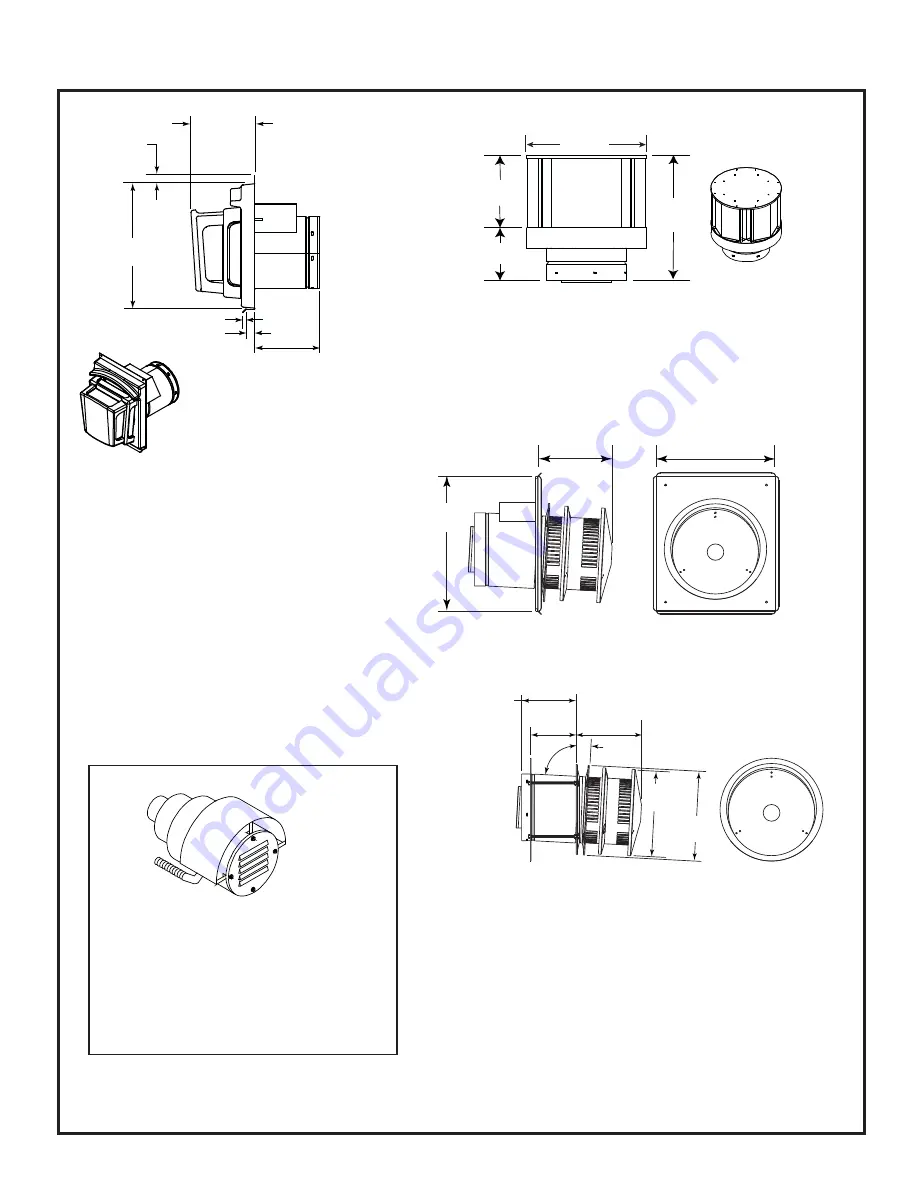
Heat & Glo • RED60 Installation Manual • 2159-980 Rev. D • 11/13
86
A. Vent Components Diagrams (
continued
)
Figure 12.4 DVP vent components
7-1/4 in.
12 in.
305 mm
(184 mm)
5-1/4 in.
(133 mm)
12-1/2 in.
(318 mm)
DVP-TVHW
VerticalTermination Cap (Highwind)
PVK-80
(For use with IPI and DSI appliances only.)
1 in.
(25 mm)
14 in.
(356 mm)
3/8 in. (10 mm)
1 in. (25 mm)
7-1/4 in.
(184 mm)
7-3/4 to 10-3/8 in.
(197 to 264 mm)
DVP-FBHT
FireBrickTermination Cap
13 in.
(330 mm)
15 in.
(381 mm)
8-1/8 in.
(206 mm)
DVP-HRC-SS NOT APPROVED FOR ALL UNITS.
NOT FOR USE WITH LP FUEL
10-7/8 in.
276 mm
10-1/2 in.
267 mm
3°
87°
Effective Length
5-3/4 to 8-3/8 in.
146 to 213 mm
5-1/2 in.
140 mm
8-3/8 in.
213 mm
DVP-HRC-ZC-SS NOT APPROVED FOR ALL UNITS.
NOT FOR USE WITH LP FUEL
NOTE: PVK-80 has specific wiring
and venting requirements for use on
the RED60 model. Refer to Section 7
for installation instructions.