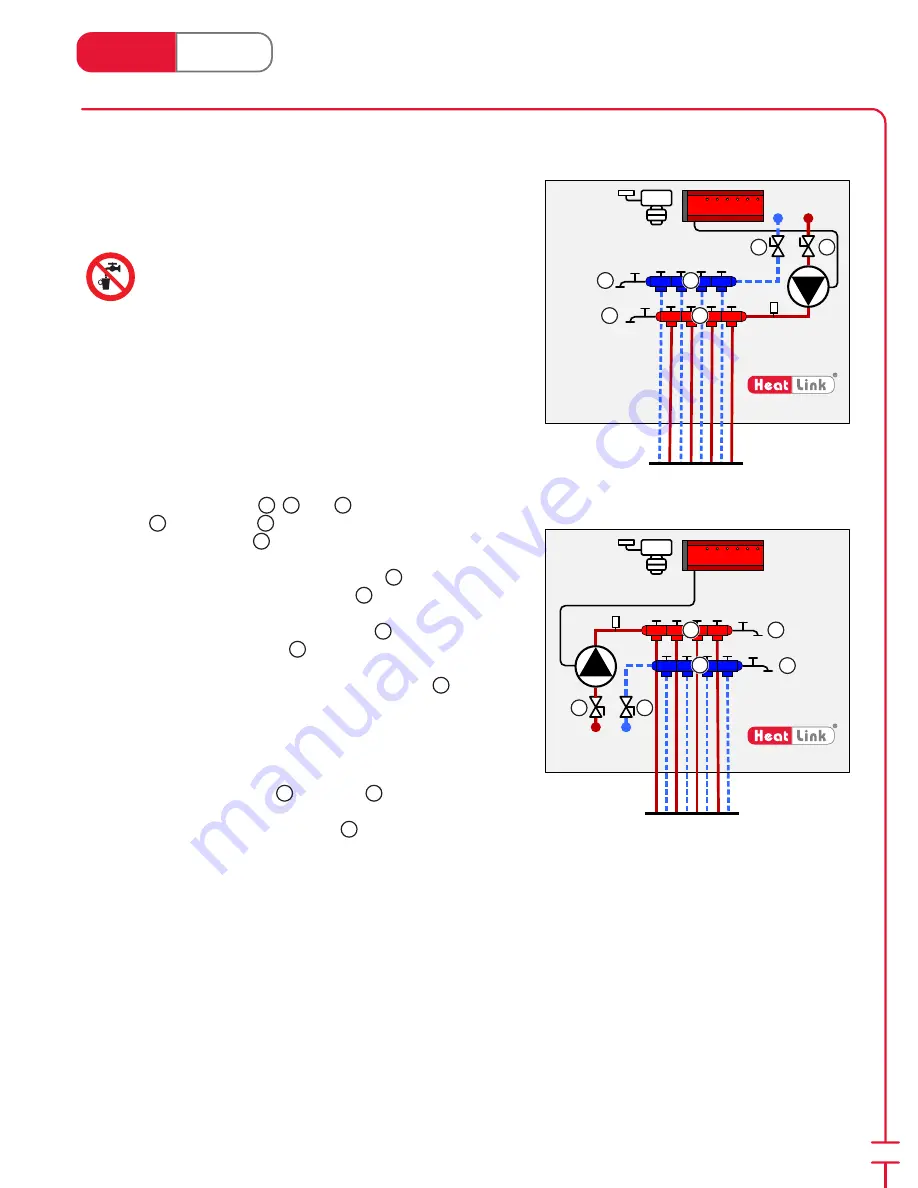
®
Heat
Link
19
www.heatlink.com
SSPxx000x – SS Manifold Pump Panels
Installation, Operation, and Maintenance
SSP Panel
T
SSP Panel
T
Fill And Purge
The following steps are recommended in order to fill the panel
with water and purge entrained air once piping is completed,
and before activation of the panel.
Note:
Additional purging steps may be required for the rest of
the hydronic system.
Note:
Isolation and drain valves are not included with the
panel, but are necessary to properly fill and purge the
panel, and to isolate the panel for service.
Step 1
Ensure the panel is not powered.
Step 2
Fully close valves
A
,
B
, and
C
. Fully close all supply
E
and all return
F
manifold valves.
Fully open valve
D
.
Step 3
Attach a purge hose (not included) to
D
. Pressurize
the main supply line. Open valve
B
.
Step 4
Open the first return manifold valve
F
. Open the first
supply manifold valve
E
. Watch the hose in the pail
until you observe a steady stream of water (no air or
spitting). Close the first return manifold valve
F
.
Step 5
Repeat Step 4 for each loop until all loops are filled
with water, and air is purged from pipes.
Step 6
Purging is complete when there is no more air and/or
spitting. Close valve
D
then valve
B
.
Step 7
Remove hose from drain valve
D
.
Step 8
Check for leaks at connections. If any leaks are found
use a back-up wrench and carefully tighten until leak
stops. Do not overtighten.
The discharged system fluid from the fill and purge
process is not for consumption or washing.
E
F
F
E
A
A
B
B
C
C
D
D
SSTL Series bottom feed
SSTL Series top feed