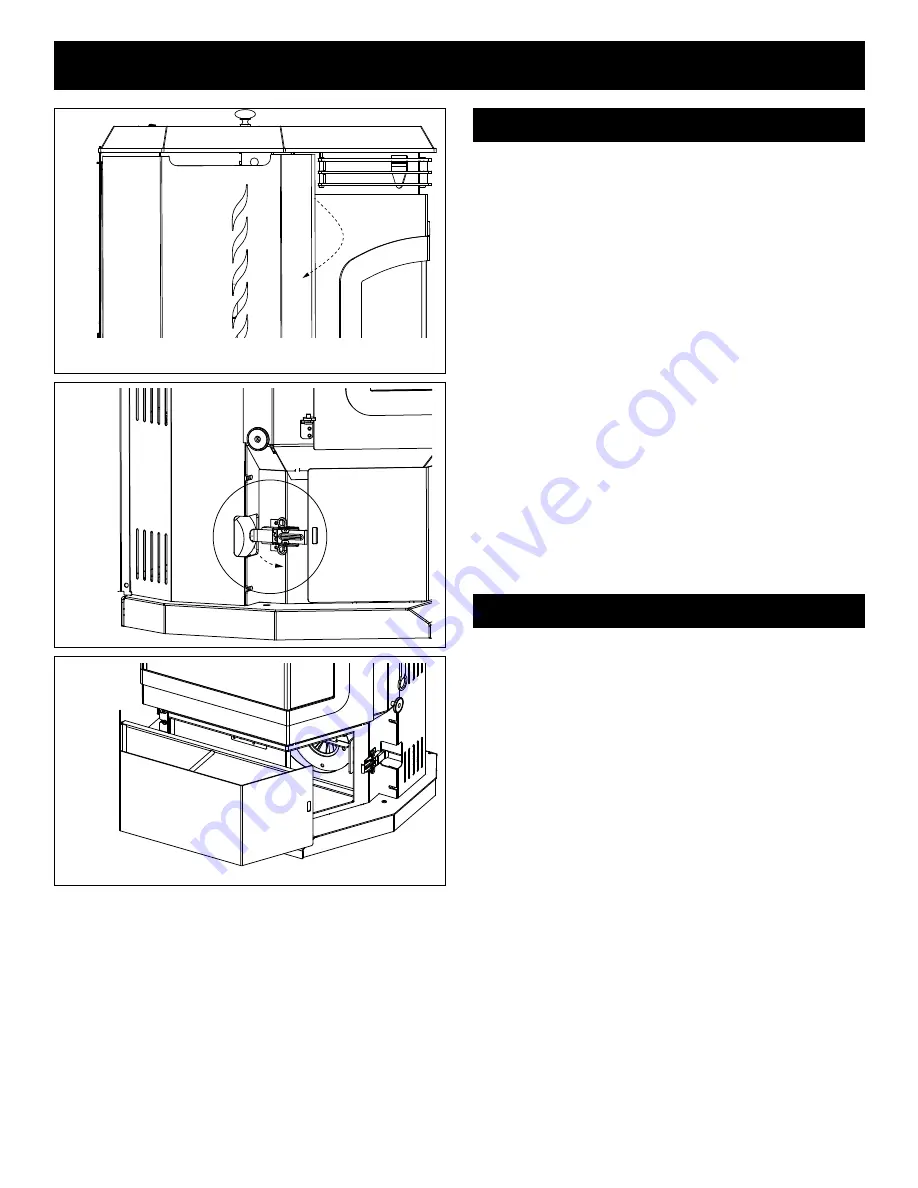
21
1-90-09730R29_02/14
CAuTION: Surfaces are hot while in operation, wear
gloves to protect from burns.
1. Open side doors. Fig. 29
2. Release spring latches on the right and left side of the
ash pan. Fig. 30
3. Slide ash pan forward enough to lift with center handle.
Empty ashes and reinstall ash pan. Fig. 31
disposal of Ashes:
Ashes should be placed in a steel container with a tight
fitting lid. The closed container of ashes should be moved
outdoors immediately and placed on a noncombustible
floor or on the ground, well away from all combustible
materials, pending final disposal. If ashes are disposed
of by burial in soil or otherwise locally dispersed, they
should be retained in the closed container until all
cinders have thoroughly cooled. Other waste shall not
be placed in this container.
4. Inspect the gasket rope located on the back side of the
ash pan for damage. Replace if necessary.
5. Insert spring latch front hooks into the ash pan side slots.
Push both latches to the rear at the same time to latch.
Fig. 29
Fig. 30
Fig. 31
maintenance - Emptying Ashes
Formation and Need For Removal -The products of
combustion will contain small particles of fly ash. The fly ash
will collect in the exhaust venting system and restrict the flow
of the flue gases. Incomplete combustion, such as occurs
during startup, shutdown, or incorrect operation of the room
heater, will lead to some soot formation which will collect in
the exhaust venting system. The exhaust venting system
should be inspected at least once every year to determine if
cleaning is necessary.
When removing the ash pan to empty ashes, you will note a
build up of ash fines behind the ash pan. This space behind
the ash pan was designed to allow the fines to fall out of the
vertical heat exchangers and collect where they are easily
cleaned out, rather than going into the flue pipe where it
would be difficult to clean. These fines should not be allowed
to build up. They may not allow the ash pan to be seated into
its gasket properly.
NOTE: If an extreme amount of force is required to snap
the latch on one or both sides of the ash pan, the area
behind the ash pan should be checked for ash build up.
Ash Pan removal and re-attachment
Soot and Fly Ash
Summary of Contents for Harman
Page 2: ......